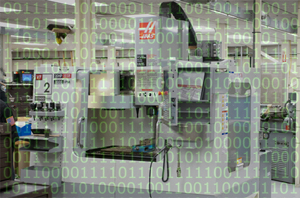
I attended ‘Integr8,’ an Industrial Internet of Things conference hosted by Automation Alley at Detroit’s Renaissance Center last month. At numerous breakout sessions, a common question from participants was, “How do I get started with getting my shop floor connected?”
This was an event full of experts enthused by the possibilities that IIoT hold for manufacturers, so I was pleasantly surprised to hear many of them reply, in effect, with moderation.
“What we’re saying is, don’t sit still, but don’t spend a lot of money yet. Don't try to eat the whole cow. First, run some experiments, figure out what it is that’s valuable to you and your customers in very ‘digestable’ investments,” said Tom Kelly, the executive director and CEO of Automation Alley, Troy, Mich.
“Rather than start with a new CNC machine, start with, say, getting some sensors onto your old machine that can kick data to your mobile phone on weekends and on the second shift. Learn what of this data is useful to you. If it is useless, then learn what kind of sensors will you need to get the useful data," he said. "We don’t want to suggest that the answer is necessarily ‘go buy the big machine.’ The person that does that could go bankrupt while waiting for Industry 4.0 to fully arrive.”
Dennis Hodges, chief information officer at automotive supplier Inteva Products, Troy, Mich., explained that when the company split off from Delphi about 10 years ago, “we realized that if we tried to be like GM or Delphi, we’d probably be bankrupt after the first day. We needed a different model. We realized we needed to be much more manufacturing shop-floor-centric.”
For others getting started, he suggests starting with a question: “The first step is to ask yourself, what is it that keeps you up at night? Which machine or process keeps you up at night with worry or work? That’s the place to start. And if it is already has data coming out of it now, that’s a natural first choice.”
Michael King is president of the Data Analytics & IoT division of LHP Engineering Solutions, Pontiac, Mich. He suggested something like a genba walk approach to getting started:
“One of the important things to do before anything else is to actually walk the shop and talk to your operators,” he said, “because they’re already monitoring the machines today.
"Ask your operators, ‘How do you know when that machine is starting to go, before it actually goes? Or before you see the data? What are you looking at? Is it a sound, for example?’ Some of the experienced operators will say ‘I can hear the spindle going a month before it fails.’ How do we capture that? So you start by gathering that operator knowledge. And then you ask, how do I make that machine information visible? That would be step one.”
Professor Jun Ni, director of the S.M. Wu Manufacturing Research Center at the University of Michigan, said there are two ways to get started. “One is reactive. Find out what’s going on with that process that keeps you up at night and causes trouble, and go to the maintenance records. But there’s also the proactive way.
You can create opportunities just by looking at the data the way a meteorologist uses current data to forecast the weather," Ni added. “Imagine a plant manager—he looks at the schedule and what past data says about it in order to know what to expect. He asks, ‘This week, what will the overall production facility look like—in terms of productive scheduling, in terms of spare parts, of personal?’ Based on the machine data he can proactively optimize production.”
Much more on shop-floor connectivity may be found in my upcoming January feature.
Related Glossary Terms
- computer numerical control ( CNC)
computer numerical control ( CNC)
Microprocessor-based controller dedicated to a machine tool that permits the creation or modification of parts. Programmed numerical control activates the machine’s servos and spindle drives and controls the various machining operations. See DNC, direct numerical control; NC, numerical control.