END USER: JM Performance Products Inc., (800) 322-7750, www.jmperformanceproducts.com.
CHALLENGE: Enhance precision and shorten changeover time when machining retention knobs.
SOLUTION: Quick-change collet chucks.
SOLUTION PROVIDER: Hainbuch America Corp., (800) 281-5734, www.hainbuchamerica.com.
Competitive manufacturers continually seek new and innovative ways to improve product quality while cutting costs, and a logical starting point involves methods to increase tool life.
JM Performance Products Inc., Fairport Harbor, Ohio, offers a retention knob that has quickly gained acceptance as a means of extending tool life and improving tool performance. The company, which started as the job shop J&M Machine in 1966, developed a high-torque retention knob that prevents the toolholder taper from expanding, thereby reducing the harmonics responsible for premature tool failure.
“In conventional milling machine operations, 70 percent of the toolholder taper does not contact the spindle,” explained Andrew Rowley, president of JM Performance Products. “This results in an uneven wear pattern capable of causing tolerance problems, as well as (negatively) impacting the tool. The spindle opens and the expanded toolholder becomes lodged, creating the characteristic ‘thump’ frequently heard during tool change. Our design stops the toolholder from expanding so it does not become lodged.”
Since production of the retention knobs began 5 years ago, the line has grown to encompass about 400 different versions for virtually every type of toolholder. The variety offered continues to expand and currently ranges from ¾ " (19.05mm) for a 30 taper holder to 2¾ " (69.85mm) for a 60 taper holder, with a maximum length of 45⁄8 " (117.48mm) for the 60 taper holder, machined from 2¾ "-dia. stock.
The knobs are made from 9310 tool steel or 8620 steel. Plant Manager Craig Fischer noted that 9310 has a higher chromium content and is about 40 percent stronger than 8620. “Everything will eventually be made out of 9310,” he said. The knobs are heat treated and shot peened to enhance rigidity, and most are equipped with coolant holes.
As the number of configurations grew, so did the need for faster changeover times and improved manufacturing capability to maintain precision when cutting materials with a hardness up to 225 HB. This led to a search for better workholding methods.
The company was using 3-jaw chucks with soft jaws, but the workpieces would cause the jaws to wear and reboring the jaws took up about 20 minutes every day—sometimes every 12 hours, Fischer said. “And that’s if you got it right. It took a good setup guy to get the jaws bored right.”
In addition, the company experienced pushback, where the bar stock slides in the collet during machining, when running at the toolmaker’s recommended speeds and feeds. “I couldn’t compensate because sometimes it would slide back 0.050 " and sometimes it would slide back 0.100 ". I don’t have that type of tolerancing in my parts,” Fischer said.
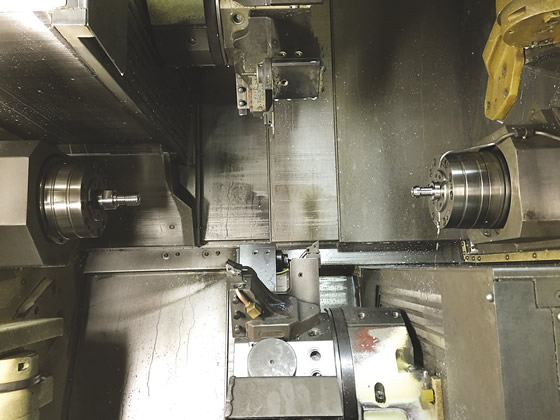
The manufacturing setup at JM Performance Products for a high-torque retention knob (below) involves two opposed Hainbuch chucks mounted in a Mazak turning center, such as this Hyper Quadrex dual-spindle unit. Images courtesy JM Performance Products.
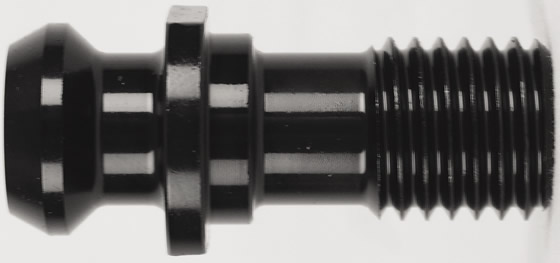
Another issue was a 3:1 ratio on drawback when the diameter varied. “For every 0.001 " we varied on the part diameter, we got a 0.003 " change in length,” he said. The answer was found in collet chucks from Hainbuch America Corp., Germantown, Wis.
“What really impressed us with the Hainbuch chucks is their quick-change capability,” Fischer said. “Our changeover time literally went from 20 minutes to 30 seconds.” He added that it previously took up to 10 minutes to remove the soft jaws to clean the chuck and another 10 to put the jaws back in. With the Hainbuch collet chucks, it takes only 5 seconds each to pull a collet out and replace it, and clearing the fine chips takes a couple minutes.
“Our workholding is now a lot truer in every respect,” Rowley said. “Thanks to the hardened chuck jaws, we’ve reduced wear and runout and have gone from 0.001 " to 0.0004 " tolerances. Also, the Hainbuch collet design results in better gripping and the elimination of pushback.” He added that quick changeover is exceptionally important to JM in that most of its products require 12 operations, four to five of which are machining processes.
Of those machining operations, Fischer noted three—blanking the parts, a secondary operation for producing the heads, and hard turning the knobs—consume the majority of machining time and require use of the collet chucks.
Although Hainbuch offers serrated and rough-surface collet pads as an option, Hainbuch indicated JM Performance Products wouldn’t need them. “We tested it in a Mazak Hyper Quadrex machine with two spindle heads and that bar did not budge when we were running with regular, smooth-surface collet pads,” Fischer said.
