Similar to multitask machining in the macro world, doing all micromachining operations in one machine enhances part precision and improves production efficiency. New to North America, the standard Model DT-110 Hybrid µEDM from Mikrotools Pte. Ltd. performs sinker EDMing, EDM milling, electrical-discharge grinding (EDGing), turning, milling, drilling and part inspection. Options include attachments for wire EDMing and wire EDGing. According to Mervyn Fathianathan, CEO of Mikrotools, every machine purchased so far has included the optional attachments.
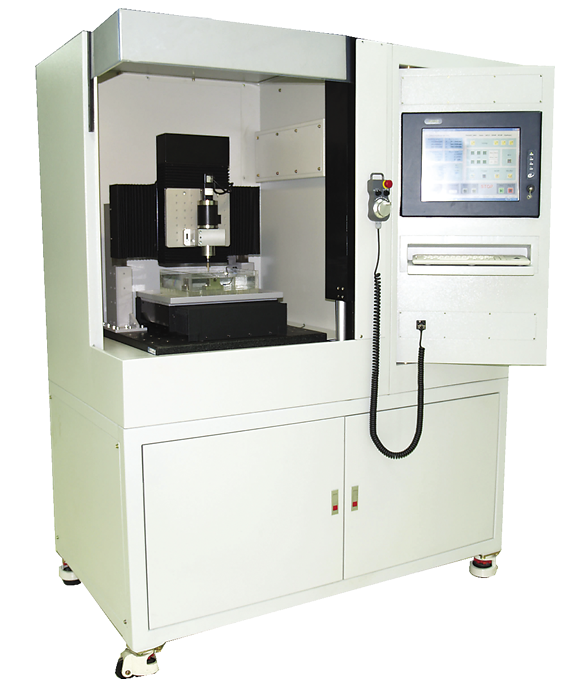
Mikrotools’ Model DT-110 Hybrid µEDM (above) can perform seven machining operations. Below: Users can directly turn electrodes, such as this 19µm-dia. shaft, on the machine with PCD tools.
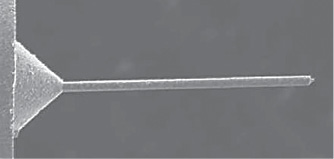
Because the machine has a turning capability, users can produce microelectrodes on the same machine in which they are applied. Fathianathan explained that the patented microturning process reduces the time needed to produce an electrode from hours to minutes.
In addition, turning electrodes on the machine prevents setup errors that can occur when an electrode is fabricated on another machine, according to Fathianathan. “With microturning in place, we can automatically fabricate electrodes, perform the EDM operation and refabricate the electrode without human intervention,” he said.
Fathianathan said the company developed the enhanced microturning technology specifically for on-machine electrode fabrication. “For example, it is very difficult to achieve straight shafts below 70µm in diameter. In many cases, the electrode will either break or start to wobble due to excessive radial cutting forces on the microshaft.”
In addition, Mikrotools developed a process to fabricate ultrasharp PCD tools, via microEDMing, on the machine. “With the ultrasharp tool, we have microturned shafts to less than 20µm,” Fathianathan said.
Although Mikrotools offers an optional 60,000-rpm spindle and users tend to prefer it for running tools with tiny diameters, Fathianathan noted the standard 3,000-rpm spindle can be more effective. This is because the chip load on a microtool’s cutting edge is small when high-speed machining, so the tool ploughs the material instead of cutting it, which imparts a poor surface finish. “Moreover, at high speeds, vibration is very high and that further aggravates the surface finish,” he said. “On the contrary, if the spindle speed is low, chip loading on the cutting edge is reasonable, the vibration level is low and the surface finish is good.”
Mikrotools announced that Global Specialty Machines LLC will distribute the Model DT-110 Hybrid µEDM in the U.S. and Canada. Average lead time for acquiring the machine in North America is 8 to 10 weeks, according to Charles Quillen, executive vice president of Global Specialty Machines. He added that the base machine will sell for about $75,000 less than microEDMs from competing builders.
For more information about Singa-pore-based Mikrotools Pte. Ltd., call +65-6776-9013 or visit www.mi krotools.com. For more information about Global Specialty Machines LLC, Mason, Ohio, call (513) 701-0441 or visit www.globalsmsas.com. CTE
Related Glossary Terms
- electrical-discharge grinding ( EDG)
electrical-discharge grinding ( EDG)
Process similar to conventional electrical-discharge machining except a grinding-wheel type of electrode is used. See EDM, electrical-discharge machining.
- electrical-discharge machining ( EDM)
electrical-discharge machining ( EDM)
Process that vaporizes conductive materials by controlled application of pulsed electrical current that flows between a workpiece and electrode (tool) in a dielectric fluid. Permits machining shapes to tight accuracies without the internal stresses conventional machining often generates. Useful in diemaking.
- gang cutting ( milling)
gang cutting ( milling)
Machining with several cutters mounted on a single arbor, generally for simultaneous cutting.
- grinding
grinding
Machining operation in which material is removed from the workpiece by a powered abrasive wheel, stone, belt, paste, sheet, compound, slurry, etc. Takes various forms: surface grinding (creates flat and/or squared surfaces); cylindrical grinding (for external cylindrical and tapered shapes, fillets, undercuts, etc.); centerless grinding; chamfering; thread and form grinding; tool and cutter grinding; offhand grinding; lapping and polishing (grinding with extremely fine grits to create ultrasmooth surfaces); honing; and disc grinding.
- milling
milling
Machining operation in which metal or other material is removed by applying power to a rotating cutter. In vertical milling, the cutting tool is mounted vertically on the spindle. In horizontal milling, the cutting tool is mounted horizontally, either directly on the spindle or on an arbor. Horizontal milling is further broken down into conventional milling, where the cutter rotates opposite the direction of feed, or “up” into the workpiece; and climb milling, where the cutter rotates in the direction of feed, or “down” into the workpiece. Milling operations include plane or surface milling, endmilling, facemilling, angle milling, form milling and profiling.
- polycrystalline diamond ( PCD)
polycrystalline diamond ( PCD)
Cutting tool material consisting of natural or synthetic diamond crystals bonded together under high pressure at elevated temperatures. PCD is available as a tip brazed to a carbide insert carrier. Used for machining nonferrous alloys and nonmetallic materials at high cutting speeds.
- turning
turning
Workpiece is held in a chuck, mounted on a face plate or secured between centers and rotated while a cutting tool, normally a single-point tool, is fed into it along its periphery or across its end or face. Takes the form of straight turning (cutting along the periphery of the workpiece); taper turning (creating a taper); step turning (turning different-size diameters on the same work); chamfering (beveling an edge or shoulder); facing (cutting on an end); turning threads (usually external but can be internal); roughing (high-volume metal removal); and finishing (final light cuts). Performed on lathes, turning centers, chucking machines, automatic screw machines and similar machines.