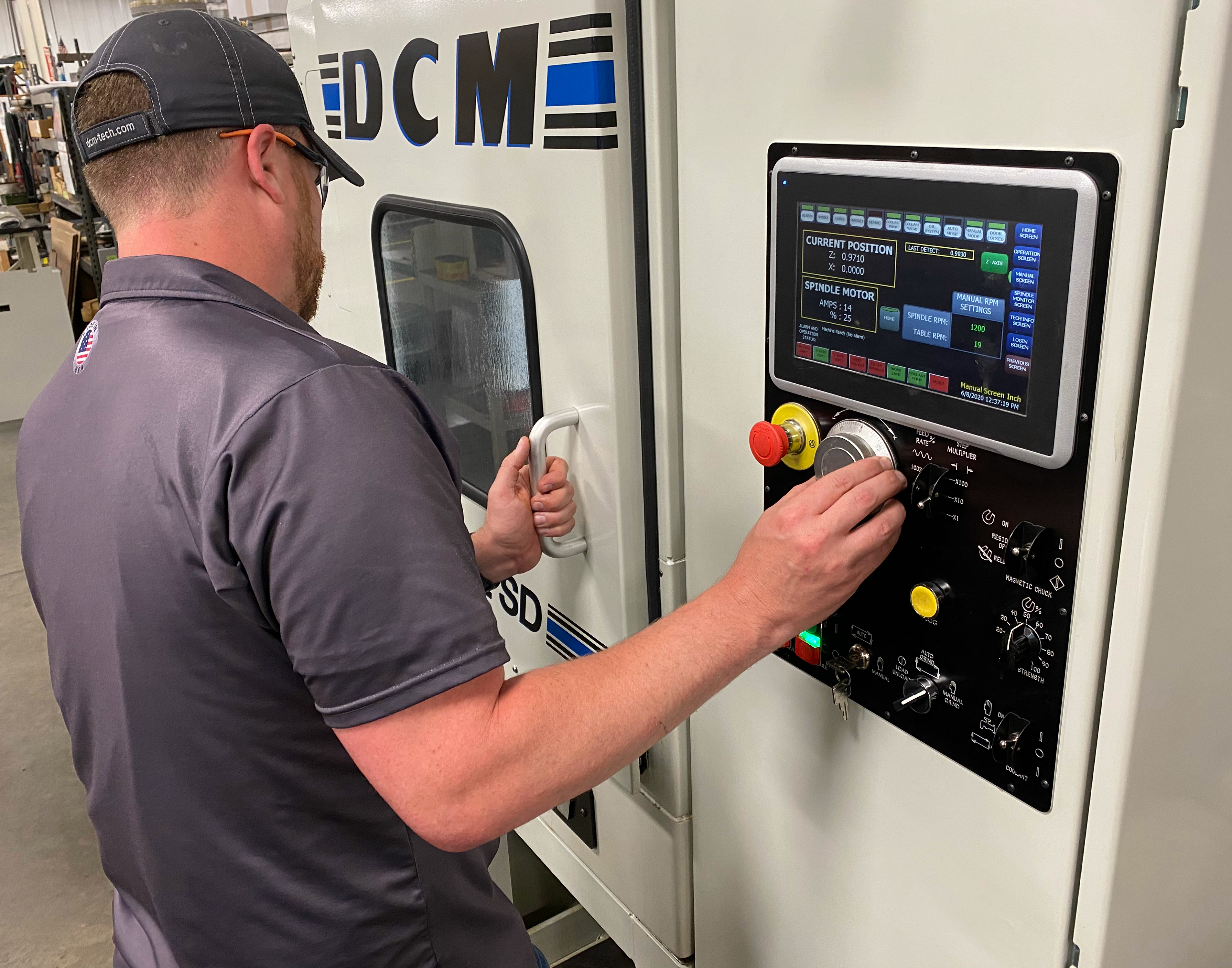
Demand is rapidly increasing for rare earth magnets, such as neodymium and samarium cobalt, which are essential to the global economy due to their magnetic strength, energy-producing capabilities, and high energy-to-weight ratio.
