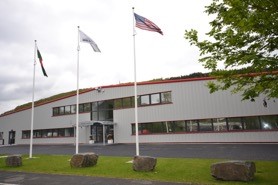
March 5, 2020 - Wall Colmonoy celebrates its golden anniversary of 50 years of making metals work harder in Pontardawe, Wales. Wall Colmonoy, a family-owned and operated organization with facilities throughout the U.S. and U.K., is a global leader in materials engineering the aerospace, automotive, glass, oil and gas, mining, energy and other industrial sectors. The U.K. company exports over 80% of its products into the Eurozone, Scandinavia, South Africa, Russia, Middle East and India.
Wall Colmonoy began its European footprint in 1952, first as a sales office and distribution center in London, importing products from Wall Colmonoy Canada. As the company grew and a need for local manufacturing became apparent, alloy manufacturing began in Motherwell, Scotland, before transferring to a larger facility in Brackley, England.
Due to continued and rapid growth in the U.K. and European markets, William P. Clark Sr., group chairman, accepted an offer by the Welsh government, in 1969, to establish its European headquarters in Pontardawe, Wales and build a larger facility to fulfill growing demand.
Clark was attracted to the region’s 200-year metallurgical history, the available skilled workforce, highly qualified graduates from the local universities and the close proximity to a major metal supplier, Inco (now known as Vale) in Clydach.
Over the half-century, Wall Colmonoy has increased capacity of the Pontardawe facility from 33,000 to 70,000 sq. ft., opening a 23,500 sq. ft. advanced machine shop to support its casting manufacturing facility in 2012. Today, its workforce continues to grow, with 215 employees; a quarter of whom have been with the company for more than a decade.
In 2015, Wall Colmonoy launched a tailor-made apprenticeship program to train and develop a new generation of engineers. There has also been a concentration on developing employees through an active learning culture, while sponsoring employees in their pursuits of further education; ensuring the business develops employees’ skills to meet its future needs.
Bill Clark, chairman and CEO, explains: “Wall Colmonoy is proud to be in Wales. We have been there for 50 years and plan to be there for many, many more years. We are growing and look to the local community and universities to build our expanding business.”
Not only does the company invest heavily in its people, but investment has extended to its manufacturing and engineering facilities. Recently, the company invested nearly £500,000 in its R&D laboratory. State-of-the-art analytical equipment has been introduced making it one of the best-equipped laboratories in the U.K., aimed at product development, technical support and advancement.
In addition to the high-tech lab, Wall Colmonoy implemented new technologies in powder processing, automated brazing paste mixing, which its engineers designed and developed; and 3D printing. This has aided and propelled the development of Colmonoy, Wallex and Nicrobraz products; the launch of ColWear, the company's vacuum-fused wear plates, and entrances into the dental industry and additive manufacturing.
Within Precision Components, Wall Colmonoy is working jointly with local academia to embrace Industry 4.0, by modernizing casting equipment and automation techniques through collaborative robots. For rapid prototyping of parts, the team deploys 3D-printed investment patterns and tooling. In addition, the company procured a 5-axis CNC milling machine, new Mazak twin-spindle CNC lathes, and expanded a turning cell to grow capacity and offerings.
Managing Director Rob Davies discusses the developments: “It’s an exciting time, where the landscape of manufacturing is changing, and our team is adapting daily. We have the drive, the knowledge and the backing to thrive into our next half-century.”
Wall Colmonoy plans to celebrate this milestone with employees, local government officials, customers and suppliers later this year.
Related Glossary Terms
- backing
backing
1. Flexible portion of a bandsaw blade. 2. Support material behind the cutting edge of a tool. 3. Base material for coated abrasives.
- computer numerical control ( CNC)
computer numerical control ( CNC)
Microprocessor-based controller dedicated to a machine tool that permits the creation or modification of parts. Programmed numerical control activates the machine’s servos and spindle drives and controls the various machining operations. See DNC, direct numerical control; NC, numerical control.
- gang cutting ( milling)
gang cutting ( milling)
Machining with several cutters mounted on a single arbor, generally for simultaneous cutting.
- lapping compound( powder)
lapping compound( powder)
Light, abrasive material used for finishing a surface.
- milling
milling
Machining operation in which metal or other material is removed by applying power to a rotating cutter. In vertical milling, the cutting tool is mounted vertically on the spindle. In horizontal milling, the cutting tool is mounted horizontally, either directly on the spindle or on an arbor. Horizontal milling is further broken down into conventional milling, where the cutter rotates opposite the direction of feed, or “up” into the workpiece; and climb milling, where the cutter rotates in the direction of feed, or “down” into the workpiece. Milling operations include plane or surface milling, endmilling, facemilling, angle milling, form milling and profiling.
- milling machine ( mill)
milling machine ( mill)
Runs endmills and arbor-mounted milling cutters. Features include a head with a spindle that drives the cutters; a column, knee and table that provide motion in the three Cartesian axes; and a base that supports the components and houses the cutting-fluid pump and reservoir. The work is mounted on the table and fed into the rotating cutter or endmill to accomplish the milling steps; vertical milling machines also feed endmills into the work by means of a spindle-mounted quill. Models range from small manual machines to big bed-type and duplex mills. All take one of three basic forms: vertical, horizontal or convertible horizontal/vertical. Vertical machines may be knee-type (the table is mounted on a knee that can be elevated) or bed-type (the table is securely supported and only moves horizontally). In general, horizontal machines are bigger and more powerful, while vertical machines are lighter but more versatile and easier to set up and operate.
- turning
turning
Workpiece is held in a chuck, mounted on a face plate or secured between centers and rotated while a cutting tool, normally a single-point tool, is fed into it along its periphery or across its end or face. Takes the form of straight turning (cutting along the periphery of the workpiece); taper turning (creating a taper); step turning (turning different-size diameters on the same work); chamfering (beveling an edge or shoulder); facing (cutting on an end); turning threads (usually external but can be internal); roughing (high-volume metal removal); and finishing (final light cuts). Performed on lathes, turning centers, chucking machines, automatic screw machines and similar machines.