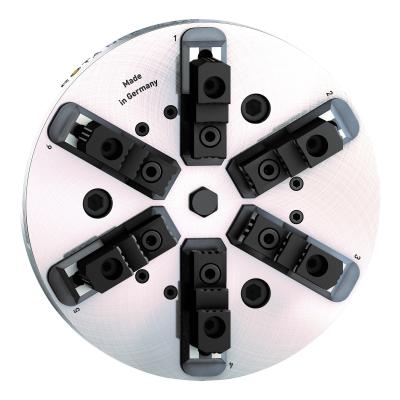
The SCHUNK ROTA NCR-A sealed 6-jaw pendulum compensation chuck has special seals at the jaw interface and the piston to keep the grease from being washed out and the clamping force from being gradually lost. Even in the case of low clamping forces, precise functioning of the chuck is ensured, and at the same time the seals ensure than an ingress of chips and dirt into the chuck body is avoided. As a result, process safety increases, and the maintenance intervals extend. This means that the lathe chuck doesn’t have to be lubricated or cleaned as often.
The SCHUNK ROTA NCR-A consists of a central chuck piston, carrying three inner pendulums aligned at 120°. Each pendulum is connected to two base jaws. This ensures workpiece centering between six contact points, which can be adjusted in pairs.
As the clamping forces are directed towards the chuck, optimal centering is achieved without redundant dimensioning of the workpiece. The chuck with its oscillating jaws perfectly adapts to the workpiece. In case of a conventional jaw clamping, this configuration ensures maximum roundness of the workpieces. Compared to the 3-jaw chuck clamping, this reduces deformation of ring-shaped workpieces by a factor of 10.
For finish machining or clamping of pre-turned surfaces, users can clamp the pendulums of the ROTA NCR-A chuck in center position, and all six jaws can move concentrically. The clamping force between the first and second clamping operation can be varied by the pressure reduction on the clamping cylinder. The rigid chuck body and the long jaw guides ensure a high repeat accuracy and precise machining results.
Due to the flat chuck design, there is plenty of space in a machine room for the workpiece and the machining process. Instead of using costly system jaws or special solutions, standard jaws from SCHUNK can be used on the jaw interface of the ROTA NCR-A. This saves cost and time-consuming special designs, increases flexibility, and reduces setup effort.
The SCHUNK ROTA NCR-A is available in sizes from 190 mm to 1,000 mm in diameter with maximum clamping forces between 36 kN and 300 kN, and jaw strokes from 6 mm to 25 mm. The power lathe chucks of sizes 190 to 225 are equipped with tongue and groove; from size 250 it is equipped with a versatile fine serration (1.5 mm x 60° or 1/16'' x 90°). From size 630 on, the lathe chuck is prepared for the use on vertical lathes. Depending on the chuck size, the pendular compensation amounts between ±1 mm and ±6 mm, and the maximum speed is 600 rpm to 4,000 rpm.
Contact Details
Related Glossary Terms
- centering
centering
1. Process of locating the center of a workpiece to be mounted on centers. 2. Process of mounting the workpiece concentric to the machine spindle. See centers.
- chuck
chuck
Workholding device that affixes to a mill, lathe or drill-press spindle. It holds a tool or workpiece by one end, allowing it to be rotated. May also be fitted to the machine table to hold a workpiece. Two or more adjustable jaws actually hold the tool or part. May be actuated manually, pneumatically, hydraulically or electrically. See collet.
- flat ( screw flat)
flat ( screw flat)
Flat surface machined into the shank of a cutting tool for enhanced holding of the tool.
- lathe
lathe
Turning machine capable of sawing, milling, grinding, gear-cutting, drilling, reaming, boring, threading, facing, chamfering, grooving, knurling, spinning, parting, necking, taper-cutting, and cam- and eccentric-cutting, as well as step- and straight-turning. Comes in a variety of forms, ranging from manual to semiautomatic to fully automatic, with major types being engine lathes, turning and contouring lathes, turret lathes and numerical-control lathes. The engine lathe consists of a headstock and spindle, tailstock, bed, carriage (complete with apron) and cross slides. Features include gear- (speed) and feed-selector levers, toolpost, compound rest, lead screw and reversing lead screw, threading dial and rapid-traverse lever. Special lathe types include through-the-spindle, camshaft and crankshaft, brake drum and rotor, spinning and gun-barrel machines. Toolroom and bench lathes are used for precision work; the former for tool-and-die work and similar tasks, the latter for small workpieces (instruments, watches), normally without a power feed. Models are typically designated according to their “swing,” or the largest-diameter workpiece that can be rotated; bed length, or the distance between centers; and horsepower generated. See turning machine.