For many small to medium-sized machine shops, automated chip handling may seem like an expensive option—a luxury not worth the investment and suitable only for large manufacturers. And as long as there are employees available who can swing a shovel, it may stay on a list of things that can be postponed.
However, a closer look reveals that automated chip handling should be a higher priority. The basic return-on-investment calculation, including the cost of capital and direct labor and higher prices for cleaner chips, may appear to be a close call. But the improved coolant recovery and shop safety that result from automated chip handling are not.
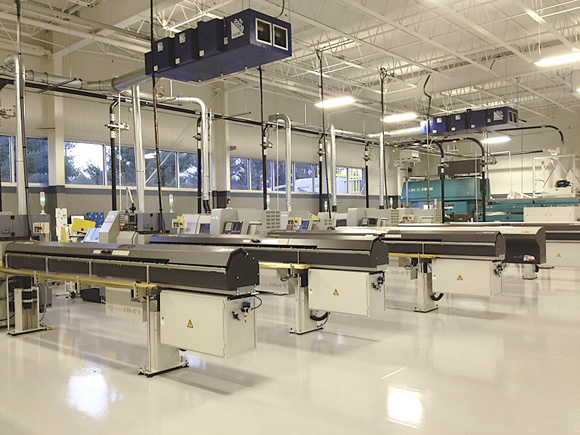
Courtesy of Otis Technology
Bar-fed, Swiss-style CNC machines at Otis Technology once produced an oily mess of chips and fluid before the shop installed an automated collection system. Now, the shop floor is clean and safe. Chips from each of the company’s eight lathes are conveyed to individual hoppers (below), where they are extracted through pipes into a central centrifuge and storage bin.

“If I had six machine tools in a shop, I’d have a conveyor of some kind for safety’s sake alone. Shoveling chips is not healthy,” said Barry Nehls, general manager of the Hydroflow product line for Eriez Manufacturing Co., Erie, Pa.
A related factor that shouldn’t be overlooked is shop morale.
“Keeping morale up—that’s the key,” said Mike Tuttle, operations manager for Otis Technology Inc., Lyons Falls, N.Y. “Everyone likes working in a cleaner, safer shop.”
Otis manufactures gun-cleaning equipment and its processes include turning brass. Before it installed an automated chip-handling system, the company shoveled chips into a hopper, spun them in a centrifuge and then packed them into fertilizer-style bags to load onto the recycling truck.
Otis applies cutting oil when turning, so despite its shovel-and-bag approach to chip recycling, recovery of the expensive oil was important. In addition, an oily, slippery floor strewn with chips was a serious safety hazard. That, combined with the unwelcome task of chip shoveling, was a threat to shop morale, according to Tuttle. Also, the impression the mess left on visitors was unappealing.
Working with chip- and material-handling company PRAB Inc., Kalamazoo, Mich., Otis devised a system, installed in 2010, that solved these issues and that promises a positive return in 5 years. “The biggest part of the investment return is labor savings,” says Tuttle. “We produce about 3,000 pounds of brass chips per week. Every day, it required one full-time employee to collect chips. On Fridays, it required two employees to spin them through the centrifuge and bag them.”
The new PRAB system includes a more effective centrifuge that recovers more oil. In an initial test of the new unit, one of the 1,800-pound polypropylene bags gave up an additional 5 gals. of oil—after having been run through the old centrifuge unit. At $20 per gal. for cutting oil, that’s approximately $10,000 per year in cutting-oil savings alone.
Otis operates eight CNC Swiss-style machines. Chips exit each machine onto a conveyor that dumps them into a funnel-shaped hopper, which, in turn, feeds into a steel vacuum pipe that runs overhead. The unit at each machine turns on for a programmed time, and the vacuuming of chips proceeds down the line of turning machines as one unit is turned off and the next one turned on. Chips flow into a central centrifuge, which reclaims and filters the oil before it is returned to the machines.
From the centrifuge, chips are transferred to a large hopper. When the hopper is full, which usually takes 2 days or so, a proximity switch is tripped and chips are spun out into a silo outside the shop (see photo on page 65). When the silo is filled, a recycler backs a truck under it and chips are augered into the truck, a process that takes about 10 minutes.
