END USER: Roden's All-Star Machine & Manufacturing Inc., (817) 927-2825, www.rodensallstar.com.
CHALLENGE: Increase machining consistency and reduce setup and changeover times to increase throughput.
SOLUTION: A multiple-pocket, selectable tool body.
SOLUTION PROVIDER: Modern Industries Inc., (814) 455-8061, www.mpwer.com.
Texans are famous for wanting to supersize just about everything, and Roden’s All-Star Machine & Manufacturing Inc. was no exception. The shop made a major commitment to substantially reducing setup and changeover times while increasing throughput.
In 2000, Thomas Roden founded the job shop, which serves the banking, food production, resource extraction, aerospace, automotive and telecommunications industries, among others. The list of workpiece materials includes beryllium copper, Monel, Inconel, titanium, Hiduron, Toughnet, tungsten, tool steel and engineering-grade plastics.
All-Star, which operates out of a 40,000-sq.-ft. facility in Fort Worth, Texas, specializes in handling challenging jobs, such as turning complex parts. The company has grown to 65 people, who operate a variety of machines, including 17 lathes, three multitask machines, 16 machining centers and five EDMs. All-Star’s reputation for meeting demanding requirements has grown with it. Nonetheless, whether it’s a special or regular job, the shop realized it needed to reduce setup and changeover times while enhancing machining consistency to boost throughput and remain competitive while continuing to grow.
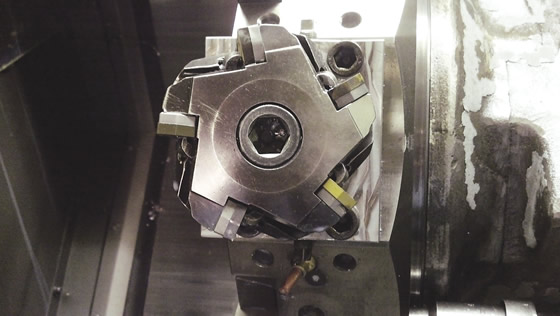
The SpinSelect accepts five indexable inserts.
All-Star was primarily applying shank tools and modular grooving tools, but was leaving money on the table. “Performance was inconsistent and typical changeover and setup times varied from 2 to 6 hours, depending on complexity and tolerances,” Roden said. “Obviously, machines sitting idle for that long are major profit-killers, losing money with every tick of the clock. We couldn’t grow our business by losing out on big chunks of time with machines waiting for the next setups.”
Then the shop heard by word-of-mouth about a new toolholder, or tool body, that held five indexable inserts. Intrigued by the supposed productivity-enhancing claims, All-Star installed one of the SpinSelect multiple-pocket selectable toolholders. Designed with five “stations,” the selectability feature enables quick indexing with a quarter turn of a socket head cap screw. The toolholders are suitable for any lathe that has a turret or tool post.
The SpinSelect product line, which is produced by Modern Industries of Erie, Pa., consists of WNMG, CNMG, VNMG, DNMG, laydown threading tools and Topnotch threading and grooving tools. Also available is a combination head. Modern Industries reports that it has plans to offer more varieties and sizes.
Based on early successes with the tool, such as a 50 to 85 percent decrease in changeover and setup times for most of the lathe parts, All-Star purchased three more tools and expanded their use, Roden noted. The operations include turning (roughing, finishing and profiling), grooving (O-rings, thread relief, thread blocking and profiling) and threading (60° “V,” Acme, stub Acme and API).
“Since we started to use SpinSelect, the ROI benefits and other tangible advantages we’ve realized, including operating improvements versus the standard single toolholders, have been significant,” said Tony Roden, who runs the lathe department and engineering group. “As we cut a full range of materials, from 12L14 to Inconel, our operators have been able to try out the toolholders on the full gamut of metals and have consistently found improved operating performance. These tools increase the versatility of our work cells by providing 20 or more tool geometries at our fingertips, without needing to requalify the tools for new setups.”
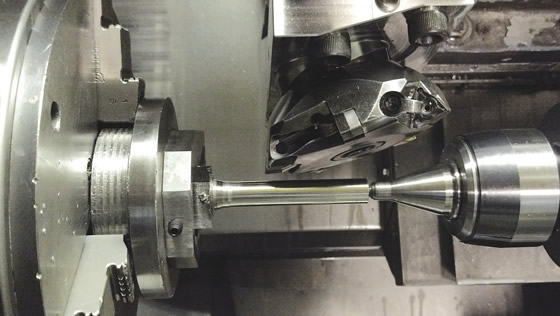
An example of how the SpinSelect tool body from Modern Industries can be oriented to the workpiece.
