Although machine shops differ in many ways and no two are the same, they share some common goals. Improving tool life and reducing tooling cost is a universal goal of all shops. After labor, tooling is usually the largest expense in every shop, and, like everything else, those costs are quickly escalating.
Machinists, shop owners and engineers are naturally focused on reducing the cost of tooling and put great effort into improving tool life. Their efforts are most often focused on things like endmills, drills, taps and inserts. It makes sense, because these items are typically the last tools to touch the part and they create the most value.
Sawing is frequently overlooked as an important part of the machining process because it occurs so early in the manufacturing process and rarely contributes to the final geometry of the part. In the past, sawing was the job given to the young apprentice after graduating from sweeping and shoveling chips. It is evident that, except for a small number of shops that specialize in sawing, the operation is often not considered critical.
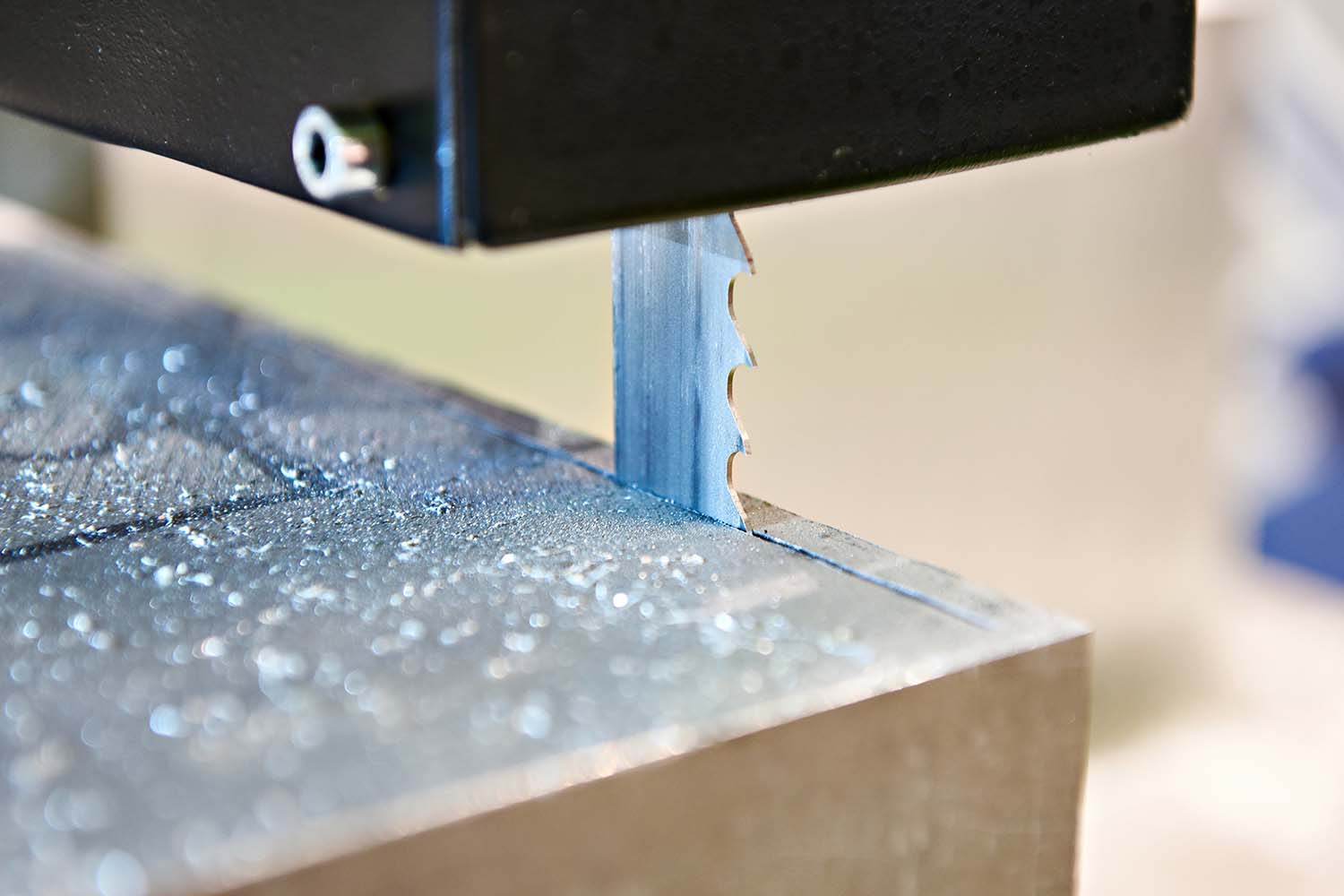
To the contrary, however, sawing is a very important operation. Sawing reduces bulk materials into the blanks that become the finished good. When done correctly, a well-cut part can produce a blank that requires less machining. With a good saw that is set up properly one person can feed many lathes and mills with cut parts ready for machining. Of course, there are several aspects that are critical to successful sawing, but the primary component is the saw blade. Choosing the correct blade and setting the correct parameters aids accuracy and improves blade life.