Larry McMillan, Great Lakes area regional manager for Hainbuch America, said Hainbuch converted all but two of JM’s machines to the new chucks and plans to outfit those last two machines with a larger model in the near future. “What JM Performance Products wanted to do in terms of changeover and accuracy was precisely what these chucks were invented for.”
Fischer added that the workholders not only improve process accuracy but also extend tool life 40 to 50 percent, because holding the bar stock more firmly minimizes vibration detrimental to the carbide cutting edge. “If you get microfracturing on the edge, it’s just gone,” he said, adding that the company can run high-performance carbide tools at the recommended machining parameters to further improve productivity. “It’s a happy coincidence that the Hainbuch chucks that extend tool life through improved gripping in turning are used to manufacture retention knobs that extend tool life in machining.”
“The retention knob may not be the most glamorous piece of equipment in the shop, and, in many cases, it is overlooked,” Rowley said. “The retention knobs we sell, though, help our customers achieve better tolerances, extend tool life and improve overall performance. In machining, as in many other areas, success is in the details.”
Related Glossary Terms
- Brinell hardness number ( HB)
Brinell hardness number ( HB)
Number related to the applied load (usually, 500 kgf and 3,000 kgf) and to the surface area of the permanent impression made by a 10mm ball indenter. The Brinell hardness number is a calculated value of the applied load (kgf) divided by the surface area of the indentation (mm2). Therefore, the unit of measure of a Brinell hardness number is kgf/mm2, but it is always omitted.
- chuck
chuck
Workholding device that affixes to a mill, lathe or drill-press spindle. It holds a tool or workpiece by one end, allowing it to be rotated. May also be fitted to the machine table to hold a workpiece. Two or more adjustable jaws actually hold the tool or part. May be actuated manually, pneumatically, hydraulically or electrically. See collet.
- collet
collet
Flexible-sided device that secures a tool or workpiece. Similar in function to a chuck, but can accommodate only a narrow size range. Typically provides greater gripping force and precision than a chuck. See chuck.
- conventional milling ( up milling)
conventional milling ( up milling)
Cutter rotation is opposite that of the feed at the point of contact. Chips are cut at minimal thickness at the initial engagement of the cutter’s teeth with the workpiece and increase to a maximum thickness at the end of engagement. See climb milling.
- coolant
coolant
Fluid that reduces temperature buildup at the tool/workpiece interface during machining. Normally takes the form of a liquid such as soluble or chemical mixtures (semisynthetic, synthetic) but can be pressurized air or other gas. Because of water’s ability to absorb great quantities of heat, it is widely used as a coolant and vehicle for various cutting compounds, with the water-to-compound ratio varying with the machining task. See cutting fluid; semisynthetic cutting fluid; soluble-oil cutting fluid; synthetic cutting fluid.
- gang cutting ( milling)
gang cutting ( milling)
Machining with several cutters mounted on a single arbor, generally for simultaneous cutting.
- hard turning
hard turning
Single-point cutting of a workpiece that has a hardness value higher than 45 HRC.
- hardness
hardness
Hardness is a measure of the resistance of a material to surface indentation or abrasion. There is no absolute scale for hardness. In order to express hardness quantitatively, each type of test has its own scale, which defines hardness. Indentation hardness obtained through static methods is measured by Brinell, Rockwell, Vickers and Knoop tests. Hardness without indentation is measured by a dynamic method, known as the Scleroscope test.
- milling
milling
Machining operation in which metal or other material is removed by applying power to a rotating cutter. In vertical milling, the cutting tool is mounted vertically on the spindle. In horizontal milling, the cutting tool is mounted horizontally, either directly on the spindle or on an arbor. Horizontal milling is further broken down into conventional milling, where the cutter rotates opposite the direction of feed, or “up” into the workpiece; and climb milling, where the cutter rotates in the direction of feed, or “down” into the workpiece. Milling operations include plane or surface milling, endmilling, facemilling, angle milling, form milling and profiling.
- milling machine ( mill)
milling machine ( mill)
Runs endmills and arbor-mounted milling cutters. Features include a head with a spindle that drives the cutters; a column, knee and table that provide motion in the three Cartesian axes; and a base that supports the components and houses the cutting-fluid pump and reservoir. The work is mounted on the table and fed into the rotating cutter or endmill to accomplish the milling steps; vertical milling machines also feed endmills into the work by means of a spindle-mounted quill. Models range from small manual machines to big bed-type and duplex mills. All take one of three basic forms: vertical, horizontal or convertible horizontal/vertical. Vertical machines may be knee-type (the table is mounted on a knee that can be elevated) or bed-type (the table is securely supported and only moves horizontally). In general, horizontal machines are bigger and more powerful, while vertical machines are lighter but more versatile and easier to set up and operate.
- tolerance
tolerance
Minimum and maximum amount a workpiece dimension is allowed to vary from a set standard and still be acceptable.
- toolholder
toolholder
Secures a cutting tool during a machining operation. Basic types include block, cartridge, chuck, collet, fixed, modular, quick-change and rotating.
- turning
turning
Workpiece is held in a chuck, mounted on a face plate or secured between centers and rotated while a cutting tool, normally a single-point tool, is fed into it along its periphery or across its end or face. Takes the form of straight turning (cutting along the periphery of the workpiece); taper turning (creating a taper); step turning (turning different-size diameters on the same work); chamfering (beveling an edge or shoulder); facing (cutting on an end); turning threads (usually external but can be internal); roughing (high-volume metal removal); and finishing (final light cuts). Performed on lathes, turning centers, chucking machines, automatic screw machines and similar machines.