The SAP systems used at Detmold, Germany-based Weidmüller GmbH & Co. KG, a manufacturer of industrial connectivity systems, had a missing link that the company wanted to join up using a manufacturing execution system, or MES. (Weidmüller USA is in Richmond, Virginia.)
“Previously, we had just been using shop floor operations data acquisition systems to capture information,” said Patrick Benjamin Bök, vice president of global digitalization/corporate factory IT and technologies. “Of course, that was not enough to manage and plan our manufacturing.”
Every morning, he said, the printers would produce reams of waybills and forms as part of the material requirements planning batch. And as soon as the product had been manufactured and packaged, the paper documentation ended up in the shredder. This practice was a key driver for the digitalization of the manufacturing processes at the Wutha-Farnroda plant in Thuringia, Germany, a project that subsequently served as a blueprint for Weidmüller’s manufacturing sites around the world. The aim was to increase digital consistency, reduce the use of paper to the bare minimum, make processes transparent and maximize the flexibility of the workforce.
Following an in-depth analysis of the market, two viable providers emerged. However, one had a key advantage as Weidmüller was already in the SAP stable.
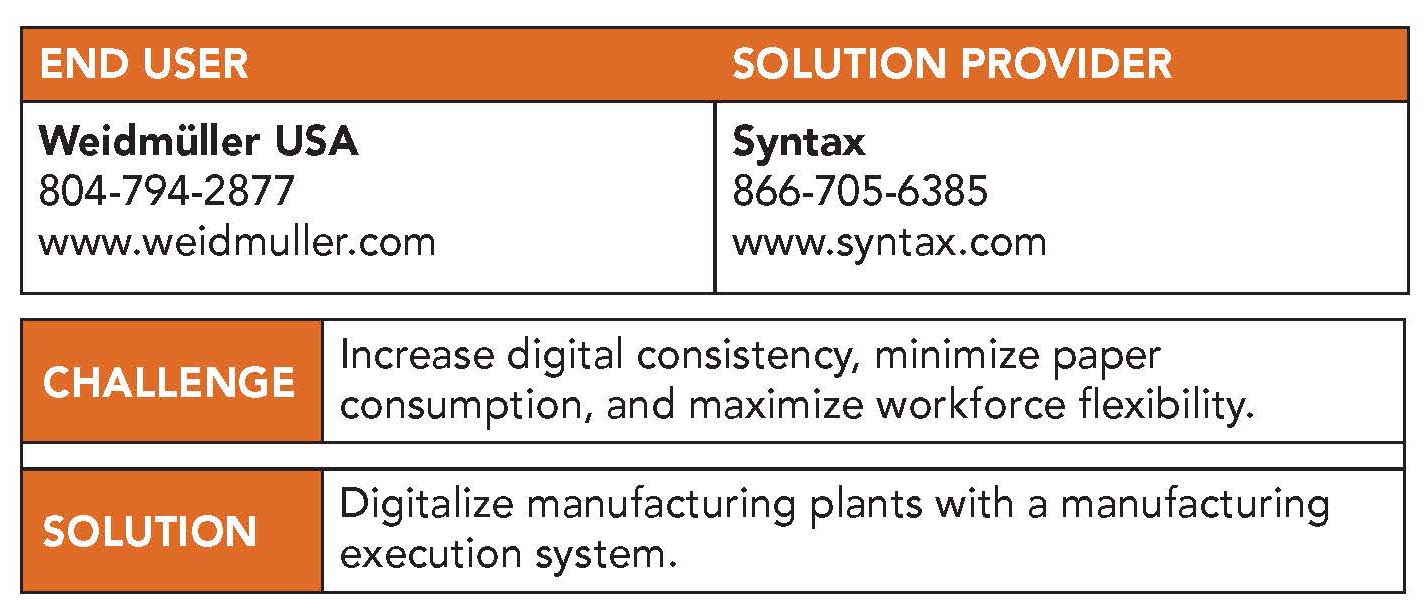
“Going with the other solution provider would have put us in a whole world of interface pain,” Bök said. “So after a lot of discussion among ourselves, we finally opted for the SAP digital manufacturing suite.”
