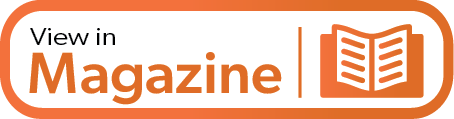
IMTS 2024 offered visitors an opportunity to browse through a number of new and improved workholding systems that reportedly will help shops streamline automation, improve precision and/or reduce downtime and setup times. What’s more, the following eight products highlighted here reflect key trends in automation, flexibility and maintenance-free operation — each of which are critical for staying competitive in today’s manufacturing sector.
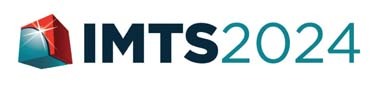
1. HAINBUCH America Corp. introduced new process automation for workpiece clamping with the unveiling of its Automated Change (AC) Line at IMTS 2024. With the company’s TOPlus AC and SPANNTOP AC chucks, clamping heads and workpiece end-stops can be changed automatically. The chucks enable unattended setup and manufacturing of workpieces with different clamping diameters, profiles and clamping lengths. The DockLock AC zero-point clamping system enables automated fixture change-over for both hydraulic and pneumatic versions. Hainbuch’s CENTREX duo AC and centroteX AC interfaces enable change-overs for entire clamping devices, and can be adapted to a shop’s unique requirements.
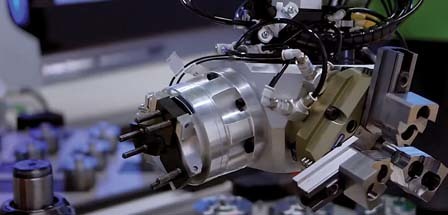
2. Mate Precision Technologies introduced a series of new enhancements for its 52/96 zero-point workholding system. Featured at Mate’s booth during IMTS 2024, the enhancements include the company’s new machinable hard jaws that allow users to create custom profiles from blank jaws. Also highlighted were Mate’s DynoGrip ER Collet Chucks for holding round parts during milling; the DynoGrip Direct Mount Vise with a wider body that provides additional flexibility and allows for direct bolting to a machine bed, pallet or other fixture, and the DynoMount Lower Profile Pyramid designed for more compact machining spaces.
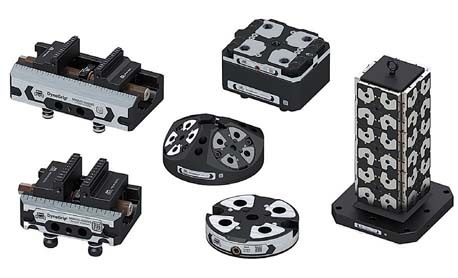
3. SMW Autoblok Corp. introduced its WPS XL (Workpiece Positioning System) featuring manual zero-point clamping that is best utilized for large workpieces. The WPS XL is said to be ideal for 5-axis machining, and is used for milling, measuring and grinding operations. With an emphasis on flexibility and speed, users reportedly can reduce their setup time by 90% or more with single quick actuation for rapid module operations in only three rotations. The new system features a pull-down force of 40 kN, holding force of 100 kN, maximum torque of 30 Nm, and repeatability of less than 0.01 mm.
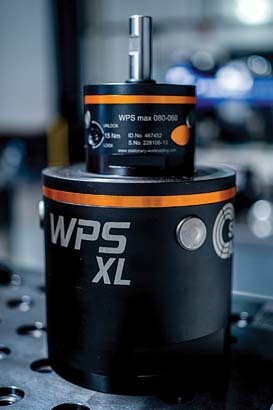
4. Royal Products highlighted its Royal Z-Lock zero-point workholding system designed for vertical, horizontal and 5-axis machining centers . The system, which does not require the installation of external air or hydraulic lines, takes just a few turns of a hex key to lock, and there is no risk of the top plate loosening from vibration, spring wear or air/hydraulic failure. The Royal Z-Lock system is said to achieve up to 11,240 lbs. (50 kN) of clamping force, and is capable of precision repeatability of 0.0001" in the X and Y axes, and 0.00005" in the Z axis.
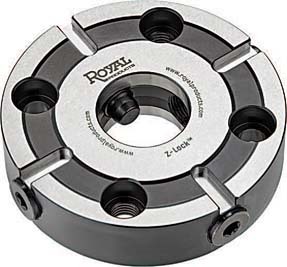
5. Kurt Workholding expanded its 5-axis workholding ecosystem with a range of new products, including three vise models, manual pallets, manual quick-release pallets, and pneumatic pallets with 96 mm zero-point docking. New vise models feature three snap-on, snapoff jaw options, easy adjustment and side pull-studs for automated pick and place. New PFW420, PFW440, and PFW460 models dock on the Kurt 96 mm pallets and other compatible 96 mm systems. Jaws can be easily changed while the vise is mounted in a machine or quickly removed and replaced with the turn of a hex bolt, push of a button or pneumatic actuation.
