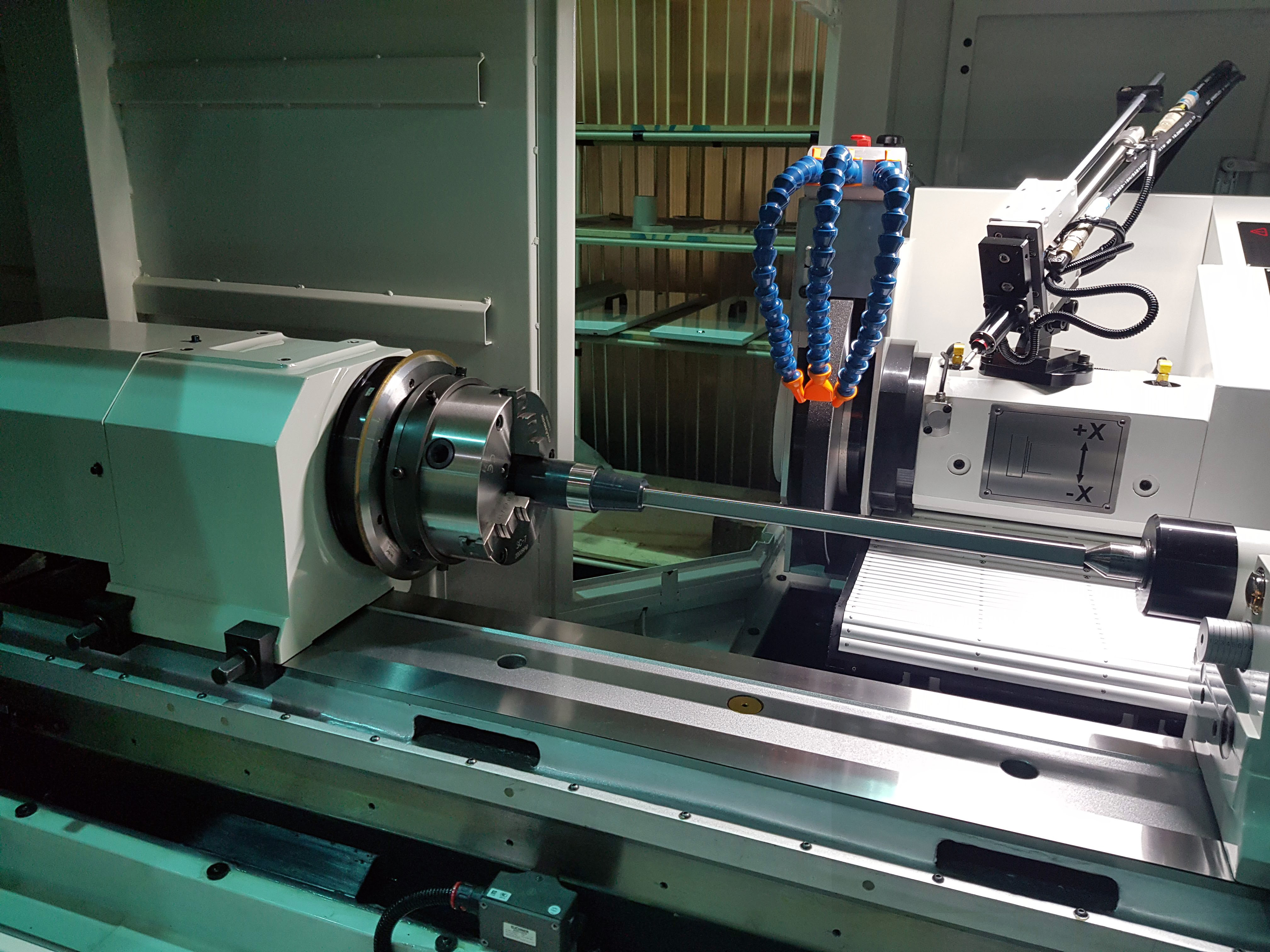
Palmary Machinery Co., Ltd, the Taiwan-based manufacturer of high-performance CNC grinding machines, is migrating control of its advanced CAM series of cylindrical grinders to NUM’s Flexium+ CNC technology.
The company, founded in 1998, manufactures CNC grinding machines in two large production facilities with more than 20,000 square meters of space. It produces a wide range of manufacturing automation – including centerless, cylindrical, internal, vertical and surface grinders – which is sold worldwide through an extensive sales and support network.