Neodymium (Nd2Fe14B), the strongest magnet for its weight, is widely used in generators, electric vehicles, wind turbines, and consumer electronics, while samarium cobalt (SmCo5) is utilized in applications such as pumps, motors, machinery, and automation.
With China currently dominating the world’s rare earth magnet supply chain, the competition for raw materials is playing out on the international stage. But so too is the development of more efficient processing, grinding, and finishing techniques to fabricate rare earth magnets. To meet the need, advanced, automated rotary surface grinders are used to bring magnets to the final size and finish required prior to permanent magnetization. Through greater control, magnet suppliers can deliver more precise value-added products to tight specifications with less waste – making domestic suppliers more competitive globally.
Streamlining processing
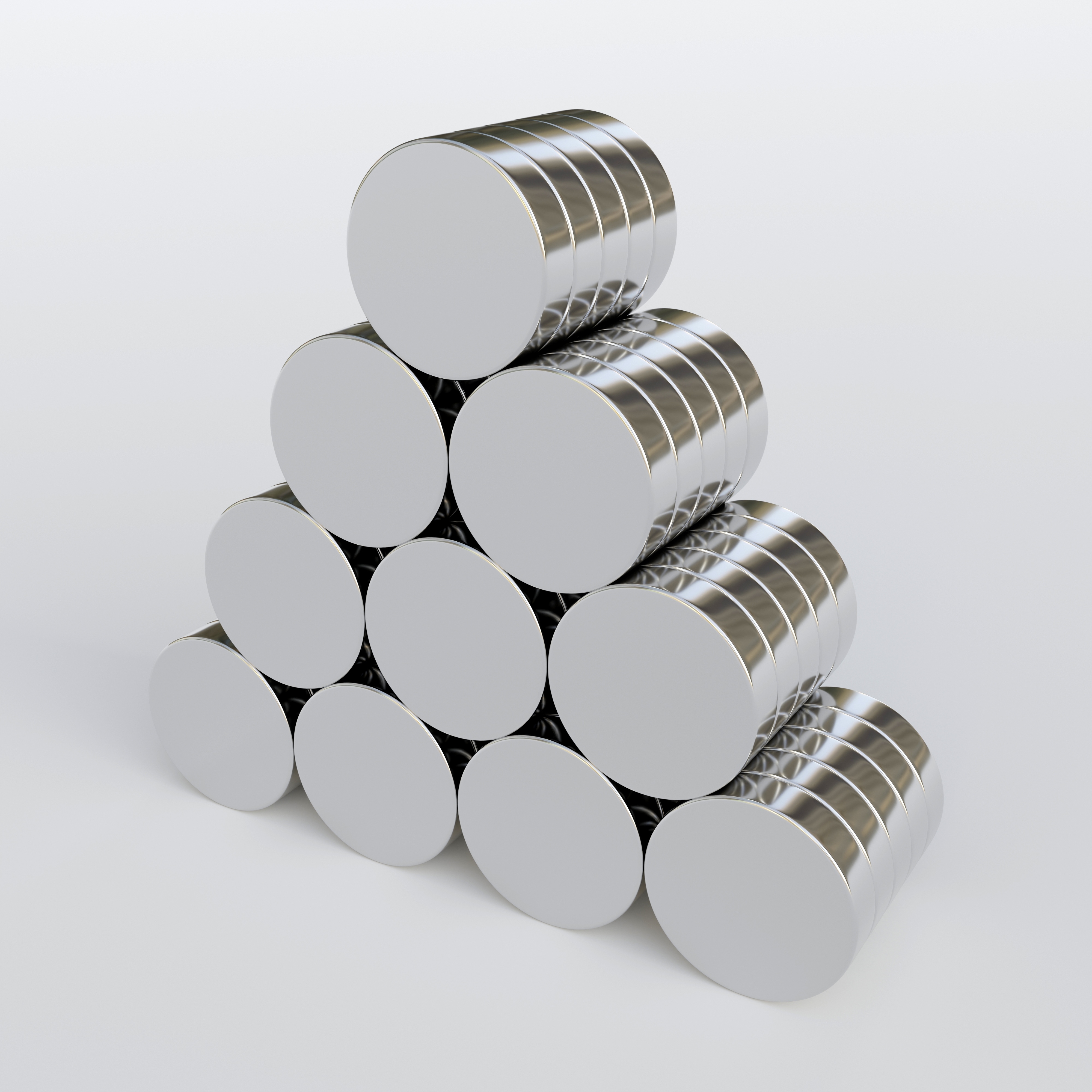
Producing rare earth magnets like neodymium or samarium cobalt requires numerous steps before the product can be magnetized and shipped. After the rare earth ore is discovered, mined, processed, and refined, certain elements are added to create an alloy.