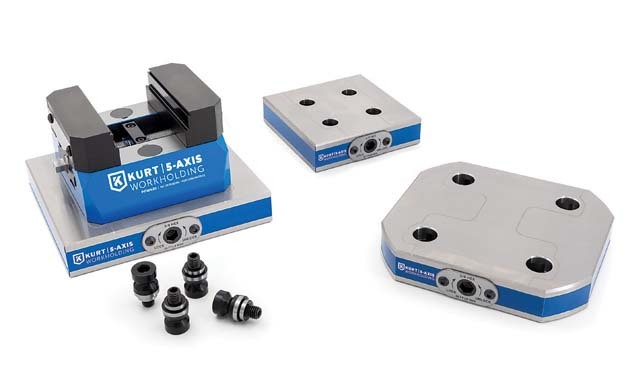
6. Jergens Inc. added to its line of Quick-Loc™ 5-axis workholding products with the Quick-Loc (QL2) combination pallet that features both 96 mm and 52 mm hole patterns for broad use quick-change fixturing on multiple machining platforms. The modular system, which features a 4-pull stud interface, allows operators to achieve fast, repeatable fixture changes of various types of top tooling with receivers. Top tooling is located and clamped to a base receiver in a single step when the pull studs are inserted into the receiver and the clamping screw is tightened.
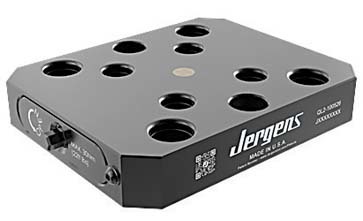
7. 5th Axis Inc.'s new LiteVise series made its debut shortly after IMTS 2024. Available in sizes of 5" x 6", 5" x 13", and 5" x 18", the LiteVise series is manufactured from a combination of highstrength aluminum alloy and steel, offering durability without the bulk and allowing for quick setup and easy handling . Other features of the LiteVise series, which is compatible with all 96 mm pull stud systems on the market, include its compact size allowing it to maximize workspace and flexibility in various CNC machines.
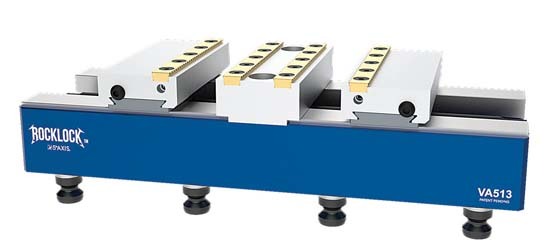
8. LANG Technik USA highlighted its Makro• Grip® family, which the company expanded to include the Micro vise and its counterpart the Quick•Point® Duo zero-point plate. The Makro• Grip Micro offers a 46 mm jaw width with a clamping range up to a maximum of 65 mm and can also be used on the matching Quick•Point 52 duo series — either alone or side by side. On the underside of the vise are only two clamping studs instead of four, making it possible to clamp two Micro vises in one Quick•Point® 52 zero-point plate
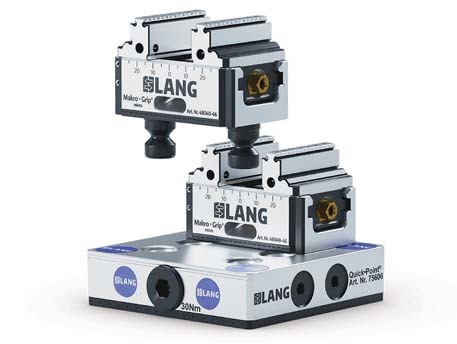
Related Glossary Terms
- centers
centers
Cone-shaped pins that support a workpiece by one or two ends during machining. The centers fit into holes drilled in the workpiece ends. Centers that turn with the workpiece are called “live” centers; those that do not are called “dead” centers.
- collet
collet
Flexible-sided device that secures a tool or workpiece. Similar in function to a chuck, but can accommodate only a narrow size range. Typically provides greater gripping force and precision than a chuck. See chuck.
- computer numerical control ( CNC)
computer numerical control ( CNC)
Microprocessor-based controller dedicated to a machine tool that permits the creation or modification of parts. Programmed numerical control activates the machine’s servos and spindle drives and controls the various machining operations. See DNC, direct numerical control; NC, numerical control.
- fixture
fixture
Device, often made in-house, that holds a specific workpiece. See jig; modular fixturing.
- gang cutting ( milling)
gang cutting ( milling)
Machining with several cutters mounted on a single arbor, generally for simultaneous cutting.
- grinding
grinding
Machining operation in which material is removed from the workpiece by a powered abrasive wheel, stone, belt, paste, sheet, compound, slurry, etc. Takes various forms: surface grinding (creates flat and/or squared surfaces); cylindrical grinding (for external cylindrical and tapered shapes, fillets, undercuts, etc.); centerless grinding; chamfering; thread and form grinding; tool and cutter grinding; offhand grinding; lapping and polishing (grinding with extremely fine grits to create ultrasmooth surfaces); honing; and disc grinding.
- milling
milling
Machining operation in which metal or other material is removed by applying power to a rotating cutter. In vertical milling, the cutting tool is mounted vertically on the spindle. In horizontal milling, the cutting tool is mounted horizontally, either directly on the spindle or on an arbor. Horizontal milling is further broken down into conventional milling, where the cutter rotates opposite the direction of feed, or “up” into the workpiece; and climb milling, where the cutter rotates in the direction of feed, or “down” into the workpiece. Milling operations include plane or surface milling, endmilling, facemilling, angle milling, form milling and profiling.