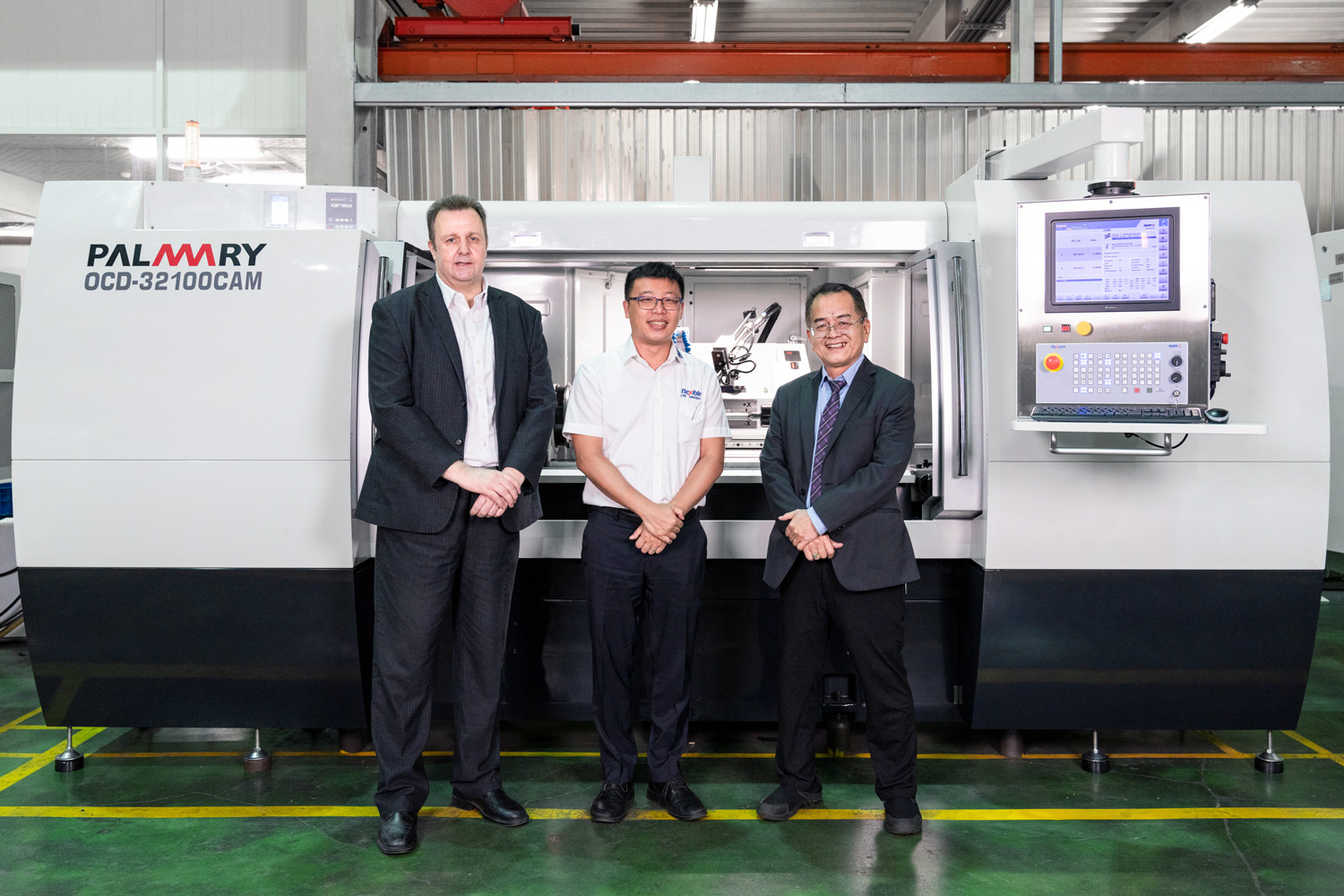
Palmary Machinery has traditionally based its automated grinders on CNC systems produced by manufacturers such as Fanuc and Fagor. However, back in 2017, following Palmary’s acquisition of Top Work Industry – another Taiwanese company that specializes in CNC tool cutters and grinders – it became aware of the advantages of NUM’s tool grinding software.
Johnny Wu, general manager of NUM Taiwan, said, “Top Work and NUM have collaborated very successfully for years. A number of its products are based on NUM’s Flexium+ CNC platform and use our NUMROTO software, which presented Palmary with a very good image of NUM’s technology. When we added non-circular grinding capabilities to NUMgrind in 2020, Top Work immediately drew this development to the attention of its parent company. After fully evaluating the software and host Flexium+ platform, Palmary has elected to adopt NUM’s CNC systems for its CAM series of cylindrical grinders.”
Palmary launched its CAM series of CNC cylindrical grinders in 2020. The grinders met with considerable acclaim, winning the prestigious 28th Taiwan Excellence Award. The family now comprises four models, offering a choice of workpiece length capacities from 250 mm to 1000 mm, which are used in a wide variety of automated manufacturing applications, such as the production of camshafts, crankshafts, cams and eccentric shafts.