When it came to the decisive meeting, SAP brought along an expert from the IT service provider Syntax.
“Often, when you meet a consultant in this type of situation, they just talk about their own background and work rather than getting into the nitty-gritty of your situation,” Bök said. “But Syntax spoke our language and in particular understood what the experts on our side of the table were saying. They were absolutely fluent when it came to the terminology and workflows of plants like ours. The mutual understanding created instant confidence.”
He said it was critical for the company to keep the project within scope and not overshoot, developing functions that nobody on the shop floor needed. Syntax once again showed its mettle with an agile approach of sprints, reviews and backlogs. This methodology opened the option of agile app development, spontaneously switching the focus and tailoring the solution to Weidmüller’s requirements.
SAP as the solution provider and Syntax as the implementation partner were invested firmly in the process, and the project quickly gathered speed, Bök said. In terms of hardware, the manufacturing machinery was equipped with load cells and connected using an Internet-of-Things controller designed for the task by Weidmüller. The MES also talks to the enterprise resource planning, or ERP, system. Whereas previously the data was held in a range of silos, now it is acquired centrally. That means it can be used and analyzed everywhere. Syntax developed the application logic and ensured that the Weidmüller team was able to feed data into the app interfaces.
As future users, shop floor workers were involved closely in the development and implementation process. Their feedback made a significant contribution to the massive process improvements achieved by the project, including the improvement of many items of the master data. The first manufacturing machine went live after three months.
Bök said Weidmüller’s staff is always responsible for managing multiple machines at the same time while on shift.
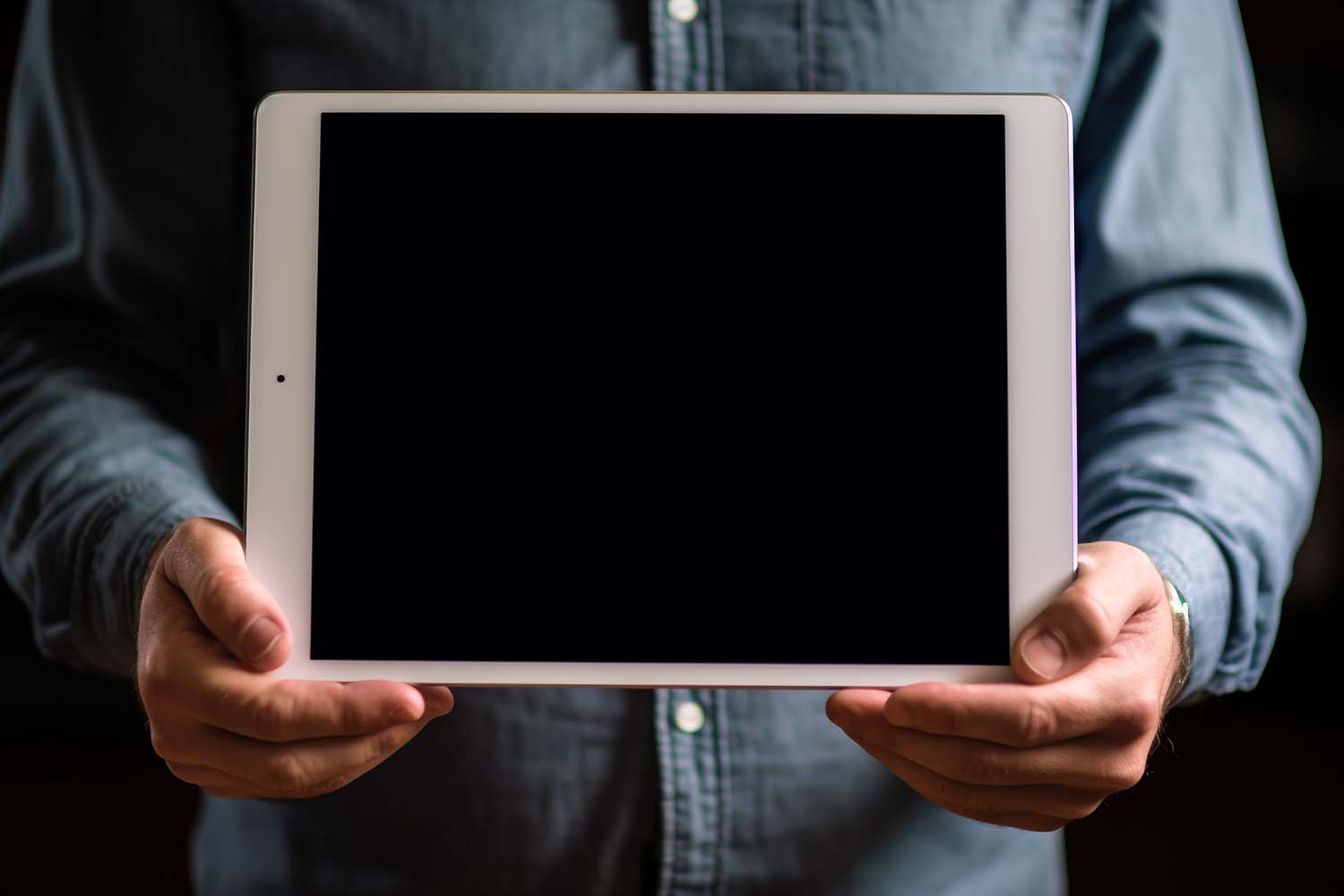
“Instead of carrying around clipboards stuffed full of paper,” he said, “our people now have an Apple iPad, which can display all of the data they need.”
The tablet shows the status for each machine under its responsibility, the machine’s current load and any potential issues. This saves the constant back and forth to keep an eye on things at several stations. Workers can use their iPads to document visual inspections, record transaction volumes and scan materials wherever they are.
“We have hugely reduced the distances in manufacturing,” Bök said.
