Ceramic matrix composites are notoriously difficult to machine because of the material’s hardness and nonuniformity, according to Karl Shaw, chief technology officer for IKONICS Corp. He added that laser machining can cause edge damage by remelting CMCs, and waterjet, drilling and other mechanical machining methods tend to cause delamination and fiber pullout and extend internal damage past the hole geometry.
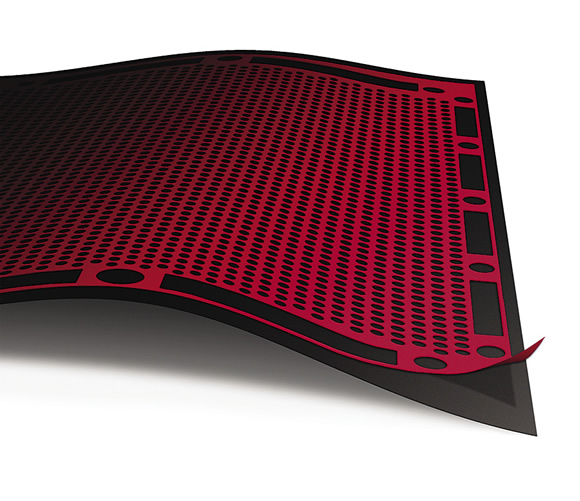
A self-adherent mask is applied to a carbon-based composite.
Searching for a better method, IKONICS developed a new, patent-pending “particle beam” technology that effectively machines CMCs and carbon-based composites without damaging the matrix material, according to the company. IKONICS, working with Laser Technology Inc., recently completed preliminary testing.
IKONICS reported that particle beam technology is a “purposeful evolution” of what has been its core technology since the 1950s. It also reengineers traditional, blast-resistant films to accommodate industrial applications, such as MEMS sensors, ceramics and composites. Laser Technology offers shearographic, holographic and optical testing systems to measure material damage, and can detect variation of surface geometry down to 2nm.
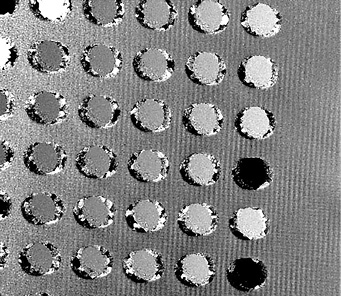
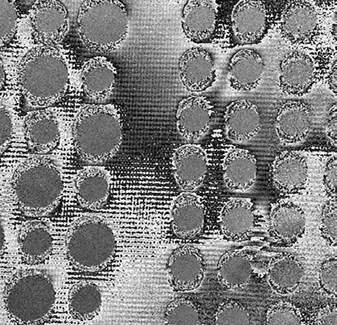
A comparison of 0.2 "-dia. holes in a ceramic matrix composite produced with IKONICS’ particle beam technology (top), showing no burrs, delamination or fiber splintering, and via drilling (two left rows in bottom photo) and waterjet cutting (three right rows in bottom photo).
“We have been able to evolve conventional sand-blasting methods into high-velocity particle beams and configure the beams as multinozzle, CNC axes with a focus to 800µm,” Shaw explained, adding that the multiple beams remain distinct and don’t interact with each other. “The combination of our particle beam technology with our proprietary mask material has allowed machining of very small structures in hard materials.”
Laser Technology President and CEO John Newman added, “After a comparison of the different methods in carbon-based materials, it appears that the IKONICS process produces little damage to the bulk material near machined features.”
After a self-adherent mask is placed on the brittle workpiece material, multiple nozzles directing particles at 500 mph erode material where the mask is open. The process can produce holes as small as 150µm, Shaw noted.
According to Shaw, the combination of the particle beam technology with advanced shearographic, or speckle pattern shearing interferometry, measurement will enable engineers to design finely detailed, reliable composite parts for carbon-based composite and high-temperature CMC applications.
For more information about IKONICS Corp., Duluth, Minn., call (218) 628-2217 or visit www.ikonics.com. For more information about Laser Technology Inc., Norristown, Pa., call (800) 832-4846 or visit www.laserndt.com.
Related Glossary Terms
- ceramics
ceramics
Cutting tool materials based on aluminum oxide and silicon nitride. Ceramic tools can withstand higher cutting speeds than cemented carbide tools when machining hardened steels, cast irons and high-temperature alloys.
- composites
composites
Materials composed of different elements, with one element normally embedded in another, held together by a compatible binder.
- computer numerical control ( CNC)
computer numerical control ( CNC)
Microprocessor-based controller dedicated to a machine tool that permits the creation or modification of parts. Programmed numerical control activates the machine’s servos and spindle drives and controls the various machining operations. See DNC, direct numerical control; NC, numerical control.
- hardness
hardness
Hardness is a measure of the resistance of a material to surface indentation or abrasion. There is no absolute scale for hardness. In order to express hardness quantitatively, each type of test has its own scale, which defines hardness. Indentation hardness obtained through static methods is measured by Brinell, Rockwell, Vickers and Knoop tests. Hardness without indentation is measured by a dynamic method, known as the Scleroscope test.
- laser machining
laser machining
Intensified, pulsed beams of light generated by lasers—typically carbon dioxide or neodium-doped yttrium aluminum garnet (Nd:YAG)—that drill, weld, engrave, mark, slit and caseharden. Usually under CNC, often at both high cutting rates (100 linear in./sec.) and high power (5kW or more). Lasers also are used in conjunction with in-process quality-control monitoring systems allowing measuring accuracies of 0.00001".
- waterjet cutting
waterjet cutting
Fine, high-pressure (up to 50,000 psi or greater), high-velocity jet of water directed by a small nozzle to cut material. Velocity of the stream can exceed twice the speed of sound. Nozzle opening ranges from between 0.004" to 0.016" (0.l0mm to 0.41mm), producing a very narrow kerf. See AWJ, abrasive waterjet.