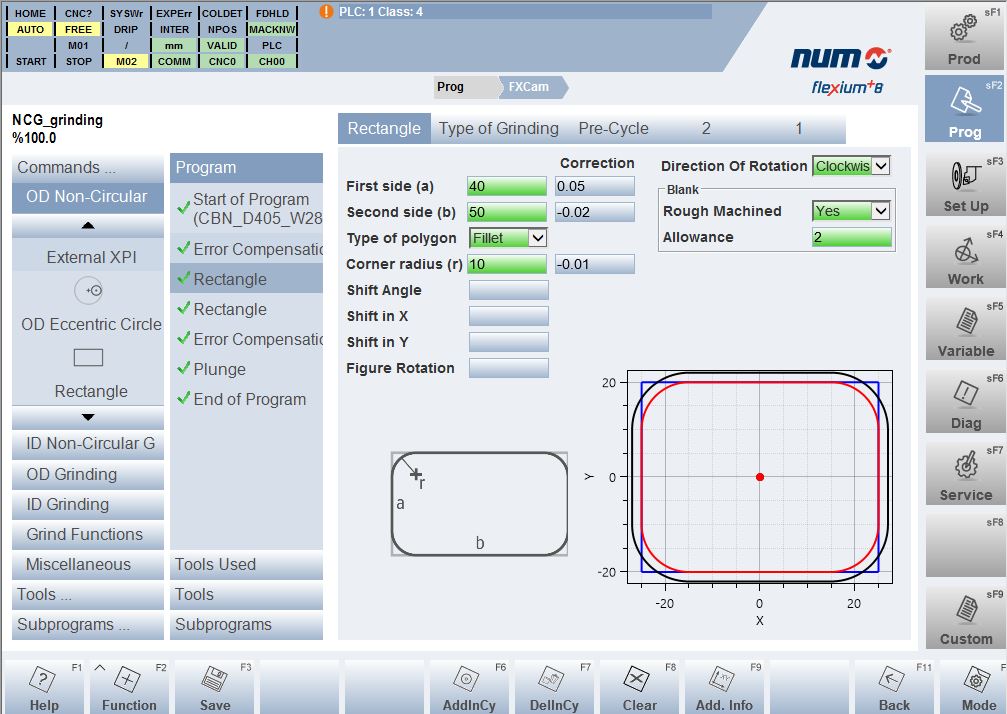
According to Tiger Wang, general manager of Palmary, “Until now, the CNC systems we used in our CAM series machines necessitated our customers using third-party software to generate the grinding path. However, NUM’s CNC technology provides a complete, fully integrated solution. This has several important advantages. It effectively gives us a ‘one-stop shop’ for the machines’ CNC hardware and software, furnishes a very ergonomic, unified HMI (human-machine interface) for machine operators, and offers considerable flexibility for customization and future development.”
The first Palmary machine to be equipped with NUM’s CNC technology is the OCD-32100CAM cylindrical grinder. Capable of accommodating workpieces weighing up to 150 kg and as long as 600 mm, this machine features a direct drive spindle motor (C axis), a brushless servomotor with a precision angle decoder for dynamically controlling the grinding position (Z axis), and a linear motor with a precision optical scale for very accurate control of the grinding wheel in-feed (X axis). Each of the three motors is driven by a NUM MDLUX drive.
The machine’s new controller comprises a NUM Flexium+ CNC system, with an FS153 operator’s panel and an MP06 machine panel. The system’s NUMgrind software helps to completely automate non-circular grinding. The operator simply determines the sequence of the process via the HMI and enters the necessary grinding data. Programming is further simplified by the fact that the HMI is supported by a comprehensive library of 15 predefined external shapes, including eccentric circles, hexagons, pentagons, polygons, Reuleaux triangles and rhombic. Palmary’s customers can also import any customized profile of their choice in the form of a standard DXF file, without involving any third-party CAD/CAM software.
NUMgrind enables machine operators to define the closed shape of the workpiece in the XY plane. Grinding is subsequently performed by interpolating or synchronizing the X axis with the C axis. The Flexium+ CNC system’s NCK transforms the contour from the XY plane into an XC plane, and calculates the corresponding compensation and in-feed movements, taking the grinding wheel diameter into account. The speed profile is also transformed, so that the speed and acceleration are automatically adapted to suit the physical attributes of the machine.
Contact Details
Related Glossary Terms
- computer numerical control ( CNC)
computer numerical control ( CNC)
Microprocessor-based controller dedicated to a machine tool that permits the creation or modification of parts. Programmed numerical control activates the machine’s servos and spindle drives and controls the various machining operations. See DNC, direct numerical control; NC, numerical control.
- computer-aided manufacturing ( CAM)
computer-aided manufacturing ( CAM)
Use of computers to control machining and manufacturing processes.
- grinding
grinding
Machining operation in which material is removed from the workpiece by a powered abrasive wheel, stone, belt, paste, sheet, compound, slurry, etc. Takes various forms: surface grinding (creates flat and/or squared surfaces); cylindrical grinding (for external cylindrical and tapered shapes, fillets, undercuts, etc.); centerless grinding; chamfering; thread and form grinding; tool and cutter grinding; offhand grinding; lapping and polishing (grinding with extremely fine grits to create ultrasmooth surfaces); honing; and disc grinding.
- grinding wheel
grinding wheel
Wheel formed from abrasive material mixed in a suitable matrix. Takes a variety of shapes but falls into two basic categories: one that cuts on its periphery, as in reciprocating grinding, and one that cuts on its side or face, as in tool and cutter grinding.
- linear motor
linear motor
Functionally the same as a rotary motor in a machine tool, a linear motor can be thought of as a standard permanent-magnet, rotary-style motor slit axially to the center and then peeled back and laid flat. The major advantage of using a linear motor to drive the axis motion is that it eliminates the inefficiency and mechanical variance caused by the ballscrew assembly system used in most CNC machines.