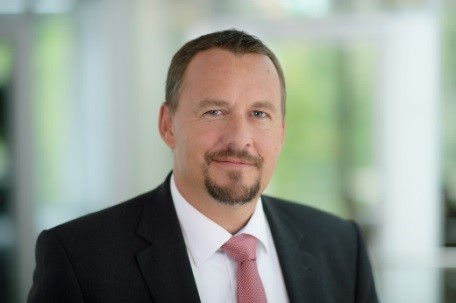
Walter Dunkmann, head of the vacuum automation business area for J. Schmalz GmbH, Glatten, Germany, answers queries about digitization. Schmalz Inc. is located in Raleigh, N.C.
Everybody is talking about digitization. However, it often seems like we are not really making headway. Why is that?
Discussions about digitization have been taking place for a long time at all levels. And although many things are technically feasible and there are numerous solutions on the market, the specific benefits are often not evident to the user. Sweeping promises such as “increased efficiency” or “market growth” are simply not enough. Ultimately, the aim is to analyze the applications together with the customer and to demonstrate the usable advantages of digitization. Providing information on the current status, including performance, system status, projections for component service life or recommendations for subsequent maintenance work are examples. And this is precisely what is lacking to date.
Providing data to the user alone is also not enough. It must be possible to record and transmit data as easily as possible from any location. In the meantime, we equip all our mechatronic components, such as vacuum generators or switches, with near field communication (NFC). This means that the user can read important process or system data directly from the processor of the field device via a smartphone or tablet. In addition, we are designing apps with which our NFC-capable devices are not only readable, but also writable. The devices can then be started up or configured via smartphone. The next step for us would then be to move this data into the cloud. I can then find out how my machine or system at the other end of the world is running regardless of my location or I can compare systems.
I believe there are three features that convince a customer to use a product: The possibility of digitizing the device itself, the connectivity and the usability of the data in the cloud via apps.
Why do companies find it so difficult to show their customers the added value of digitized processes?
Digitization is not an end in itself, but should always be associated with added value for the customer. If the data provided is not prepared and condensed, quality over quantity as the saying goes, it is of no use to the customer. On the contrary, the customer then assumes high costs for data storage, for example. This affects both the hardware and software sides. And even if solutions are available that make the right data available to the user in a meaningful way, the question remains, what is the resulting customer benefit. In other words, what is the customer ultimately willing to pay? Many providers of digitization solutions have not yet achieved the right balance between “effort” and “benefit.” For us at Schmalz, it is important to show exactly what our products do and how they help the customer.
What specific steps is Schmalz taking?
For example, we will demonstrate the “digital version” of predictive maintenance. This does not even require a large infrastructure. Vacuum components used in conjunction with an app and a smartphone provide a wealth of data to further optimize the process, to detect errors at an early stage or to make targeted improvements to the energy consumption of a system.
By using the app as a “control center to go,” the user can install, configure and operate devices via smartphone or tablet. How does the user benefit? If a gripping system or equipment comes to a standstill, the app delivers clear information about the source of the fault, rather than cryptic error codes. The app also allows for predictive wear monitoring to minimize the risk of device failure: Users can set a reminder for predictive maintenance as well as a list of possible wearing parts. This lets users take action quickly if required, thereby reducing service times by up to 80 percent. This is an added value that is measurable for the customer, which only becomes possible through digitization.