Demand for machined aerospace parts and components is skyrocketing. With private enterprises entering the aerospace travel and exploration marketplace, the industry is growing exponentially. Statistics show that revenue generated by the global space industry may increase to more than $1 trillion by 2040. This requires engineers to design processes to manufacture the high-quality, high-tolerance parts and components that will build this future.
In the aerospace industry, precision and quality already are of utmost importance. Manufacturers must meet tight specifications for parts, including precise edge breaks and finishes. Such specs are designed so the final product has the appropriate aerodynamics to safely perform to rigorous standards. Parts held to this expectation include blisks, turbine blades and turbine discs, as well as housing components, such as aircraft and rocket bodies. These parts play critical roles in balance and drag. Missing the mark on quality here could cost the manufacturer upward of hundreds of thousands of dollars in scrap.
If you’re in the industry, you know: This is not a one-off occurrence for aerospace manufacturers. There are too many opportunities throughout production for mistakes, mishandling and neglect to happen for scrap to be considered uncommon and unexpected. Aerospace parts in particular are often large and complex. Even if they’re small, they typically are complicated. And they frequently are moved off the CNC machine for hand deburring, with large parts calling for heavy equipment to flip them for deburring and finishing one side and then the other.
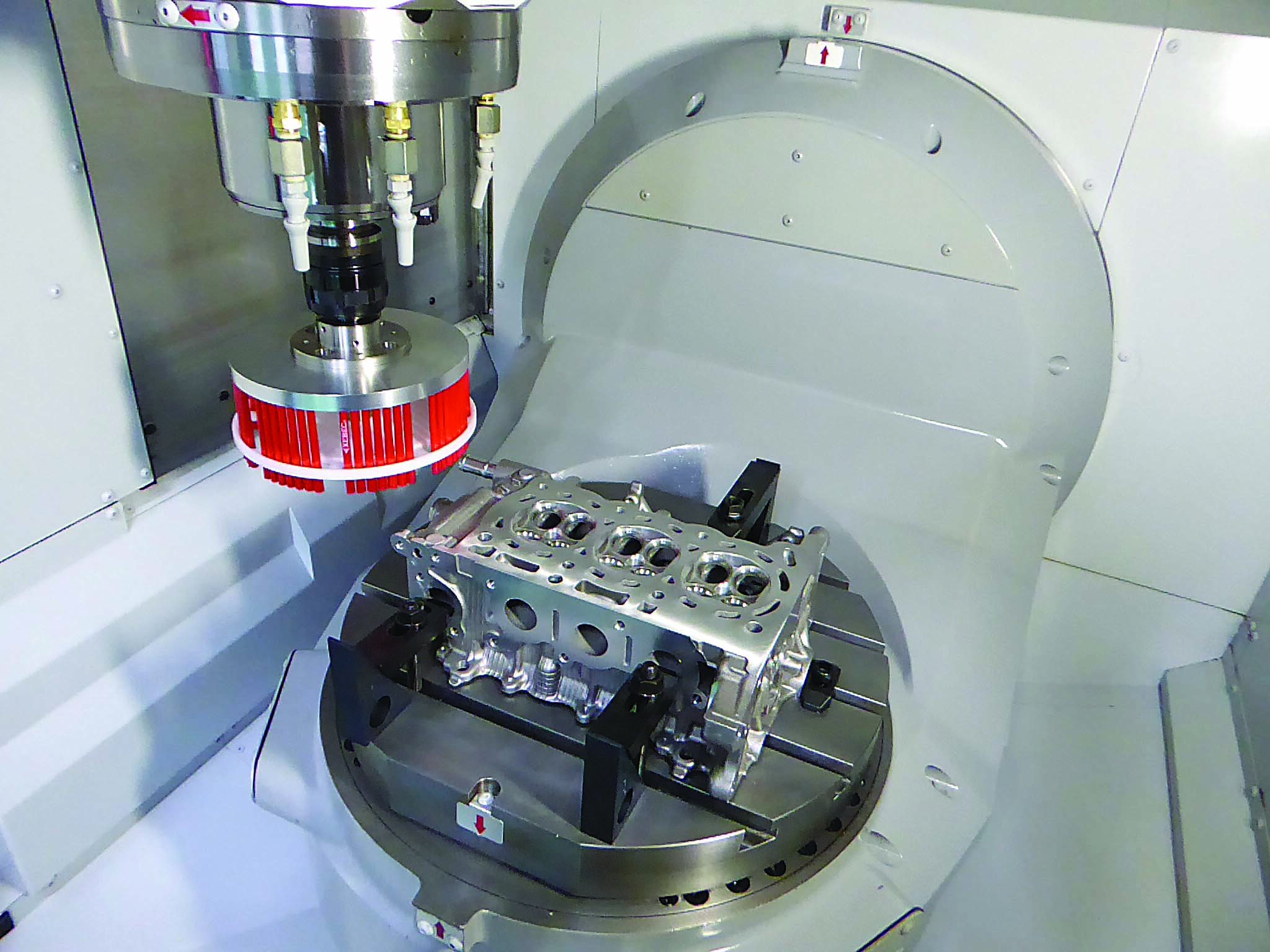
No matter the experience level of a technician, it’s hard to achieve consistent results with hand deburring and finishing — not to mention the difficulty of finding skilled labor in the first place.
