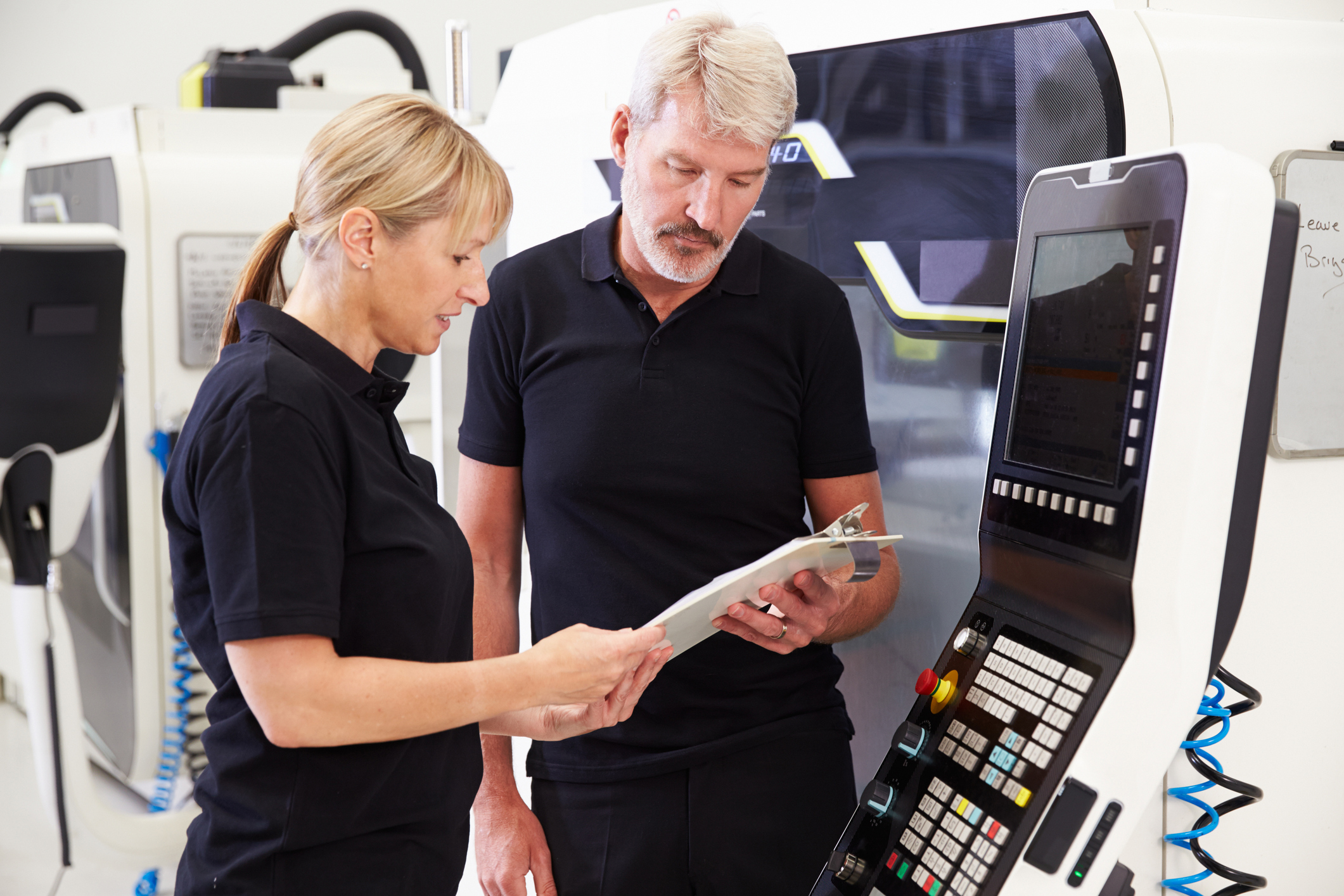
Article from NIMS
The National Institute for Metalworking Skills (NIMS) has launched a new credential to validate an instructor’s or evaluator’s parts inspection skills.
According to Montez King, executive director of NIMS, “Validating skills has become ever more important to employers and, of course, a necessity for educational institutions offering certificate-type training programs in manufacturing technology. For our current customers, this is a refreshing evolution in the certification process.”
Designed for manufacturers and schools, the new “NIMS Inspector Credential” allows a much faster, more efficient performance validation process within the NIMS online structural framework. Until now, shops and schools had to send test parts to be inspected and evaluated by a NIMS-sanctioned review committee of industry volunteers, which guaranteed quality control, but could take up to four weeks or longer, and often created a backlog of uninspected parts. Now, the validation can be done on-site by instructors themselves, and credentials can be issued much quicker.
King said, “The initial feedback from pilots has been very positive and this credential is one of many streamlining activities we’re undertaking at NIMS surrounding our training, testing, validation, and credentialing services. As industry transforms with digital manufacturing technologies, skills training must evolve as well, and that’s what’s happening now in the education sector and at NIMS.”
Related Glossary Terms
- metalworking
metalworking
Any manufacturing process in which metal is processed or machined such that the workpiece is given a new shape. Broadly defined, the term includes processes such as design and layout, heat-treating, material handling and inspection.
- quality assurance ( quality control)
quality assurance ( quality control)
Terms denoting a formal program for monitoring product quality. The denotations are the same, but QC typically connotes a more traditional postmachining inspection system, while QA implies a more comprehensive approach, with emphasis on “total quality,” broad quality principles, statistical process control and other statistical methods.