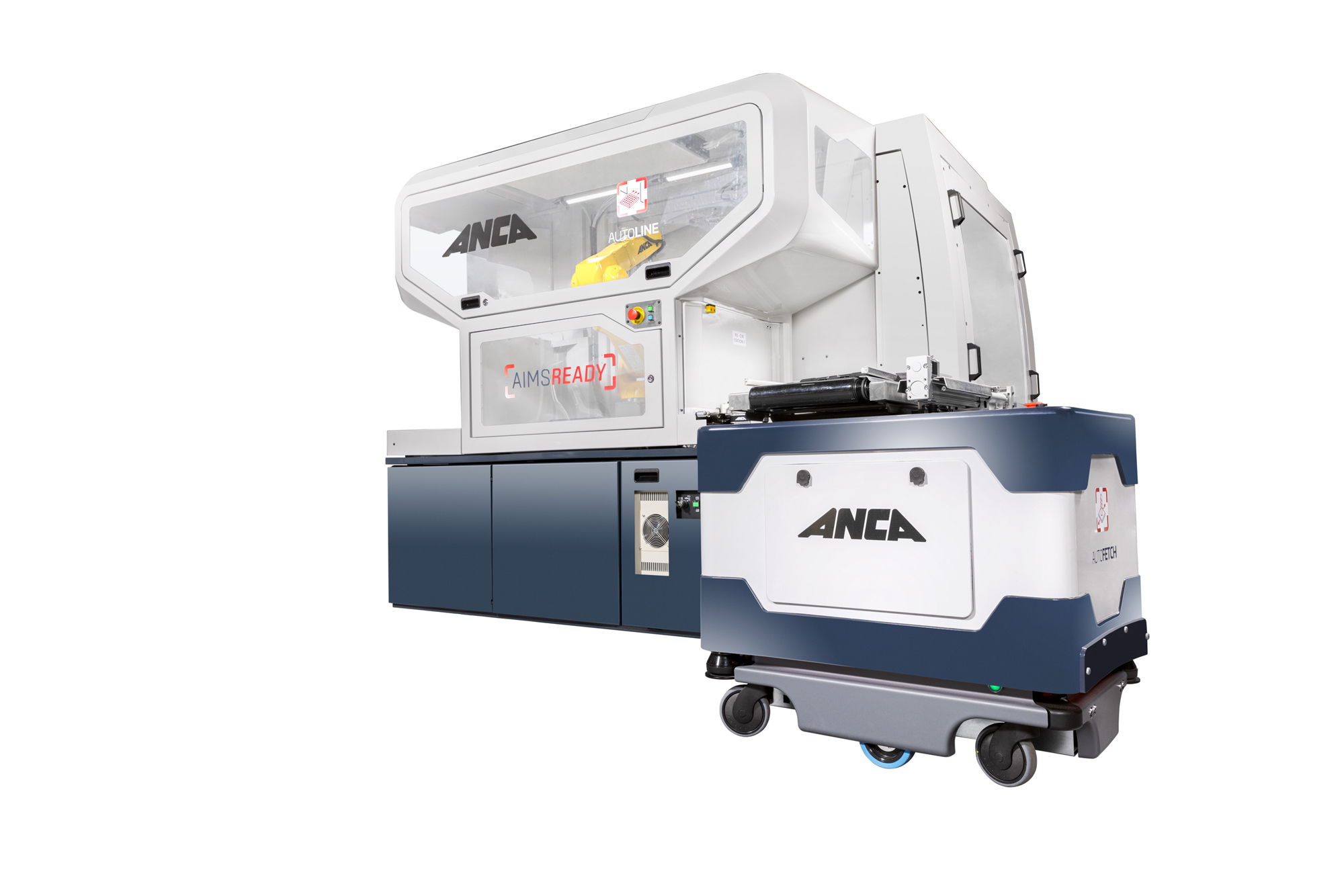
Cutting tools are essential components across many industries, and as these industries expand their product range and complexity, manufacturers increasingly demand high-quality cutting tools that meet unique requirements. For cutting tool manufacturers, deciding what technology to invest in should be driven by business goals, and at IMTS, ANCA will present the grinding technology that it says demonstrates the advantages of investing in a technologically advanced future.