With all this in mind, it’s clear that manufacturers are challenged to produce the high-quality, high-precision results that are expected.
To overcome obstacles related to manufacturing machined parts in the aerospace industry, including meeting production schedules with current staffing numbers and reducing scrap to save on the high expense of aerospace parts, manufacturers can integrate automated deburring and finishing solutions in place of manual methods.
Aerospace component manufacturers can expect the following benefits from automated deburring:
- Improved surface finishes
- Increased consistency and quality
- Reduced setup and cycle times
- Boosted throughput and capacity
- Achieved dimensional tolerance requirements
These advantages — and the fact that automated deburring solutions perform both deburring and finishing in the same run — make this approach efficient and ideal for an industry with such high expectations for precision and quality.
To expand on these benefits, here are a few examples of results that aerospace manufacturers can realize when they introduce automated processes.
Gain back time, and optimize resources. Automated deburring is quicker and produces more consistent results than hand deburring. Also, automated deburring reduces much of the setup time involved in CNC machining because automation simultaneously performs both deburring and finishing without the part having to come off the machine. As a result, manufacturers can better utilize their resources, including the time of machines and employees. They also may improve cycle times and enable operators to run several machines at one time to achieve greater throughput. And manufacturers can reallocate employees to more value-added tasks at the facility.
Improve consistency to lower your scrap rate. With automated deburring, manufacturers can more readily and consistently produce parts to spec, achieving the expected precision and finish for aerodynamics, performance and safety. Because of this, manufacturers won’t encounter as many defects and quality issues with produced parts, thus reducing scrap, rework and resource waste. Resource waste includes the additional setup time and resources required to rework a part or start a new one, as well as the resources lost on a scrapped piece.
Produce more, faster. An automated deburring process needs a shorter overall cycle time for parts, considering the time savings on manual methods, setup times and moving of parts. Machines and employees gain back time to perform more jobs and increase production on current jobs. Time savings often equate to hours, especially for large or intricate parts. Employees can use that time to perform high-value tasks. Importantly, producing parts faster makes you competitive and frequently means quicker customer payment cycles.
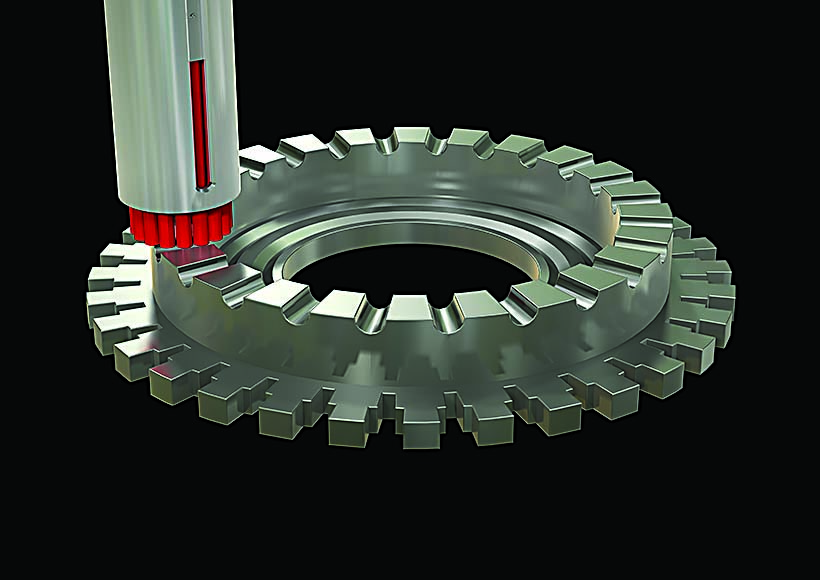
Create a safer work environment. Due to the size and complexity of aerospace parts, manually deburring and finishing parts often means straining, contorting, intensely concentrating and maneuvering into and around difficult areas — all while trying to meet specs for quality and precision. It’s no surprise that there is a high worker injury rate in this industry. Any improvement in the process that enhances worker safety and supports personnel in their tasks will benefit the business as a whole. You’ll likely experience less turnover, and your employees will be safer and healthier in their daily work. Automated deburring removes much of the strain of manual deburring and finishing, lowering the risk of injuries and strain and improving the experience for workers.
Relieve labor shortage pressure. Many shops are forced to have highly skilled CNC operators and even engineers perform hand deburring when production becomes backlogged at facilities. There are opportunities for upskilling by taking employees away from these tedious, time-intensive tasks and training them to operate CNCs or other automated equipment. And with the difficulty that many organizations have simply finding qualified workers, implementing an automated deburring solution increases production without hiring additional personnel.
When you calculate the return on each of these benefits, it’s easy to see that an investment in automated deburring is a game changer for aerospace manufacturers. Customers expect greater product quality and faster delivery from manufacturers. Any effort that aerospace component manufacturers make should help them achieve both faster speeds and higher quality. Investing in automated deburring will help aerospace manufacturers realize their objectives with more efficiency and quality.
Related Glossary Terms
- computer numerical control ( CNC)
computer numerical control ( CNC)
Microprocessor-based controller dedicated to a machine tool that permits the creation or modification of parts. Programmed numerical control activates the machine’s servos and spindle drives and controls the various machining operations. See DNC, direct numerical control; NC, numerical control.
- tolerance
tolerance
Minimum and maximum amount a workpiece dimension is allowed to vary from a set standard and still be acceptable.