Through a series of processes, the alloy is reduced to a powder which is pressed in a mold under pressure. The resulting block is sintered at high temperature in a furnace to densify the material and then annealed in a heat-treating process to relieve stress.
After these steps, the sintered magnetic material must be precisely machined and ground to the required shapes and sizes with minimal waste. Sintered magnets may be ground smooth and parallel, to a specific OD or ID, or sliced into smaller parts. Since the material is brittle and very hard (Rockwell C 57 to 61), slicing and grinding typically requires a diamond wheel. These processes must be performed with care and precision to minimize chipping and cracking.
However, traditional grinding techniques can be slow and require considerable expertise while lacking sufficient control and reliability for the necessary processes, according to Mike Anderson, Product Manager at Winona, MN-based DCM Tech, a designer and builder of industrial rotary surface grinders.
“Reciprocating table grinders [in which the work piece travels back and forth under the grinding wheel] can be precise, but the material removal rate is slow and many grind passes are required,” says Anderson.
Vintage rotary surface grinders are another option but can be problematic in the hands of less experienced operators. With no control of spindle speeds as well as manual controls, older equipment requires savvy operators that can physically sense machine feedback. Considerable expertise and experience are necessary, which can be a challenge as skilled operators retire.
Industrial magnet manufacturers are discovering a faster, more reliable alternative in modern vertical spindle, rotary table surface grinders, in which the table rotates with the workpiece held firmly in place underneath a vertical spindle. The grinding is not performed by the peripheral edge of the wheel, but by the entire diameter of the abrasive surface, which facilitates grinding performance and consistency.
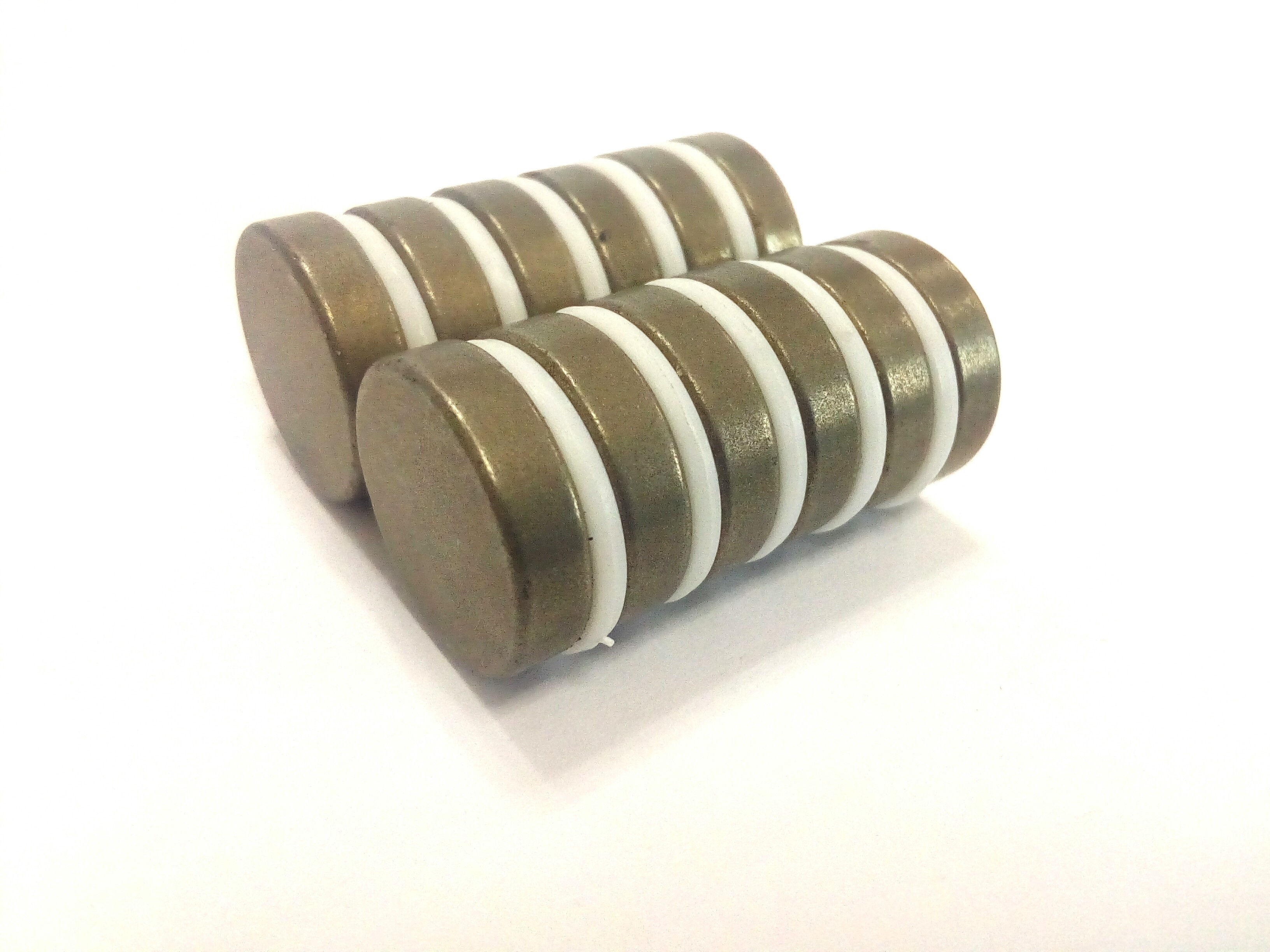