Where to Start
Shops considering an automated chip-handling system like the one at Otis Technology might think having a high volume of chips is the key issue, but that is not necessarily the case, according to Neb Perrovic, application engineer for Mayfran International Inc., Cleveland, a provider of scrap and coolant management and material-handling equipment. “When a prospective customer asks us to recommend a system, our first question is about the result they want,” he said. “And that result most often is about extending coolant life and reducing sediment.”
In addition, cleaner coolant dramatically increases tool life and sump pumps require less maintenance, Perrovic said.
The type of coolant a shop uses—including soluble oil, straight oil and synthetics—is a key factor in designing a chip- handling system. For example, if a shop machines steel and the chips are not stringy, Mayfran recommends separation of chips and coolant at the conveyor stage. “The basic need with steel chips is to filter out particles larger than 50µm,” Perrovic said. “We can accomplish that at the conveyor.” In normal steel machining, just providing for a good flow of coolant dripping from the chips while they’re being conveyed can do the job, avoiding the need for a separate filtration unit.
Mayfran recommends several approaches for steel with chips that aren’t stringy: slow the conveyor, allowing more time for coolant to drain; apply a perforated-screen, coolant-saving device at the head of the conveyor; or use a two-belt conveyor system, such as the company’s ConSep 2000, to filter particles larger than 50µm in one step. The ConSep 2000 has a conventional, hinged belt on top and a lower drag conveyor that feeds a rotating, screened drum. Coolant drips through, ready to return to the sump.
Handling cast iron chips is a different story. For greater tool and sump-pump life, Mayfran recommends filtering particles larger than 15µm. That requires additional separation—centrifugal or magnetic—or media filtration.
Eriez, which makes magnetic separation, metal detection and material- handling equipment, offers a combination conveyor and coolant cleaner to handle the job at each machine tool. Magnets attract and hold chips and fines while allowing coolant to drip through.
In most cases, however, filtering coolant must be done after chip conveyance takes place, such as when processing non-ferrous aluminum or the brass chips that Otis Technology has to deal with.
However the chips are transported—in barrels, wheeled hoppers or an automated transport as in Otis’ system—they typically end up in a central processing unit. Otis’s modest-scale chip-management system deals with two high-value items: cutting oil and brass chips. Having a central centrifuge is cost justified even though it is fed by just eight lathes.
The ROI for extensive coolant separation is less certain with steel and iron chips. It depends more on the cost of disposal than on the cost of coolant, and the value of drier chips will vary from one scrap recycler to another. However, high-value chips can change the economics of an automated chip-handling system, making it more attractive for smaller shops.
“We deal a lot in the aerospace industry, where they’re cutting Hastelloy and other high-nickel alloys, as well as titanium,” said Nehls of Eriez. “There’s a lot of value in those chips. And that applies to grinding swarf [containing high-value metals], as well.
“Separating coolant from grinding swarf requires filtering and drying the swarf to make it saleable,” Nehls continued. “We apply squeezers, also known as sludge presses. The wet swarf is placed in a chamber and squeezed dry between plates under high hydraulic pressure. We get the coolant volume down to a percentage, by weight, that’s in the teens. Our users can then sell that dried swarf.”
Coolant-recovery and chip-handling systems can be sized to fit different types of machining operations, according to Nehls. “Gravity-type coolant recovery, which just allows coolant to drip out of the chips, may be appropriate to handle 10 to 20 gallons of coolant per minute. Large central systems that can handle 6,000 or even 10,000 gallons per minute justify high-performance centrifuges. It’s a matter of value: if there is value in the chips, there are systems scaled to handle it.”
Another consideration is whether compacting chips into pucks, or briquettes, after coolant has been extracted can be cost justified. For smaller operations, the answer is, usually, no. Adding value to the chips by compacting and briquetting them is likely to pay off only when a shop is producing thousands of pounds of chips per day.