Blade material
Choosing the correct blade material is the first step toward successful sawing. Practically speaking, there are essentially three types of blades: carbon steel, a combination of carbon steel and high-speed steel (bi-metal), and blades that have been “tipped” with something like carbide or diamond.
Carbon steel blades are the least expensive and typically used to cut non-metallic materials like wood and plastics. Carbon steel blades do not typically have application in modern metalworking shops as they are products of earlier times before the existence of materials like high-speed steel.
Bandsaw blades need to be hard so they last, but they must also be flexible, so they do not break. A bandsaw blade made from HSS alone would be brittle and prone to fracture, therefore bi-metal blades were developed. Made by welding a strip of carbon steel to a strip of HSS, bi-metal blades offer the best of both materials. These blades are the most common type used in shops today, and have the broadest application. Bi-metal blades can be used on almost any material, and they are ubiquitous in modern machine shops.
Diamond-plated or carbide-tipped bandsaw blades are available but less common than the bi-metal blades because they only have non-ferrous applications. Most shops are cutting a variety of materials, so mounting diamond or carbide tipped blades on the saw would limit the types of materials that can be processed. However, if you are only cutting materials like aluminum, plastic or phenolics, then diamond and carbide are the best choices.
It is probably obvious that matching blade material to the raw material to be cut is important. However, matching the blade material to the saw also is critical. The saw must be rigid enough to tension the blade properly, and each model of saw requires a specific length of blade. As with other cutting tools, the best approach is to get input from the blade manufacturer.
Tooth pitch
Saw blades have different tooth pitches to accommodate different material thicknesses. To be efficient and cut as fast as possible, you want to use the coarsest tooth pitch possible. However, if the pitch is too coarse, then the teeth are likely to fracture. And if the pitch is too fine, then the teeth can become loaded, which can result in broken blades. In general, the best approach is to purchase the coarsest pitch possible while keeping 3.5-4 teeth in the cut. Any less, and you risk breaking teeth. While too many teeth in the cut can cause problems, it is better to have more teeth in the cut than to have too few.
Many shops reach a productive balance by using variable pitch blades, which have an alternating pattern of coarse and fine pitches that allow the shop to change from thick and thin materials with fewer blade changes. Getting the tooth pitch right is as important as selecting the right blade material.
Blade life
Some other simple things to remember about sawing that will improve blade life and ensure efficiency.
- Set proper cutting parameters. As with milling and turning, sawing requires that you have the blade speed and feed rate set correctly in order to maximize blade life. All the blade manufacturers give away speed and feed charts to make it easy to set proper speeds.
- Use a coolant that is formulated for sawing and maintain it. Keep the coolant tanks filled to the correct level, maintain proper concentration and replace at the proper interval.
- Maintain the chip brushes. Most saws will have a rotating brush on the exit side of the cut that is intended to brush chips out of the tooth gullet. This prevents recutting of chips, which would otherwise shorten the life of the blade. These brushes need to be replaced when they are worn.
- Cut the material through the thickest section. For example, if you want to cut ¼ x 4 flat bar, then cut it through the 4" section as it is less likely to damage the blade. Stacking thin materials together to make a thick section also works well. Stacking eight pieces of the same ¼ x 4 flat bar will yield a 2 x 4 section and eight pieces per cut.
- Tension blades correctly. Having a blade too tight or too loose will cause damage and can be dangerous. Purchase a blade tensioning gauge and check the tension occasionally. Yes, blade manufacturers will give you the proper specifications.
- Make sure the saw is well maintained. Worn bearings and blade guides will allow the blade to “wander” in the cut, causing a poor cut and reduced tool life. Also, ensure the clamping mechanisms are well serviced and not worn. A moving workpiece can strip the teeth off a blade.
Everything discussed to this point has focused on bandsaw blades because bandsaws are the most common style of saw found in machine shops. These guidelines are applicable to cold saws, which use a circular blade much like those you buy for wood working and deck building.
