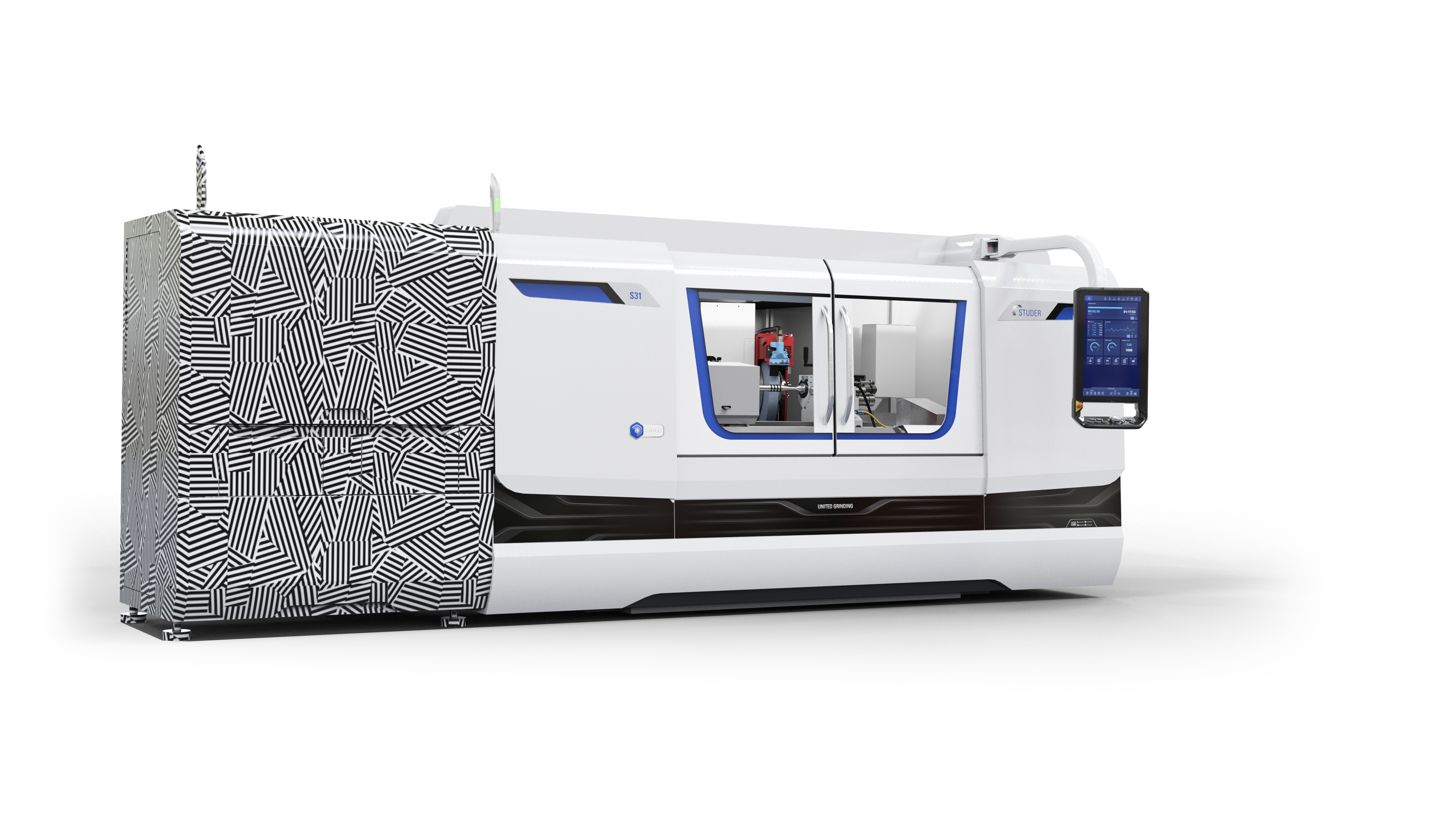
Fritz Studer AG, a market and technology leader in universal, external, internal cylindrical and noncircular grinding, will present a new automation solution on the S31 universal external cylindrical grinding machine at EMO 2023 in Hanover.
The S31 is a cylindrical grinding machine for small to large workpieces in single, small and large series production. It has a distance between centers of 400mm (15.7") / 650mm (25.6") / 1,000mm (40") / 1,600mm (63") and a center height of 175mm (6.9"). It can machine workpieces with a maximum weight of 150kg (330lbs).
In addition, visitors can look forward to other machines on display:
- favorit – A CNC universal cylindrical grinding machine for the individual and batch production of short to long-sized workpieces, which the company says is available in an attractive price for the most important applications.
- S33 with uniLoad – A CNC universal cylindrical grinding machine the company says it is it's "bestselling machine with unbeatable value for the price."
- S100 - internal cylindrical grinding machine is a new ergonomic offering built for the entry-level segment.
- S131R with roboLoad – The do-everything machine for every conceivable internal grinding task.
Customer-Oriented REvolution
With the debut of the C.O.R.E. operating system at EMO 2021 in Milan, the United Grinding Group triggered a revolution in machine tool controls.
The advanced hardware and software architecture on which C.O.R.E. is based enables a novel machine interaction concept. But C.O.R.E. is much more than just a revolutionary operating system. It opens up new possibilities for process optimization, networking and controlling and monitoring the production process. It also lays the foundation for the operation of modern IoT applications, opening the door to the digital future.
Contact Details
Related Glossary Terms
- centers
centers
Cone-shaped pins that support a workpiece by one or two ends during machining. The centers fit into holes drilled in the workpiece ends. Centers that turn with the workpiece are called “live” centers; those that do not are called “dead” centers.
- computer numerical control ( CNC)
computer numerical control ( CNC)
Microprocessor-based controller dedicated to a machine tool that permits the creation or modification of parts. Programmed numerical control activates the machine’s servos and spindle drives and controls the various machining operations. See DNC, direct numerical control; NC, numerical control.
- cylindrical grinding
cylindrical grinding
Grinding operation in which the workpiece is rotated around a fixed axis while the grinding wheel is fed into the outside surface in controlled relation to the axis of rotation. The workpiece is usually cylindrical, but it may be tapered or curvilinear in profile. See centerless grinding; grinding.
- grinding
grinding
Machining operation in which material is removed from the workpiece by a powered abrasive wheel, stone, belt, paste, sheet, compound, slurry, etc. Takes various forms: surface grinding (creates flat and/or squared surfaces); cylindrical grinding (for external cylindrical and tapered shapes, fillets, undercuts, etc.); centerless grinding; chamfering; thread and form grinding; tool and cutter grinding; offhand grinding; lapping and polishing (grinding with extremely fine grits to create ultrasmooth surfaces); honing; and disc grinding.
- grinding machine
grinding machine
Powers a grinding wheel or other abrasive tool for the purpose of removing metal and finishing workpieces to close tolerances. Provides smooth, square, parallel and accurate workpiece surfaces. When ultrasmooth surfaces and finishes on the order of microns are required, lapping and honing machines (precision grinders that run abrasives with extremely fine, uniform grits) are used. In its “finishing” role, the grinder is perhaps the most widely used machine tool. Various styles are available: bench and pedestal grinders for sharpening lathe bits and drills; surface grinders for producing square, parallel, smooth and accurate parts; cylindrical and centerless grinders; center-hole grinders; form grinders; facemill and endmill grinders; gear-cutting grinders; jig grinders; abrasive belt (backstand, swing-frame, belt-roll) grinders; tool and cutter grinders for sharpening and resharpening cutting tools; carbide grinders; hand-held die grinders; and abrasive cutoff saws.