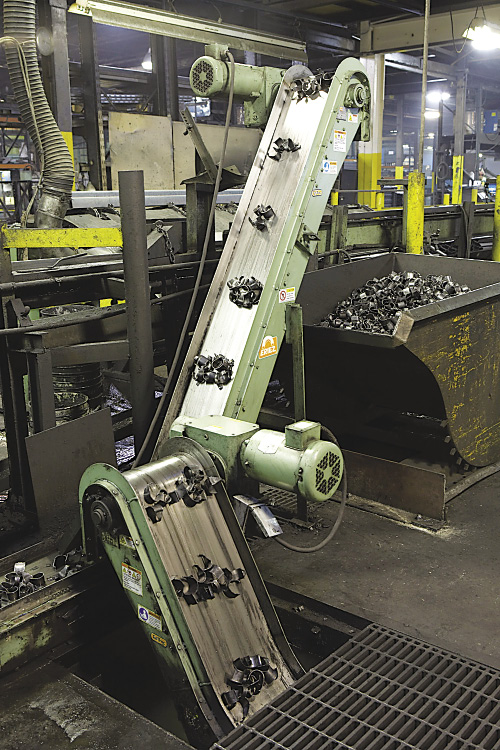
Courtesy of Eriez
Ferrous chips open up handling opportunities for magnets, from separators to magnetic conveyors, such as this one from Eriez.
But, again, the chip material may decide the issue. “The jury is out on puckers,” Nehls said. “Take aluminum, for example. Its low density implies that it should be more valuable when it’s compacted. Often, it is. Scrap dealers vary on the issue of whether they’ll pay more for pucks, but they often do.
“However, unless you get it good and dry, you can wind up encapsulating liquid inside that puck,” he continued. “If you throw them into a melting furnace, they can explode. So, if you’re going to briquette your chips, you also need a good drying system.”
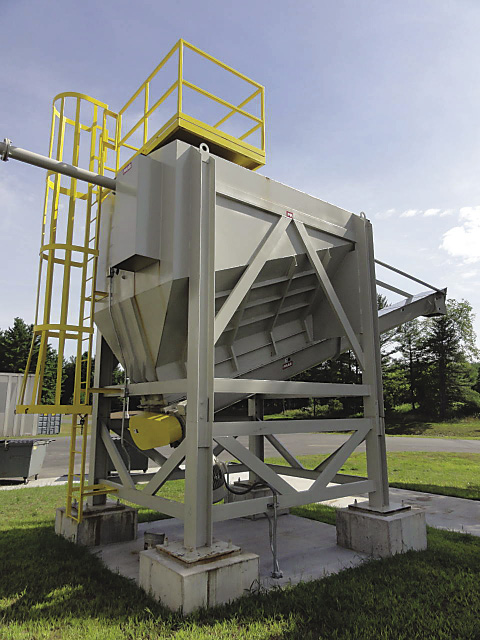
Courtesy of Otis Technology
Otis Technology’s outdoor silo unloads brass chips into a scrap truck in 10 minutes.
According to Ron Chapman of PRAB, its “small” briquetters cost in the neighborhood of $80,000—a cost not likely to be recovered by a small operation.
However, Nehls pointed out that gathering chips from small shops and briquetting them could be a business in itself. “You’d need to gather from a lot of small shops,” he said.
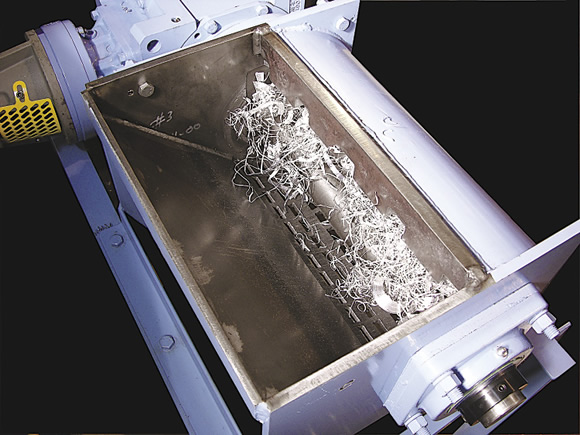
Courtesy of PRAB
Compactors are usually sized for large operations, but there are exceptions. This crusher from PRAB, dedicated to one machine or operated as a standalone unit, can compact 300 lbs. of chips per hour to 1/12 of their original volume.