“With rotary table surface grinders, the entire part passes through the wheel, which is more efficient than reciprocating table grinders that may have workpieces wider than the grinding wheel,” says Anderson.
Today, surface grinders are designed with much more advanced sensors and controls that automatically maintain very tight tolerances, removing material down to within one ten-thousandth of an inch of the final thickness. Digital technology allows for an interface with easy-to-use touchscreen controls. When combined with automation, surface grinder operators are no longer required to be highly trained individuals.
For example, rotary units such as DCM Tech’s IG 282 SD, with a 24” variable speed table and 20HP variable speed grinding spindle motor, make it possible for virtually anyone to successfully operate a unit.
One example of innovation available in this model involves the automation of the initial touch off sequence between the abrasive wheel and the part, which typically has to be finessed by the operator. With this updated option, advanced sensor technology detects vibration, then automatically initiates the grind sequence.
“Automatic part detection eliminates the need for the operator to do time-consuming, error prone ‘manual touch offs’ where they would manually feed the grinding machine until it just touches the surface of the part before manually starting the grind sequence,” says Anderson.
Advanced rotary surface grinders are also much faster than reciprocating grinders because the units can finish the grind faster by not having to take multiple fine step finish passes.
In addition, programmable Human Machine Interface (HMI) controls allow operators to enter grind parameters via a touch screen. For routine processes, a variety of grind “recipes” with sets of parameters for specific parts provide repeatability of processes, enhance quality, and aid in quick changeover.
According to Anderson, the automation provided by advanced rotary grinders allows operators to set up the machine and then attend to other tasks. The machine does not need to be constantly monitored because it has built-in load monitoring.
