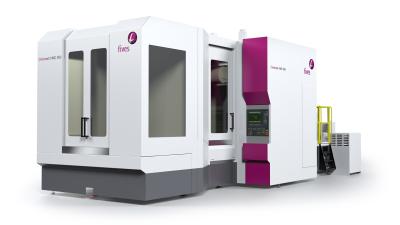
The new Cincinnati HMC 800 is a high-performance HMC solution for demanding aerospace, oil and gas, and other industrial hard metal manufacturing applications that require precision machining. The Cincinnati HMC 800 combines high spindle torque and power with superior dynamic machine stiffness, plus, the dual ball screws provide exceptional feed rates: 45m/min, and acc/dec rates of 0.5G.
The bridge and saddle, designed with enhanced dynamic stiffness, provide optimum finish and tool life in hard metal applications. “The Cincinnati HMC 800 is the perfect solution for the aero or industrial customer who machines hard metal applications, from steel to titanium. The unified structural design allows for fast installation on existing shop foundations,” said Brent Keller, engineering director at Fives Cincinnati. “With the Cincinnati HMC 800, we are targeting those applications where accuracy, rigidity and reliability are priorities.”
The Cincinnati HMC 800 is capable of 5-axis five-sided complex part manufacturing. The 5-axis combines twin ball screw driven axes in XYZ, an infinite contouring B-axis table, and compact u-frame A-axis tilt spindle for full 5-axis contour machining of complex part geometries. All combined, the HMC 800 delivers five-sided machining capability with balanced speed, accuracy and range for complex part manufacturing, with reduced part setups for better quality and lowest cost-per-part.
Keller added, “We designed the Cincinnati HMC 800 with the customer in mind – reliable, hard metal machining, low parasitic time, all at an affordable price.”
Additionally, it is equipped with high-torque spindle options for hard metal processing, 2 speed - 6,000 rpm, and all spindles have external flood up to 250 psi and internal through-spindle coolant up to 1,500 psi (HSK100A/KM4X). Tooling options include: HSK-100A, KM4X100 and Big Plus 50.
Contact Details
Related Glossary Terms
- coolant
coolant
Fluid that reduces temperature buildup at the tool/workpiece interface during machining. Normally takes the form of a liquid such as soluble or chemical mixtures (semisynthetic, synthetic) but can be pressurized air or other gas. Because of water’s ability to absorb great quantities of heat, it is widely used as a coolant and vehicle for various cutting compounds, with the water-to-compound ratio varying with the machining task. See cutting fluid; semisynthetic cutting fluid; soluble-oil cutting fluid; synthetic cutting fluid.
- dynamic stiffness
dynamic stiffness
Measure of a machining system’s ability to dampen vibration from a forced input. If the dynamic stiffness of a system is not sufficient to dampen vibration, chatter occurs. See static stiffness; stiffness.
- feed
feed
Rate of change of position of the tool as a whole, relative to the workpiece while cutting.
- precision machining ( precision measurement)
precision machining ( precision measurement)
Machining and measuring to exacting standards. Four basic considerations are: dimensions, or geometrical characteristics such as lengths, angles and diameters of which the sizes are numerically specified; limits, or the maximum and minimum sizes permissible for a specified dimension; tolerances, or the total permissible variations in size; and allowances, or the prescribed differences in dimensions between mating parts.
- stiffness
stiffness
1. Ability of a material or part to resist elastic deflection. 2. The rate of stress with respect to strain; the greater the stress required to produce a given strain, the stiffer the material is said to be. See dynamic stiffness; static stiffness.