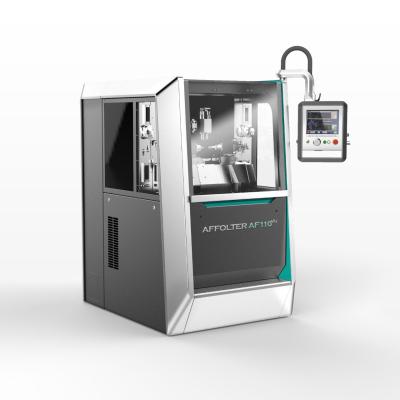
Affolter Technologies SA launches a groundbreaking innovation: worm screw power skiving (WSPS). “This cutting-edge technology was developed by our engineering experts in an intensive R&D process. Worm screw power skiving allows us to finish a high-precision worm in only 6 seconds. If done by worm hobbing, every piece will take 25 seconds”, explains Managing Director Vincent Affolter. In other words: WSPS makes producers four times more efficient. “This will increase the productivity and efficiency of manufacturers in the automotive and aircraft industries considerably.”
Many producers in these industries need to manufacture large quantities of high-precision worms. The WSPS technology focuses on small worms with a module of 0.3 to 1.5. “Such worms are used in car seats or trunks, for instance. We see a big demand in the automotive industry, but also in other sectors”, explains Affolter.
The idea behind the new technology: Unlike in worm hobbing, where the hob turns much faster than the workpiece, the Affolter experts inverted the process. “The workpiece turns extremely fast, with 2 new spindles up to 12’000rpm, while the cutter turns much slower. Only highest quality machines like the Affolter AF100 plus and AF110 plus can reach this speed and at the same time provide the necessary stiffness”, states the Managing Director.
Over the course of the recent months, the Affolter engineers redesigned the well-established Gear Line Model AF110 to optimize the WSPS process. The result is the brand new gear hobbing machine AF110 plus. The workpiece spindles were successfully remodeled to reach the high speeds needed. The Affolter marketing and R&D team also focused on completely redesigning the machine.
“We integrated a cutting fluid filtration system and a chip disposal solution. This allows us to cope with all the requirements imposed by the workpiece up to module 1.5 and the production of large volumes of chips”, says Affolter.
Additionally, the Affolter engineers and the marketing team improved the ergonomics through a redefinition of the machine base and surrounding as well as the human-machine interface. The flexible AF110 plus also convinces with a function that allows to operate at reduced speeds with the hood open (full safety setup machine mode). Extensive test runs proved successful, as Affolter recounts: “We achieved outstanding results processing both steel and brass. The new AF110 plus and the WSPS technology will open completely new opportunities for our customers.”
Contact Details
Related Glossary Terms
- cutting fluid
cutting fluid
Liquid used to improve workpiece machinability, enhance tool life, flush out chips and machining debris, and cool the workpiece and tool. Three basic types are: straight oils; soluble oils, which emulsify in water; and synthetic fluids, which are water-based chemical solutions having no oil. See coolant; semisynthetic cutting fluid; soluble-oil cutting fluid; synthetic cutting fluid.