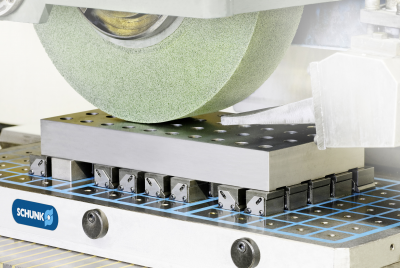
SCHUNK says its MAGNOS parallel pole, square pole, and radial pole plates ensure reliable workpiece clamping, quick workpiece changes, and particularly efficient processes in grinding applications. Among other things, SCHUNK MAGNOS square pole grinding plates boost productivity by up to 200 percent, compared to conventional solutions using parallel-pole technology.
Movable pole extensions make such a difference possible and ensure uniform, deformation-free clamping. These allow all flat workpieces to be ground micron-precise with regard to flatness and parallelism. Multiple grinding operations, repeated changes to the clamping configuration, and time-consuming mounting are no longer necessary with the MAGNOS square pole technology.
The compensating magnetic chucks are equipped with adhesive force regulation as standard to enable individual adjustment of their adhesive force to the workpiece in question. A special magnetic chuck design makes it possible to machine even extra-hardened workpieces, and then effortlessly remove them from the magnetic chuck.
Design features:
- MAGNOS square pole grinding plates fitted with movable pole extensions are ideal for flat grinding of large, thin workpieces with a material thickness of 4 mm or higher.
- Due to the grid size of 32 x 32 mm, small or narrow parts can also be clamped free of deformation.
- If required, the square pole plates can be clamped to already installed parallel pole plates to form a complementary clamping solution
- The monoblock design ensures high stability and rigidity, thus minimizing vibrations and improving the surface finish.
- Additional stops can be installed in the threaded holes located on the side allowing alignment of the workpieces in a matter of seconds.
- The square pole grinding plates are available in 12 standardized sizes, with individual dimensions also possible.
Contact Details
Related Glossary Terms
- chuck
chuck
Workholding device that affixes to a mill, lathe or drill-press spindle. It holds a tool or workpiece by one end, allowing it to be rotated. May also be fitted to the machine table to hold a workpiece. Two or more adjustable jaws actually hold the tool or part. May be actuated manually, pneumatically, hydraulically or electrically. See collet.
- flat ( screw flat)
flat ( screw flat)
Flat surface machined into the shank of a cutting tool for enhanced holding of the tool.
- grinding
grinding
Machining operation in which material is removed from the workpiece by a powered abrasive wheel, stone, belt, paste, sheet, compound, slurry, etc. Takes various forms: surface grinding (creates flat and/or squared surfaces); cylindrical grinding (for external cylindrical and tapered shapes, fillets, undercuts, etc.); centerless grinding; chamfering; thread and form grinding; tool and cutter grinding; offhand grinding; lapping and polishing (grinding with extremely fine grits to create ultrasmooth surfaces); honing; and disc grinding.
- magnetic chuck
magnetic chuck
Workholding device used on surface grinders and milling machines for holding ferrous parts with large, flat sides. Holding power may be provided by permanent magnets or by an electromagnetic system. See chuck.
- parallel
parallel
Strip or block of precision-ground stock used to elevate a workpiece, while keeping it parallel to the worktable, to prevent cutter/table contact.