Sawing is often the first operation in the machining process. Done well it can help reduce costs associated with other machining operations and improve raw material yields. World class machine shops give sawing operations the same level of attention as milling, turning and grinding.
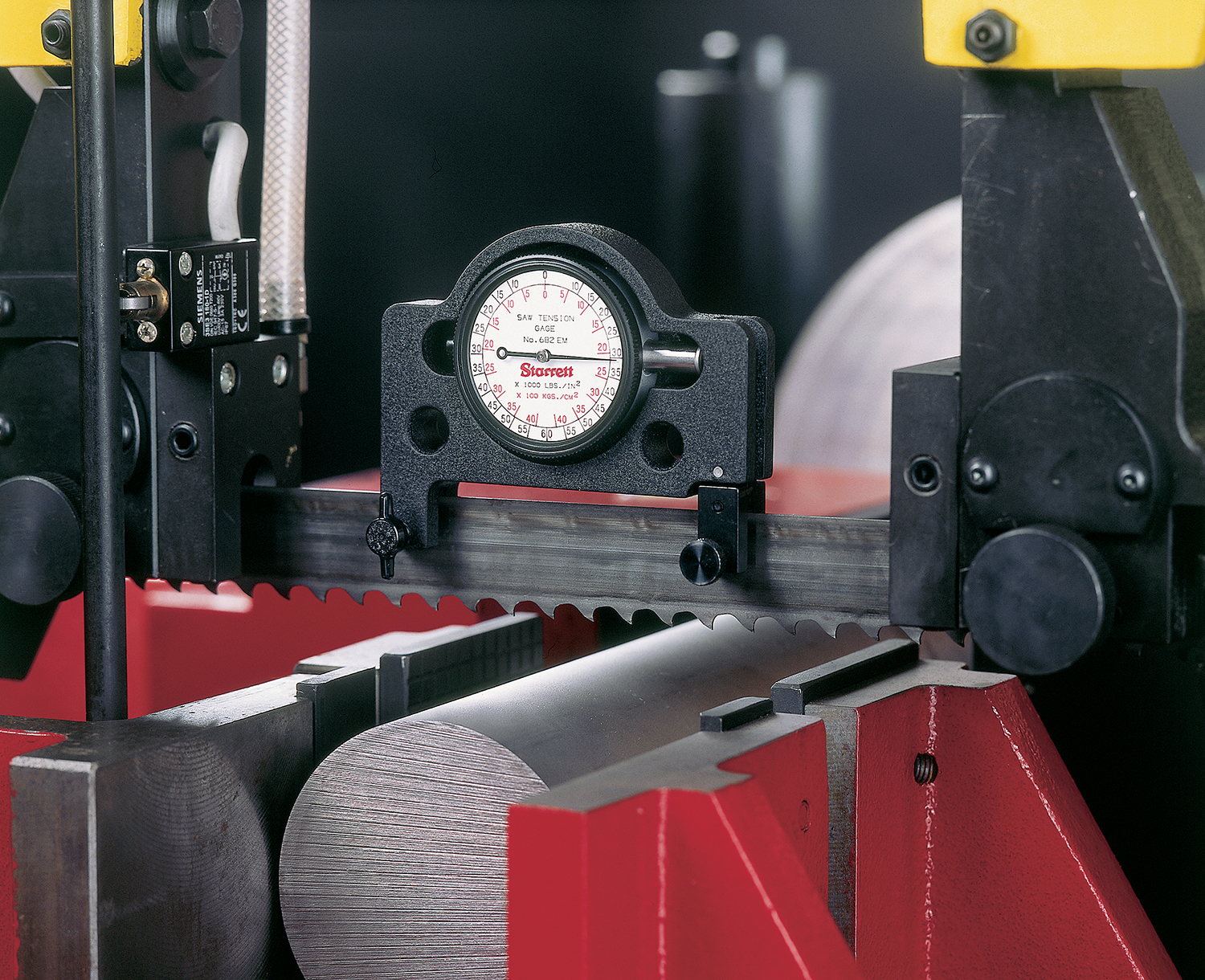
Tips for Extending Blade Life
Improving saw blade life saves costs and increases productivity. The L.S. Starrett Company offers some guidelines for extending the life of your blade:
Breaking in the blade
Taking the time to break in a saw blade is time well spent, and we recommend always performing this step. The process to break in a band saw blade will vary depending on the characteristics of the material being cut. While breaking in a blade, have the machine running at the normal surface feet per minute (sfm).