An Orderly Evaluation
When a small to medium-sized shop is considering an automated chip-handling system, there is no simple formula to determine the number of machines needed or pounds of chips produced for a system to be cost-effective.
However, a shop can determine if an automated system would make sense based on the problems it is trying to solve. For example, a shop operating six machines might want a system to automatically remove chips just to improve shop safety. The criteria used by Otis Technology started with recovering expensive cutting oil, but the system itself also was justified, in part, by shop cleanliness and safety.
Also, when combined with coolant filtration, chip-handling systems can help extend coolant life because advanced filtration can keep coolant viable for a year or two.
The cost of a chip-handling system can range from around $2,000 for an all-purpose chip conveyor, offered as options by all major machine tool builders, to hundreds of thousands of dollars for a large-scale automated one. Scaling a system that works for a small or medium-sized shop is possible, and can pay back in monetary and nonmonetary ways. CTE
Contributors
Eriez Manufacturing Co.
(800) 345-4946
www.eriez.com
Mayfran International Inc.
(440) 461-4100
www.mayfran.com
Otis Technology Inc.
(800) OTISGUN
www.otisgun.com
PRAB Inc.
(800) 968-7722
www.prab.com
Related Glossary Terms
- alloys
alloys
Substances having metallic properties and being composed of two or more chemical elements of which at least one is a metal.
- centrifuge
centrifuge
Filtering device that uses a spinning bowl and the differences in specific gravities of materials to separate one from another. A centrifuge can be used to separate loosely emulsified and free oils from water-diluted metalworking fluid mixes and to remove metalworking fluids from chips.
- computer numerical control ( CNC)
computer numerical control ( CNC)
Microprocessor-based controller dedicated to a machine tool that permits the creation or modification of parts. Programmed numerical control activates the machine’s servos and spindle drives and controls the various machining operations. See DNC, direct numerical control; NC, numerical control.
- coolant
coolant
Fluid that reduces temperature buildup at the tool/workpiece interface during machining. Normally takes the form of a liquid such as soluble or chemical mixtures (semisynthetic, synthetic) but can be pressurized air or other gas. Because of water’s ability to absorb great quantities of heat, it is widely used as a coolant and vehicle for various cutting compounds, with the water-to-compound ratio varying with the machining task. See cutting fluid; semisynthetic cutting fluid; soluble-oil cutting fluid; synthetic cutting fluid.
- grinding
grinding
Machining operation in which material is removed from the workpiece by a powered abrasive wheel, stone, belt, paste, sheet, compound, slurry, etc. Takes various forms: surface grinding (creates flat and/or squared surfaces); cylindrical grinding (for external cylindrical and tapered shapes, fillets, undercuts, etc.); centerless grinding; chamfering; thread and form grinding; tool and cutter grinding; offhand grinding; lapping and polishing (grinding with extremely fine grits to create ultrasmooth surfaces); honing; and disc grinding.
- recovery
recovery
Reduction or removal of workhardening effects, without motion of large-angle grain boundaries.
- straight oil
straight oil
Cutting fluid that contains no water. Produced from mineral, vegetable, marine or petroleum oils, or combinations of these oils.
- swarf
swarf
Metal fines and grinding wheel particles generated during grinding.
- turning
turning
Workpiece is held in a chuck, mounted on a face plate or secured between centers and rotated while a cutting tool, normally a single-point tool, is fed into it along its periphery or across its end or face. Takes the form of straight turning (cutting along the periphery of the workpiece); taper turning (creating a taper); step turning (turning different-size diameters on the same work); chamfering (beveling an edge or shoulder); facing (cutting on an end); turning threads (usually external but can be internal); roughing (high-volume metal removal); and finishing (final light cuts). Performed on lathes, turning centers, chucking machines, automatic screw machines and similar machines.