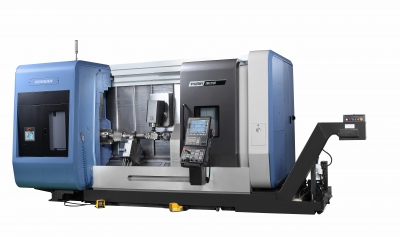
Doosan Machine Tools America offers its latest generation of advanced multi-tasking turning centers: the PUMA SMX series. There are six models in the line, stepped in size and capabilities. Most offer the configuration of equally sized and powered left and right spindles plus a B-axis milling spindle.
According to Dooosan Region Manager Carl Barthelson, current manufacturing trends are exemplified in this new line. “Our customers are requiring machines too have more functionality to increase efficiency, accuracy, and conserve floor space. It’s common that one multi-tasking center can machine all sides of a part in one setup and replace multiple machine tools that have singular functions. Thee PUMA SMX series of machines fulfill all of those needs.”
Barthelson also said that the new line is a reflection of Doosan’s larger product development approach, which is to research customers’ needs and provide solutions, sometimes with specific niche applications in mind. “For example, the new PUMA SMX 3100L model has the new longer 100-inch turning length dimension as a direct result of listening to our customers. Many manufacturers in the aerospace and power generation markets need that extra capacity for their parts. Likewise for the medical industry, several companies in that market liked what we were doing in multi-tasking, but didn’t need such large equipment. So, we now have models that are ideal for medical and other smaller parts.”
In addition to the highlighted Z-axis travel of 100 inches (2,540 mm), other key specifications of the PUMA SMX 3100L include a 4-inch bar capacity and a maximum turning diameter of 26 inches (600 mm) to support the turning of long, large-diameter workpieces. A range of chuck sizes can be accommodated. The main spindle is powered by 40-hp, 3,0000-rpm motors. The Y-axis travel is 11.8 inches (300 mm) and features the B-axis 12,000-rpm milling spindle that has a 0.00001-degree incremental accuracy control function, and programmable C-axes. The Y-axis machining area has been maximized through an orthogonal design structure.
As with all of Doosan’s machine tools, special features and materials have been designed and built-in aimed at high rigidity, accuracy, thermal compensation, and optimal ergonomics. For example, the company uses the finite element method in structural design and minimizes thermal distortion with an oil cooler and an accuracy control feature based on multiple thermal compensation functions. In addition to using robust materials for mass, high rigidity and precision are also achieved through the use of roller-type linear motion components on all guideways. For operator convenience, the SMX machines allow tools to be loaded in the 80-tool magazine from the front, rather than from the side or rear as is typical on other brands. The FANUC 31i-B5 control panel moves from side-to-side, swivels, and its height may be adjusted for the operator’s comfort and preference.
Contact Details
Related Glossary Terms
- chuck
chuck
Workholding device that affixes to a mill, lathe or drill-press spindle. It holds a tool or workpiece by one end, allowing it to be rotated. May also be fitted to the machine table to hold a workpiece. Two or more adjustable jaws actually hold the tool or part. May be actuated manually, pneumatically, hydraulically or electrically. See collet.
- gang cutting ( milling)
gang cutting ( milling)
Machining with several cutters mounted on a single arbor, generally for simultaneous cutting.
- milling
milling
Machining operation in which metal or other material is removed by applying power to a rotating cutter. In vertical milling, the cutting tool is mounted vertically on the spindle. In horizontal milling, the cutting tool is mounted horizontally, either directly on the spindle or on an arbor. Horizontal milling is further broken down into conventional milling, where the cutter rotates opposite the direction of feed, or “up” into the workpiece; and climb milling, where the cutter rotates in the direction of feed, or “down” into the workpiece. Milling operations include plane or surface milling, endmilling, facemilling, angle milling, form milling and profiling.
- turning
turning
Workpiece is held in a chuck, mounted on a face plate or secured between centers and rotated while a cutting tool, normally a single-point tool, is fed into it along its periphery or across its end or face. Takes the form of straight turning (cutting along the periphery of the workpiece); taper turning (creating a taper); step turning (turning different-size diameters on the same work); chamfering (beveling an edge or shoulder); facing (cutting on an end); turning threads (usually external but can be internal); roughing (high-volume metal removal); and finishing (final light cuts). Performed on lathes, turning centers, chucking machines, automatic screw machines and similar machines.