For softer materials, such as carbon steel and aluminum, adjust the feed pressure to 50% of the normal cutting rate for the first 50 sq. in. to 100 sq. in. Then, gradually increase the feed pressure to a cutting rate of 100%.
For harder materials — such as nickel-based alloys, Inconel, or other difficult materials such as hardened steels, tool steels and stainless steels — adjust the feed pressure to 75% of the normal cutting rate when you reach 25 sq. in. to 75 sq. in. Gradually increase the cutting rate to reach 100% after 50 sq. in. As the feed pressure is increased to the 100% cutting rate, be careful to avoid creating vibrations that can occur by increasing the rate too quickly.
Cutting fluid considerations
Cutting fluid, a.k.a. coolants and lubricants, is important in band sawing operations because it cools the blade, lubricates the teeth and washes chips away. Without it, a blade would likely overheat, wearing out the teeth faster with chips filling the blade gullets, which leads to blade stress, tooth breakage and inferior cuts.
A rich cutting fluid solution does a better job coating and lubricating the blade throughout the entire cut. Coolant should wash over the blade as it enters and exits the cut, recirculating throughout the cutting process. Water will evaporate from the mixed solution, so replace it as needed. Also, keep an eye out for chips that fly into the machine and block coolant flow, as well as system leaks — all which can cause problems.
Proper feeds and speeds
Proper feeds and speeds are necessary not only for blade life and sawing production, but also for the surface quality of the piece being cut. Blade speed should be established based on the type of material. If the speed is set too low, the teeth can over penetrate, which will put excessive stress on them, eventually causing the teeth to strip. Running a blade at too slow a speed will result in teeth with loaded chips and cause the teeth to “walk.” Too fast a feed rate will also cause the teeth to load, producing a similar outcome. It is also important to refer to cutting recommendations from the saw machine manufacturer.
Establish the right tension
Tension should be set to the machine manufacturer’s recommendations, and a blade tension gauge should always be used to check it. Most production machines require between 28,000 psi and 32,000 psi of blade tension. Low blade tension allows the blade to “walk,” bowing the blade as it travels between the guide arms, which may cause cracking in the back of the blade. Without adequate and proper blade tension, the beam strength will be insufficient to hold the blade straight, resulting in crooked cuts.
Brush off the blade
Most saw machines have a rotating wire brush that clears chips out of blade gullets while the blade is cutting, helping to extend blade life. It is important to keep the brush in good working condition, and it should be positioned close to the drive wheel. The brush needs to be close enough to the blade for the filaments to effectively remove chips from gullets. However, do not set the brush too close to the blade because the hard-hitting filaments could prematurely dull band saw teeth. A brush set too close to the blade also could wear itself out and quickly become useless. The brush should reach in and touch without going beyond the deepest part of gullets.
Contact Details
Related Glossary Terms
- alloys
alloys
Substances having metallic properties and being composed of two or more chemical elements of which at least one is a metal.
- bandsaw
bandsaw
Machine that utilizes an endless band, normally with serrated teeth, for cutoff or contour sawing. See saw, sawing machine.
- bandsaw blade ( band)
bandsaw blade ( band)
Endless band, normally with serrated teeth, that serves as the cutting tool for cutoff or contour band machines.
- bandsaw blade ( band)2
bandsaw blade ( band)
Endless band, normally with serrated teeth, that serves as the cutting tool for cutoff or contour band machines.
- coolant
coolant
Fluid that reduces temperature buildup at the tool/workpiece interface during machining. Normally takes the form of a liquid such as soluble or chemical mixtures (semisynthetic, synthetic) but can be pressurized air or other gas. Because of water’s ability to absorb great quantities of heat, it is widely used as a coolant and vehicle for various cutting compounds, with the water-to-compound ratio varying with the machining task. See cutting fluid; semisynthetic cutting fluid; soluble-oil cutting fluid; synthetic cutting fluid.
- cutting fluid
cutting fluid
Liquid used to improve workpiece machinability, enhance tool life, flush out chips and machining debris, and cool the workpiece and tool. Three basic types are: straight oils; soluble oils, which emulsify in water; and synthetic fluids, which are water-based chemical solutions having no oil. See coolant; semisynthetic cutting fluid; soluble-oil cutting fluid; synthetic cutting fluid.
- feed
feed
Rate of change of position of the tool as a whole, relative to the workpiece while cutting.
- flat ( screw flat)
flat ( screw flat)
Flat surface machined into the shank of a cutting tool for enhanced holding of the tool.
- gang cutting ( milling)
gang cutting ( milling)
Machining with several cutters mounted on a single arbor, generally for simultaneous cutting.