In addition, all machine operating data can be viewed on the shop floor. He said this allows any problems to be detected as they occur and defective parts to be replaced.
“The MES shows us what is going on at all times,” Bök said. “That is amazing. It does not matter where the machine operator is at any particular time. They can see instantly if it is not working as required.”
He said transparent machine data means that the manufacturing process also can be optimized. For example, injection molding tools heat plastic, inject it into a mold, allow the part to cool, eject it and then repeat the process. The MES makes the process transparent so parameters, such as pressure or cooling time, can be optimized.
“We can compare the length of time planned for production of a part against how long we actually need,” Bök said. “We have noted that in many instances we can achieve significantly higher throughput and therefore optimize deadlines.”
Weidmüller made sure that all its stakeholders were onboard early in the process.
“As soon as we encountered a pinch point,” Bök said, “we sought a lever together and established whether or not the employees wanted a modification to be made. We broke down numerous processes as a result and have introduced comprehensive improvements and leaner approaches.”
He said employee feedback helps determine if functions go live. It was important for the company not to overload the workforce or stretch it too thin. By expanding functionality a step at a time and thanks to an accompanying transformation management process, there were ample opportunities for workers to get used to new practices while the shop floor’s ability to contribute to decision-making increased user acceptance for the system.
For companies considering a similar project, Bök recommends choosing an implementation partner carefully.
“Can they pursue an agile strategy and navigate a moving target?” he said. “Does the consultant understand your situation and the specifics of your industry? Time and again, throughout our project meetings Syntax asked a justifiable question about whether certain functions actually added value on the shop floor. I really do not know if we could have completed the project with the same degree of success with any other service provider.”
Related Glossary Terms
- feed
feed
Rate of change of position of the tool as a whole, relative to the workpiece while cutting.
- overshoot
overshoot
Deviation from nominal path caused by momentum carried over from previous step, as when a tool is rapidly traversed a considerable distance to begin a cut. Usually applies to CNC machining and is prevented if the control has the appropriate look-ahead capability. See look-ahead; undershoot.