He added that additional benefits include the ability to take deeper cuts and feed faster with less vibration and chatter. “Increases in operational complexity, such as single chucking, have subsequently decreased the number of operations required to complete a part.”
Tommy Roden explained: “Operators especially like the ability to switch-out roughing inserts virtually on the fly. For example, roughing inserts invariably wear the fastest, so one great thing about SpinSelect is that insert changes take just seconds—not minutes. Plus, offline insert change and reloading can create a virtually continuous runtime.”
He added that by cutting 1 to 3 hours of setup time per project, on average, and eliminating mistakes from extra part handling, All-Star Machine & Manufacturing realized a payback in 6 to 8 weeks per work cell.
Related Glossary Terms
- centers
centers
Cone-shaped pins that support a workpiece by one or two ends during machining. The centers fit into holes drilled in the workpiece ends. Centers that turn with the workpiece are called “live” centers; those that do not are called “dead” centers.
- chatter
chatter
Condition of vibration involving the machine, workpiece and cutting tool. Once this condition arises, it is often self-sustaining until the problem is corrected. Chatter can be identified when lines or grooves appear at regular intervals in the workpiece. These lines or grooves are caused by the teeth of the cutter as they vibrate in and out of the workpiece and their spacing depends on the frequency of vibration.
- feed
feed
Rate of change of position of the tool as a whole, relative to the workpiece while cutting.
- grooving
grooving
Machining grooves and shallow channels. Example: grooving ball-bearing raceways. Typically performed by tools that are capable of light cuts at high feed rates. Imparts high-quality finish.
- lathe
lathe
Turning machine capable of sawing, milling, grinding, gear-cutting, drilling, reaming, boring, threading, facing, chamfering, grooving, knurling, spinning, parting, necking, taper-cutting, and cam- and eccentric-cutting, as well as step- and straight-turning. Comes in a variety of forms, ranging from manual to semiautomatic to fully automatic, with major types being engine lathes, turning and contouring lathes, turret lathes and numerical-control lathes. The engine lathe consists of a headstock and spindle, tailstock, bed, carriage (complete with apron) and cross slides. Features include gear- (speed) and feed-selector levers, toolpost, compound rest, lead screw and reversing lead screw, threading dial and rapid-traverse lever. Special lathe types include through-the-spindle, camshaft and crankshaft, brake drum and rotor, spinning and gun-barrel machines. Toolroom and bench lathes are used for precision work; the former for tool-and-die work and similar tasks, the latter for small workpieces (instruments, watches), normally without a power feed. Models are typically designated according to their “swing,” or the largest-diameter workpiece that can be rotated; bed length, or the distance between centers; and horsepower generated. See turning machine.
- relief
relief
Space provided behind the cutting edges to prevent rubbing. Sometimes called primary relief. Secondary relief provides additional space behind primary relief. Relief on end teeth is axial relief; relief on side teeth is peripheral relief.
- shank
shank
Main body of a tool; the portion of a drill or similar end-held tool that fits into a collet, chuck or similar mounting device.
- threading
threading
Process of both external (e.g., thread milling) and internal (e.g., tapping, thread milling) cutting, turning and rolling of threads into particular material. Standardized specifications are available to determine the desired results of the threading process. Numerous thread-series designations are written for specific applications. Threading often is performed on a lathe. Specifications such as thread height are critical in determining the strength of the threads. The material used is taken into consideration in determining the expected results of any particular application for that threaded piece. In external threading, a calculated depth is required as well as a particular angle to the cut. To perform internal threading, the exact diameter to bore the hole is critical before threading. The threads are distinguished from one another by the amount of tolerance and/or allowance that is specified. See turning.
- toolholder
toolholder
Secures a cutting tool during a machining operation. Basic types include block, cartridge, chuck, collet, fixed, modular, quick-change and rotating.
- turning
turning
Workpiece is held in a chuck, mounted on a face plate or secured between centers and rotated while a cutting tool, normally a single-point tool, is fed into it along its periphery or across its end or face. Takes the form of straight turning (cutting along the periphery of the workpiece); taper turning (creating a taper); step turning (turning different-size diameters on the same work); chamfering (beveling an edge or shoulder); facing (cutting on an end); turning threads (usually external but can be internal); roughing (high-volume metal removal); and finishing (final light cuts). Performed on lathes, turning centers, chucking machines, automatic screw machines and similar machines.