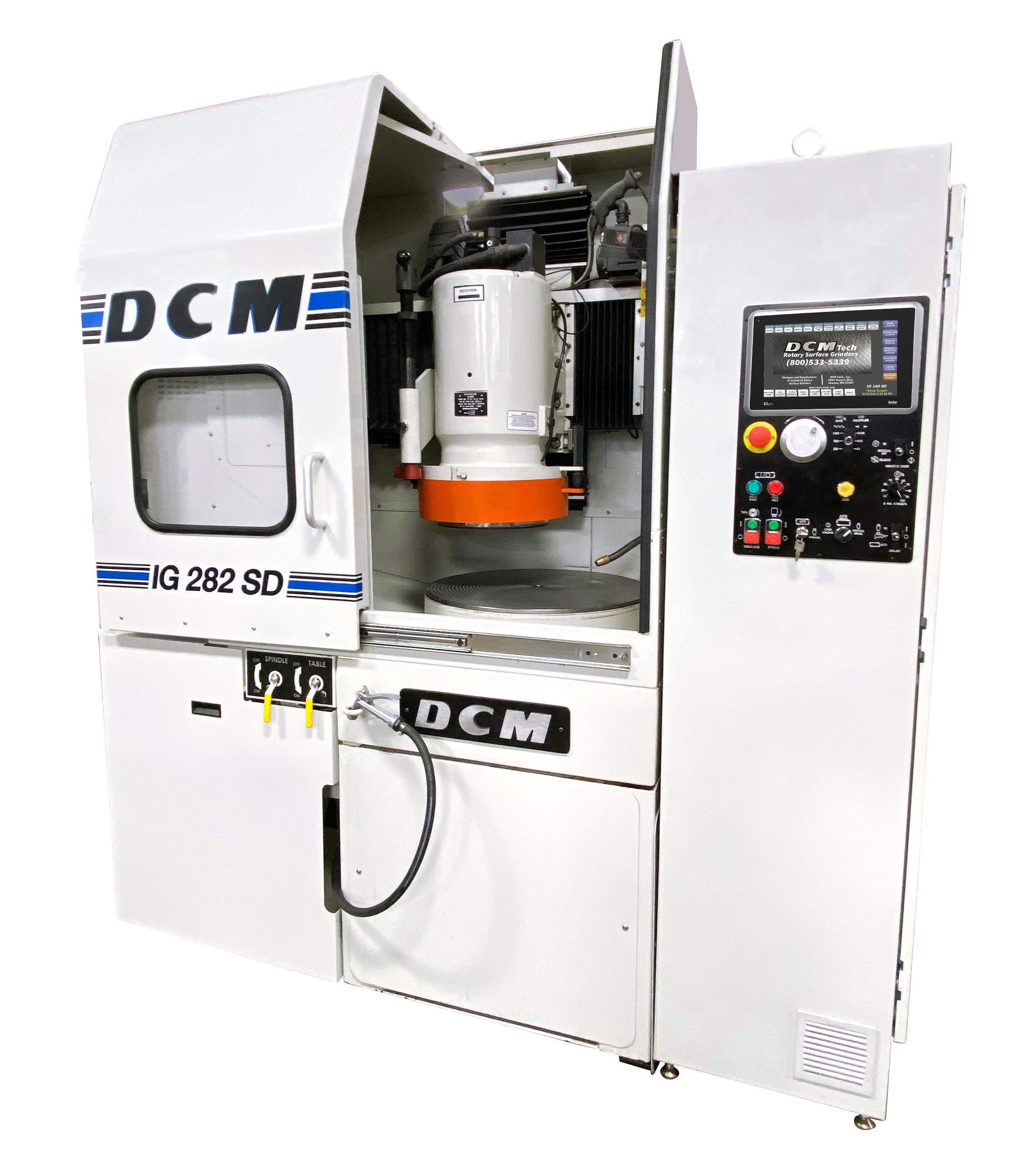
“Load monitoring allows the user to select a spindle load setpoint. The machine will pause the automatic feed motion when the setpoint is met, which is important since the magnet material is both brittle and hard. Too much pressure between the wheel and the part can cause damage to the workpiece. The spindle load limit parameter helps avoid this automatically,” says Anderson.
