END USER: Haas Factory Outlet, (336) 665-1080, www.jeffreysmfg.com.
CHALLENGE: Run at high machining parameters without chatter when demonstrating machine tools.
SOLUTION: A precision collet chuck.
SOLUTION PROVIDERS: FAHRION Vertriebs-GbmH, +49 7184-92-82-0, www.fahrion.de; HORN USA Inc., (888) 818-HORN, www.hornusa.com.
Demonstrating a machine tool’s ability to cost-effectively boost productivity to a potential customer isn’t effective if the cutting tool chatters at high machining parameters. Haas Factory Outlet, a division of Jeffreys Manufacturing Solutions, was experiencing such a scenario when demonstrating Haas machines tooled with conventional collet chucks, according to Ken Potts, director of training and applications for Jeffreys, Franklin, Tenn. The company is a division of Phillips Corp., which owns and operates Haas Factory Outlets in the U.S., China and India. Haas Factory Outlets provide sales and service for machines from Haas Automation, Oxnard, Calif.
He added that chattering wasn’t an issue when running cutting tools with hydraulic and shrink-fit holders, but end users frequently want to avoid the extra cost associated with those toolholding techniques.
While discussing cutting tools during a meeting, Potts recalled that Michael Morgan, a regional sales representative for HORN USA Inc., Franklin, Tenn., presented a CENTRO/P precision collet chuck distributed by HORN and manufactured by FAHRION Vertriebs-GmbH, Kaiserbach, Germany. Potts was immediately impressed. “The holders are visibly amazing,” Potts said, “and you just feel the difference in them.”
However, he found the beauty of these collet chucks isn’t only skin deep. According to FAHRION, the CENTRO/P collets have a maximum accuracy of 2µm and achieve a system accuracy of 3µm at 3 times diameter, 50mm maximum, when matched to its chucks. This is six times the precision of a conventional ER collet chuck, the company added.
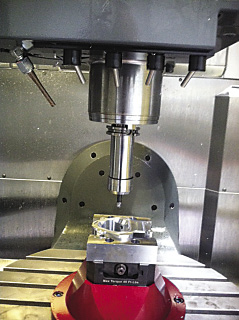
Courtesy of Haas Factory Outlet
A cutting tool clamped in a FAHRION CENTRO/P precision collet chuck machines a part during a Haas machine tool demonstration.
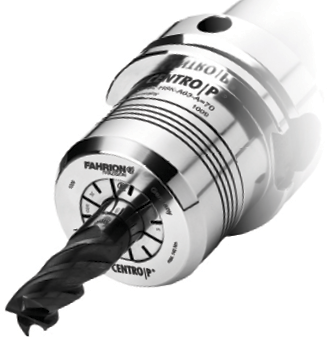
Courtesy of HORN USA
The FAHRION CENTRO/P precision collet chuck from HORN USA achieves a system accuracy of 3µm.
“It’s not just what that collet chuck looks like, but also how it performs,” Potts said. “It doesn’t vary whether you have a short collet chuck or a standard-length one; you get the same accuracy.”
That minimal runout enables an endmill, for example, to machine at a feed rate of up to 400 ipm when clamped in a CENTRO/P collet chuck, whereas the tool would chatter when held with a conventional collet chuck, according to Potts. Minimal runout also enables all cutting edges to equally engage the workpiece material and extend tool life while taking a larger DOC compared to a conventional clamping system, he added. Potts noted he didn’t replace any tools held with the precision clamping system even after machining 150 parts during a 3-day demonstration at a trade show. “The main thing is my cutting tools are lasting a lot longer.”
According to the manufacturer, the chuck offers maximum symmetry with minimum residual imbalance and has a ground 30° trapezoidal thread and special coating on the nut to ensure accurate centering of the nut on the chuck. In addition, the precision collet chucks provide a G2.5 balance at up to 30,000 rpm. Because the CENTRO/P collet sits completely inside the collet closing taper, it does not apply the usual bridging, thereby enabling holding forces twice as high as those of conventional collet chucks, according to the manufacturer.
Since learning about the precision collet chucks 6 months ago, Potts said he has used them in all his recent machine demonstrations. He estimates the clamping system increases productivity about 25 percent.
As a result of the higher machining parameters, longer tool life and finer surface finishes that the CENTRO/P collet chucks provide compared to conventional offerings, Potts said about half of prospective customers consider the tool clamping system after witnessing it in action, with some considering switching from hydraulic and shrink-fit holders to the collet chucks. “Whether it’s a common job shop application or whether it’s getting into the medical or aerospace industry where closer tolerances are needed, they’re definitely looking at these collet chucks.”
Related Glossary Terms
- centering
centering
1. Process of locating the center of a workpiece to be mounted on centers. 2. Process of mounting the workpiece concentric to the machine spindle. See centers.
- chatter
chatter
Condition of vibration involving the machine, workpiece and cutting tool. Once this condition arises, it is often self-sustaining until the problem is corrected. Chatter can be identified when lines or grooves appear at regular intervals in the workpiece. These lines or grooves are caused by the teeth of the cutter as they vibrate in and out of the workpiece and their spacing depends on the frequency of vibration.
- chuck
chuck
Workholding device that affixes to a mill, lathe or drill-press spindle. It holds a tool or workpiece by one end, allowing it to be rotated. May also be fitted to the machine table to hold a workpiece. Two or more adjustable jaws actually hold the tool or part. May be actuated manually, pneumatically, hydraulically or electrically. See collet.
- collet
collet
Flexible-sided device that secures a tool or workpiece. Similar in function to a chuck, but can accommodate only a narrow size range. Typically provides greater gripping force and precision than a chuck. See chuck.
- endmill
endmill
Milling cutter held by its shank that cuts on its periphery and, if so configured, on its free end. Takes a variety of shapes (single- and double-end, roughing, ballnose and cup-end) and sizes (stub, medium, long and extra-long). Also comes with differing numbers of flutes.
- feed
feed
Rate of change of position of the tool as a whole, relative to the workpiece while cutting.
- inches per minute ( ipm)
inches per minute ( ipm)
Value that refers to how far the workpiece or cutter advances linearly in 1 minute, defined as: ipm = ipt 5 number of effective teeth 5 rpm. Also known as the table feed or machine feed.