ANCA Inc. general manager Russell Riddiford said “With a long four-year wait since the last IMTS, I am excited to show our visitors the latest technological advancements from ANCA.” Riddiford, who also serves as head of the Wixom, Mich. ANCA office, added that “We have not been idle between shows - once again ANCA has industry-first innovations launching in Chicago this year, and we will be presenting technology that helps solve the challenges faced by many manufacturers in the market.”
The company will also announce the winners of the fifth ANCA Tool of the Year competition at IMTS. The ‘Oscars’ of the cutting tool industry, the contest celebrates the deep experience and creativity of tool manufacturers across a highly skilled grinding industry, Russell concluded.
Integrated manufacturing with AIMS
The company will also showcase its ANCA Integrated Manufacturing System (AIMS) which optimizes cutting tool production through streamlined manufacturing, automation, and connectivity. With ANCA and AIMS, customers can achieve continuous, unattended production that dramatically reduces non-productive machine time, with smart automation that connects sequential tool production processes and offers connectivity across the whole factory.
This is Industry 4.0 — factory-wide integration. The technology considers a factory as a single machine, rather than separating it into many different process elements. This is a powerful concept that brings together one ecosystem and builds it to be as efficient as possible. AIMS, being a modular solution, can be deployed in stages, allowing for an easy, gradual, and smooth transition from traditional to automated and integrated manufacturing.
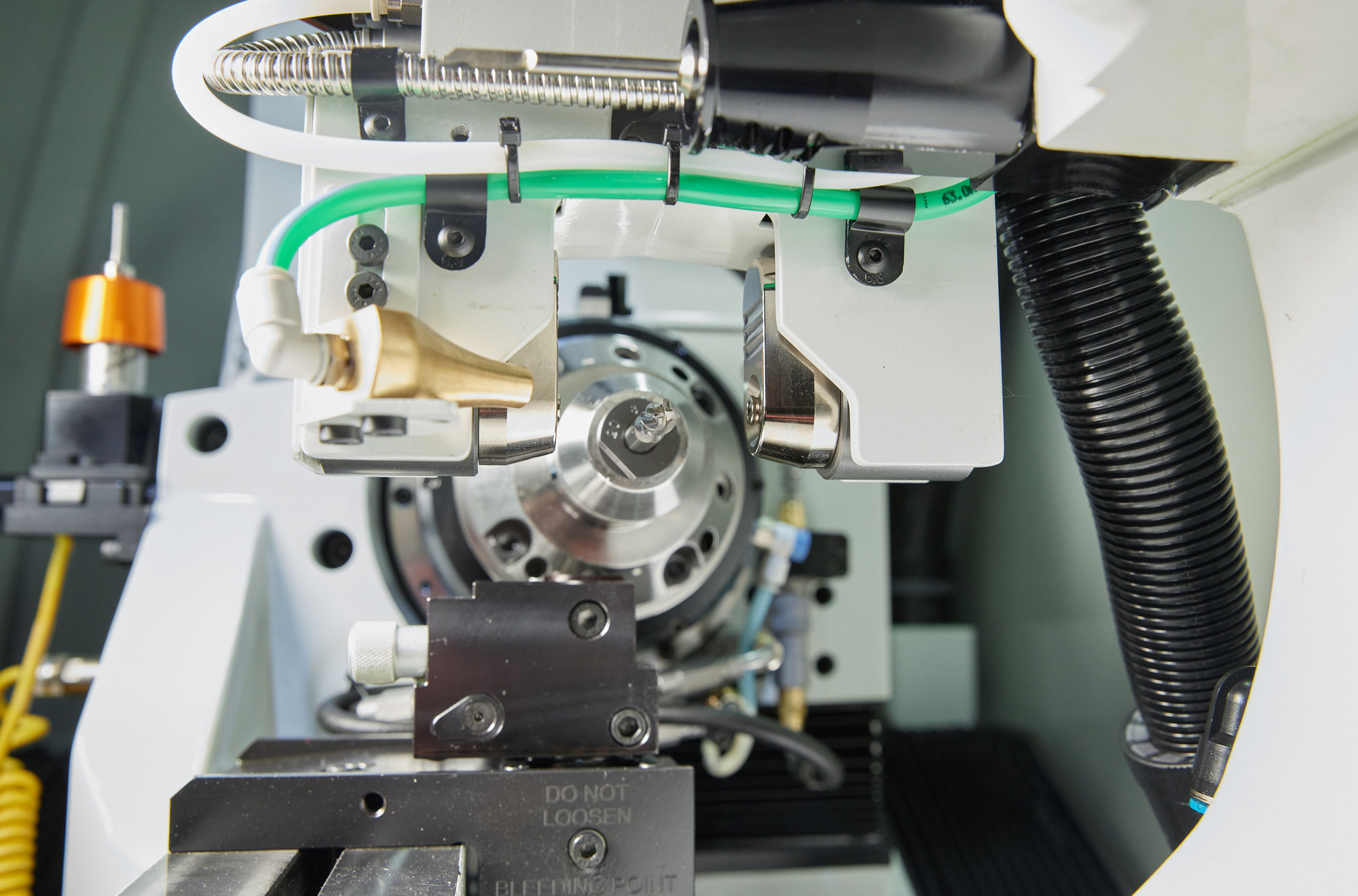
A fully operational manufacturing cell will be displayed at IMTS, demonstrating a fully automatic process of tool manufacturing, from blanks to ground tools. Included will be ANCA’s latest premium machine MX7 ULTRA capable of manufacturing high-quality cutting tools, along with an AutoSet job preparation station, AutoLine for pallet and tool transfer as well as AutoFetch – a robot responsible for material transfer between processes - pallet and individual tools between job preparation, grinding and tool measurement on ZOLLER measuring machine.