He adds that the automated grinders also contribute to a cleaner shop environment because the grinding is accomplished inside an enclosed shroud that contains the debris and prevents it from entering the work area.
As the tolerances for grinding become stricter and production requirements grow with rising global demand, rare earth magnet fabricators that take advantage of advanced, automated rotary surface grinders will outperform rivals even as experienced operators retire.
“With automated rotary surface grinders, a machinist can be quickly trained to become proficient at equipment operation. It just takes a few hours of training, not decades of experience as with older machines,” concludes Anderson. He adds that systems incorporating full automation are now being developed that will integrate with a robot to load and unload parts without an operator.
As China continues to dominate rare earth magnet resources, the need to secure a domestic supply chain and fabricate industrial magnets will only increase to meet global demand. Magnet fabricators that take advantage of advanced grinding technology will play a key role in streamlining the manufacturing process, reducing waste, and increasing productivity and repeatability.
Contact Details
Related Glossary Terms
- abrasive
abrasive
Substance used for grinding, honing, lapping, superfinishing and polishing. Examples include garnet, emery, corundum, silicon carbide, cubic boron nitride and diamond in various grit sizes.
- feed
feed
Rate of change of position of the tool as a whole, relative to the workpiece while cutting.
- grinding
grinding
Machining operation in which material is removed from the workpiece by a powered abrasive wheel, stone, belt, paste, sheet, compound, slurry, etc. Takes various forms: surface grinding (creates flat and/or squared surfaces); cylindrical grinding (for external cylindrical and tapered shapes, fillets, undercuts, etc.); centerless grinding; chamfering; thread and form grinding; tool and cutter grinding; offhand grinding; lapping and polishing (grinding with extremely fine grits to create ultrasmooth surfaces); honing; and disc grinding.
- grinding machine
grinding machine
Powers a grinding wheel or other abrasive tool for the purpose of removing metal and finishing workpieces to close tolerances. Provides smooth, square, parallel and accurate workpiece surfaces. When ultrasmooth surfaces and finishes on the order of microns are required, lapping and honing machines (precision grinders that run abrasives with extremely fine, uniform grits) are used. In its “finishing” role, the grinder is perhaps the most widely used machine tool. Various styles are available: bench and pedestal grinders for sharpening lathe bits and drills; surface grinders for producing square, parallel, smooth and accurate parts; cylindrical and centerless grinders; center-hole grinders; form grinders; facemill and endmill grinders; gear-cutting grinders; jig grinders; abrasive belt (backstand, swing-frame, belt-roll) grinders; tool and cutter grinders for sharpening and resharpening cutting tools; carbide grinders; hand-held die grinders; and abrasive cutoff saws.
- grinding wheel
grinding wheel
Wheel formed from abrasive material mixed in a suitable matrix. Takes a variety of shapes but falls into two basic categories: one that cuts on its periphery, as in reciprocating grinding, and one that cuts on its side or face, as in tool and cutter grinding.
- heat-treating
heat-treating
Process that combines controlled heating and cooling of metals or alloys in their solid state to derive desired properties. Heat-treatment can be applied to a variety of commercially used metals, including iron, steel, aluminum and copper.
- inner diameter ( ID)
inner diameter ( ID)
Dimension that defines the inside diameter of a cavity or hole. See OD, outer diameter.
- lapping compound( powder)
lapping compound( powder)
Light, abrasive material used for finishing a surface.
- outer diameter ( OD)
outer diameter ( OD)
Dimension that defines the exterior diameter of a cylindrical or round part. See ID, inner diameter.
- parallel
parallel
Strip or block of precision-ground stock used to elevate a workpiece, while keeping it parallel to the worktable, to prevent cutter/table contact.