- grinding
grinding
Machining operation in which material is removed from the workpiece by a powered abrasive wheel, stone, belt, paste, sheet, compound, slurry, etc. Takes various forms: surface grinding (creates flat and/or squared surfaces); cylindrical grinding (for external cylindrical and tapered shapes, fillets, undercuts, etc.); centerless grinding; chamfering; thread and form grinding; tool and cutter grinding; offhand grinding; lapping and polishing (grinding with extremely fine grits to create ultrasmooth surfaces); honing; and disc grinding.
- high-speed steels ( HSS)
high-speed steels ( HSS)
Available in two major types: tungsten high-speed steels (designated by letter T having tungsten as the principal alloying element) and molybdenum high-speed steels (designated by letter M having molybdenum as the principal alloying element). The type T high-speed steels containing cobalt have higher wear resistance and greater red (hot) hardness, withstanding cutting temperature up to 1,100º F (590º C). The type T steels are used to fabricate metalcutting tools (milling cutters, drills, reamers and taps), woodworking tools, various types of punches and dies, ball and roller bearings. The type M steels are used for cutting tools and various types of dies.
- metalworking
metalworking
Any manufacturing process in which metal is processed or machined such that the workpiece is given a new shape. Broadly defined, the term includes processes such as design and layout, heat-treating, material handling and inspection.
- milling
milling
Machining operation in which metal or other material is removed by applying power to a rotating cutter. In vertical milling, the cutting tool is mounted vertically on the spindle. In horizontal milling, the cutting tool is mounted horizontally, either directly on the spindle or on an arbor. Horizontal milling is further broken down into conventional milling, where the cutter rotates opposite the direction of feed, or “up” into the workpiece; and climb milling, where the cutter rotates in the direction of feed, or “down” into the workpiece. Milling operations include plane or surface milling, endmilling, facemilling, angle milling, form milling and profiling.
- pitch
pitch
1. On a saw blade, the number of teeth per inch. 2. In threading, the number of threads per inch.
- sawing
sawing
Machining operation in which a powered machine, usually equipped with a blade having milled or ground teeth, is used to part material (cutoff) or give it a new shape (contour bandsawing, band machining). Four basic types of sawing operations are: hacksawing (power or manual operation in which the blade moves back and forth through the work, cutting on one of the strokes); cold or circular sawing (a rotating, circular, toothed blade parts the material much as a workshop table saw or radial-arm saw cuts wood); bandsawing (a flexible, toothed blade rides on wheels under tension and is guided through the work); and abrasive sawing (abrasive points attached to a fiber or metal backing part stock, could be considered a grinding operation).
- sawing machine ( saw)
sawing machine ( saw)
Machine designed to use a serrated-tooth blade to cut metal or other material. Comes in a wide variety of styles but takes one of four basic forms: hacksaw (a simple, rugged machine that uses a reciprocating motion to part metal or other material); cold or circular saw (powers a circular blade that cuts structural materials); bandsaw (runs an endless band; the two basic types are cutoff and contour band machines, which cut intricate contours and shapes); and abrasive cutoff saw (similar in appearance to the cold saw, but uses an abrasive disc that rotates at high speeds rather than a blade with serrated teeth).
- stainless steels
stainless steels
Stainless steels possess high strength, heat resistance, excellent workability and erosion resistance. Four general classes have been developed to cover a range of mechanical and physical properties for particular applications. The four classes are: the austenitic types of the chromium-nickel-manganese 200 series and the chromium-nickel 300 series; the martensitic types of the chromium, hardenable 400 series; the chromium, nonhardenable 400-series ferritic types; and the precipitation-hardening type of chromium-nickel alloys with additional elements that are hardenable by solution treating and aging.
- tool steels
tool steels
Group of alloy steels which, after proper heat treatment, provide the combination of properties required for cutting tool and die applications. The American Iron and Steel Institute divides tool steels into six major categories: water hardening, shock resisting, cold work, hot work, special purpose and high speed.
- turning
turning
Workpiece is held in a chuck, mounted on a face plate or secured between centers and rotated while a cutting tool, normally a single-point tool, is fed into it along its periphery or across its end or face. Takes the form of straight turning (cutting along the periphery of the workpiece); taper turning (creating a taper); step turning (turning different-size diameters on the same work); chamfering (beveling an edge or shoulder); facing (cutting on an end); turning threads (usually external but can be internal); roughing (high-volume metal removal); and finishing (final light cuts). Performed on lathes, turning centers, chucking machines, automatic screw machines and similar machines.