Jan Irzyk, AIMS Product Manager said: “AIMS can be configured in many ways but at IMTS visitors can see an unattended manufacturing workflow of two varieties of endmills on one MX7 machine. An important part of this workflow is the closed loop measurement and compensation process using ZOLLER Genius as a measurement station. Depending on an individual customer’s requirements, our system can automatically transfer a tool from the ground batch, clean it, measure required geometries, and transfer the results to the respective grinder where grinding parameters compensation is taking place to achieve the required dimensional tolerance of the batch.”
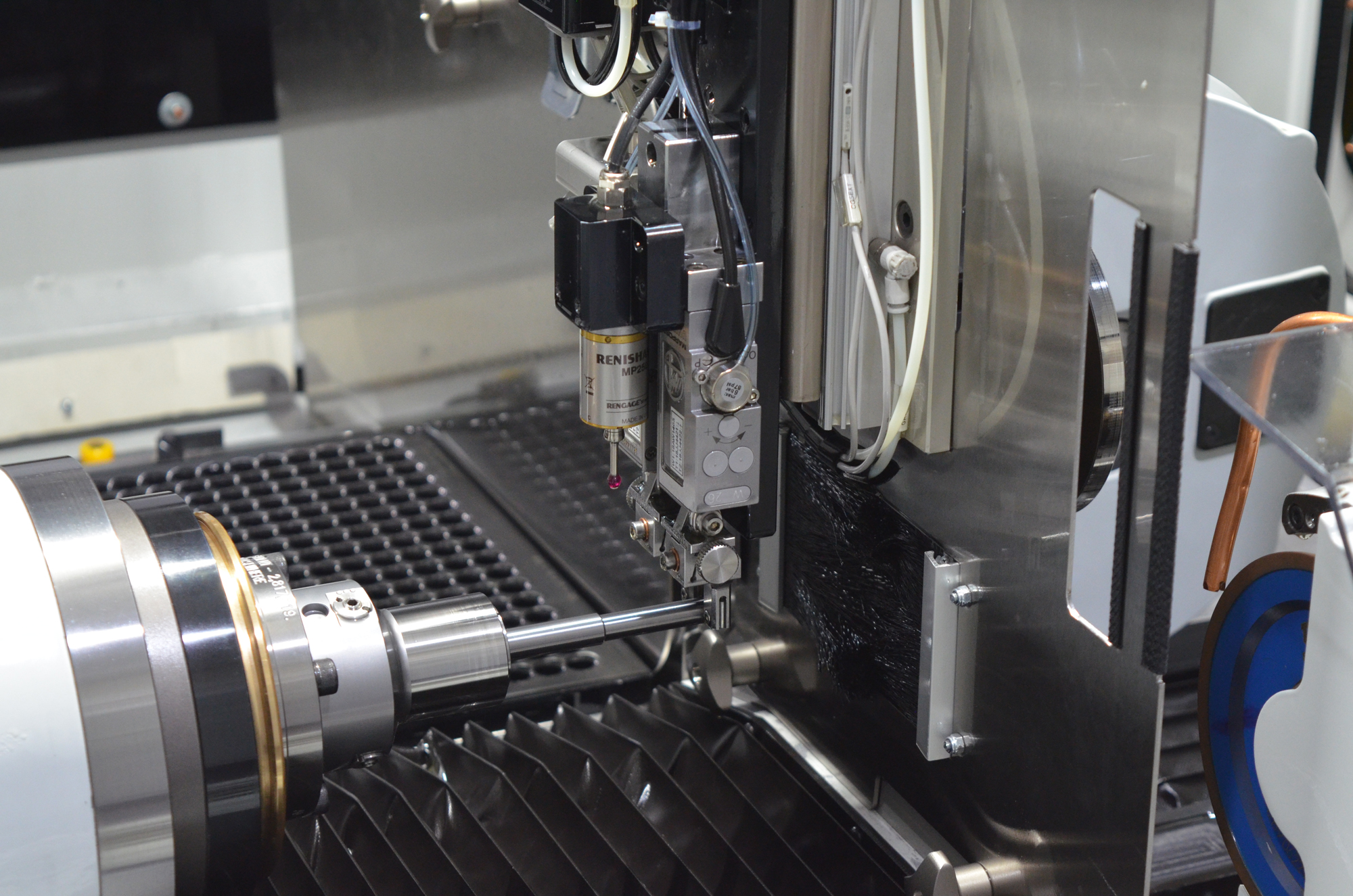
Other products on display, include:
• The CPX in-process OD measurement system is a quality control system that monitors and controls the OD of ground blanks within a batch production.
• The AutoMarkX is an automatic stand-alone laser marking station replacing manual and labor-intensive processes. It is AIMS Ready, which means it can be used as a standalone machine but could be easily integrated into your lights-out, unmanned AIMS manufacturing cell with automatic pallet transfer using the AutoFetch robot.
• The GCX linear can produce skiving cutters, shaper cutters, and regrinding of hobs. It offers advanced stand-alone software to design and optimize the tool, neatly interfaced with the gear tool package inside ANCA's renowned ToolRoom software.
• The ToolRoom RN35 focuses on productivity and cycle time improvements, especially machine running costs. New process optimization features help to enable a reduction in cycle time which in return provides better quality tools and wheel life. This includes an automated reduction in air grinding time and gaps calculated based on tool simulation models. Some of the major enhancements include:
