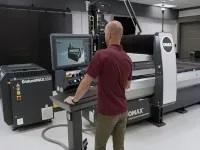
Shop owners and project managers are facing today’s potential skilled labor shortage head on by seeking solutions that allow them to maintain and, in many cases, expand their cutting capacity to meet demand today. In addition, their potential solution must set them up for success in the future.
In this blog post from OMAX Corp., the company details how technology can bridge the ongoing skills gap, and how its OptiMAX abrasive waterjet achieves both these current and future goals.
OptiMAX is designed for quickly turning drawings into parts with reduced dependency on highly experienced operators. The machine’s intuitive software is designed for ease of use for any skill level and allows for an operator to quickly start cutting with minimal training. OptiMAX’s software also provides data-driven system monitoring to avoid reducing downtime.
In addition, OptiMAX’s enhanced automation decreases the typical learning curve encountered by new operators. Equipped with a high-efficiency EnduroMAX pump that automatically sets the correct pressure and minimizes fluctuation, OptiMAX lessens the operator’s responsibilities while at the same time improves component life. A drive system with advanced motion control further enhances part accuracy without user intervention and increases OptiMAX’s reliability.
Thirty years of engineering expertise and user experience were put to work to develop an easy-to-use and versatile cutting system in OptiMAX that allows shops to keep up with today’s production demands. The same expertise and experience also pave a path toward the future. By creating an accessible machine for any skill level, shops regain time to develop and recruit talent. With OptiMAX, managers can take advantage of OMAX’s unlimited free training for everyone on their team. From machine operation to software instruction, new hires can build confidence and bridge the gap between their skills and veteran staff.
OptiMAX gives shops a solution to address the issue of skill labor shortages now while also providing the ability to plan for the future.
Contact Details
Related Glossary Terms
- abrasive
abrasive
Substance used for grinding, honing, lapping, superfinishing and polishing. Examples include garnet, emery, corundum, silicon carbide, cubic boron nitride and diamond in various grit sizes.
- abrasive waterjet ( AWJ)
abrasive waterjet ( AWJ)
System that uses high-pressure waterjets in combination with a slurry of fine abrasive grains to machine materials. See waterjet cutting.
- turning
turning
Workpiece is held in a chuck, mounted on a face plate or secured between centers and rotated while a cutting tool, normally a single-point tool, is fed into it along its periphery or across its end or face. Takes the form of straight turning (cutting along the periphery of the workpiece); taper turning (creating a taper); step turning (turning different-size diameters on the same work); chamfering (beveling an edge or shoulder); facing (cutting on an end); turning threads (usually external but can be internal); roughing (high-volume metal removal); and finishing (final light cuts). Performed on lathes, turning centers, chucking machines, automatic screw machines and similar machines.