• The FX7 is fitted with ANCA’s Dynamic Tool Loading System, which is ideal for customers manufacturing or regrinding a wide and varied range of tools in small to medium size batches. The tool management system with RFID links unique tool programs to the correct tool in a loader pallet. This works in conjunction with automated Schunk collet changing to allow unattended grinding of random tool diameters and types.
Contact Details
Related Glossary Terms
- collet
collet
Flexible-sided device that secures a tool or workpiece. Similar in function to a chuck, but can accommodate only a narrow size range. Typically provides greater gripping force and precision than a chuck. See chuck.
- grinding
grinding
Machining operation in which material is removed from the workpiece by a powered abrasive wheel, stone, belt, paste, sheet, compound, slurry, etc. Takes various forms: surface grinding (creates flat and/or squared surfaces); cylindrical grinding (for external cylindrical and tapered shapes, fillets, undercuts, etc.); centerless grinding; chamfering; thread and form grinding; tool and cutter grinding; offhand grinding; lapping and polishing (grinding with extremely fine grits to create ultrasmooth surfaces); honing; and disc grinding.
- outer diameter ( OD)
outer diameter ( OD)
Dimension that defines the exterior diameter of a cylindrical or round part. See ID, inner diameter.
- quality assurance ( quality control)
quality assurance ( quality control)
Terms denoting a formal program for monitoring product quality. The denotations are the same, but QC typically connotes a more traditional postmachining inspection system, while QA implies a more comprehensive approach, with emphasis on “total quality,” broad quality principles, statistical process control and other statistical methods.
- slotting machine ( shaper)
slotting machine ( shaper)
Vertical or horizontal machine that accommodates single-point, reciprocating cutting tools to shape or slot a workpiece. Normally used for special (unusual/intricate shapes), low-volume runs typically performed by broaching or milling machines. See broaching machine; mill, milling machine.
- tolerance
tolerance
Minimum and maximum amount a workpiece dimension is allowed to vary from a set standard and still be acceptable.