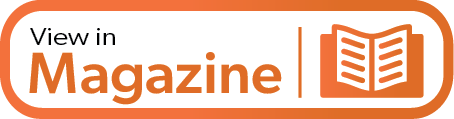
Carbide-tipped saw blades tend to be the go-to tool when cutting difficult-to-machine workpiece materials, such as titanium, stainless steel, heat-resistant superalloys and case-hardened metals. However, more and more end users are using them as an effective method for sawing more “run-of-the-mill” jobs and finding that they cut faster, impart finer surface finishes and can last about 20 percent longer than bimetal blades, according to Steve Yulga, director of sales and marketing for DoALL Sawing Products in Savage, Minnesota. “In a lot of instances, carbide can be a more cost-effective [cutting] method.”
The company produces four types of tungsten carbide-tipped bandsaw blades, along with various other saw blades, cutting fluids and sawing machines. Yulga said DoALL recently improved its T3P blade by enhancing the quality assurance and control when performing welding of the carbide to the tooth tips of the blade and to provide a more consistent product. The triple- chip carbide blade has a positive rake angle on its teeth to handle difficult-to-machine materials in high-production environments.
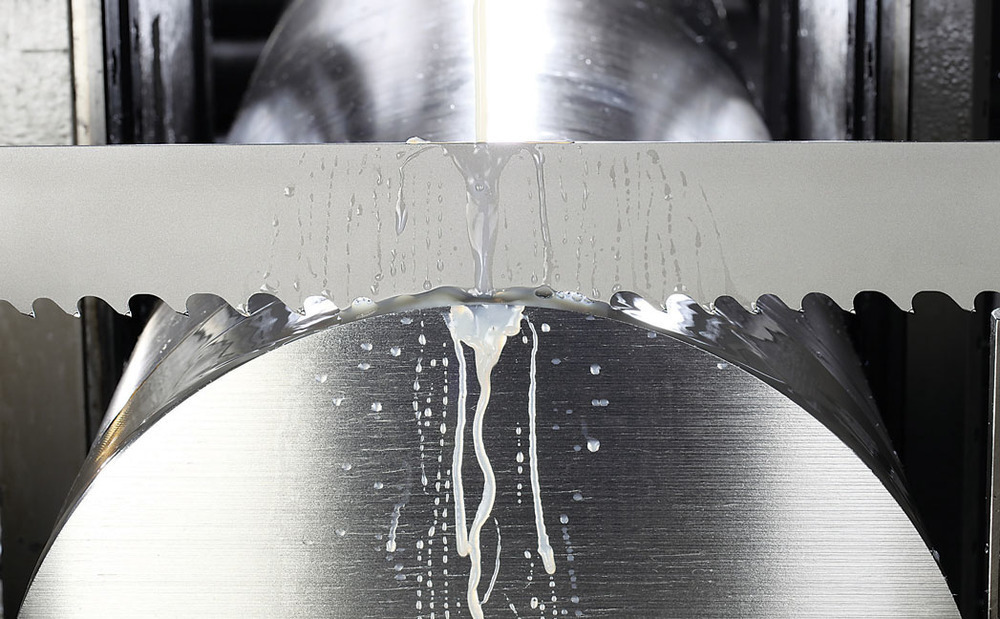
“The positive rake angle allows for the tool to grip and to create a chip. It has to really dig in hard.”
In contrast, the company’s T3N blade has a triple-chip negative rake for case-hardened, or heat induction- hardened, workpieces like cylinder rods and hydraulic shafts in which the saw has to cut through an outer surface that is harder than the core, Yulga explained. “The T3N really goes through that material like butter.”
For cutting abrasive materials such as cast aluminum, DoALL offers the STC carbide blade. The blade has a wide set tooth design to increase the cut channel and prevent or at least limit the amount of pinching on the backing of the blade due to the material tending to pinch the blade and cause premature wear or failure, he noted.
While the T3P is typically recommended for sawing materials 152.4 mm (6") in diameter or less, the company makes the T7P for larger diameter workpieces. Yulga said that the T7P has five unique cutting surfaces ground into the carbide barrels for enhanced penetration compared to the three grinds on a triple chip. “You have more surface area that is actually cutting. The big secret sauce is the grind, making the multiple cutting surfaces on the tooth tip.” He added that the tooth tip has a trapezoidal design.
Sharing the Load
When it comes to carbide-tipped bandsaw blades, Wikus Saw Technology Corp. manufactures its blades in a variety of carbide grades and tooth geometries at the cutting edge, said Mike Masters, chief technology officer for the Addison, Illinois- based bandsaw blade manufacturer.
The trapezoidal-ground teeth on the carbide portion, which is wider than the blade itself, remove material in a broaching-like fashion while creating the kerf, he explained, starting small and becoming larger sequentially to widen the machined path. “The first tooth is very sharp. The edges are beveled, which makes it similar to having a pilot drill in a drilling application, keeping the blade centered in the cut.”
Masters added that after the initial tooth makes a cut, the tooth behind it removes material on the left and right of the path that the previous tooth missed and the next tooth repeats the process. In one tooth design, for example, Wikus grinds four teeth to create seven chips, and each tooth exerts symmetrical pressure. “It’s not pushing on the left harder or on the right harder like it would with a set style tooth as the teeth enter and exit the cut. It’s sharing the load. At the same time, you get a nice, straight, smooth cut.”
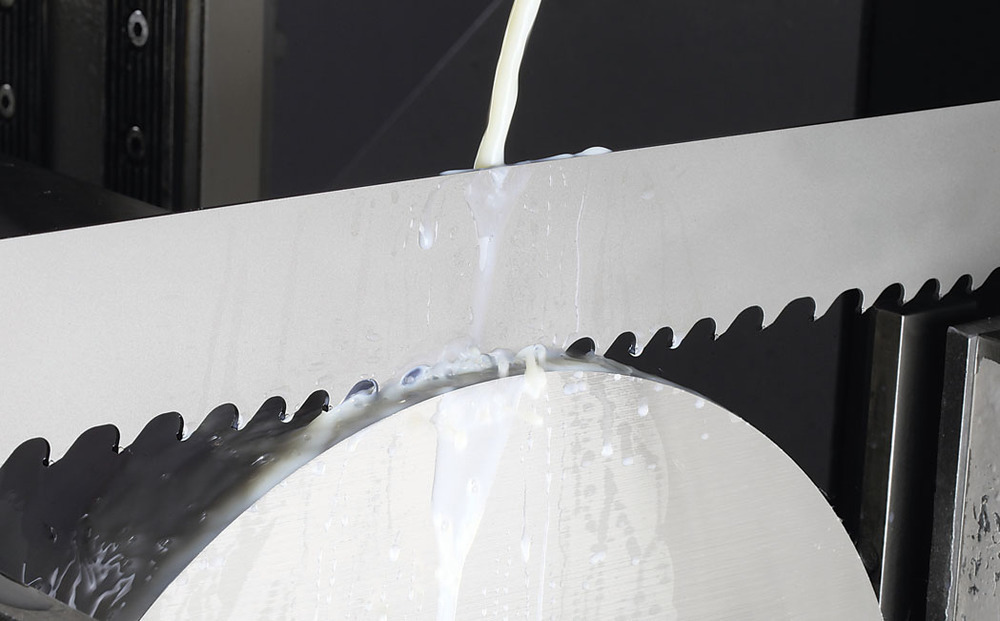
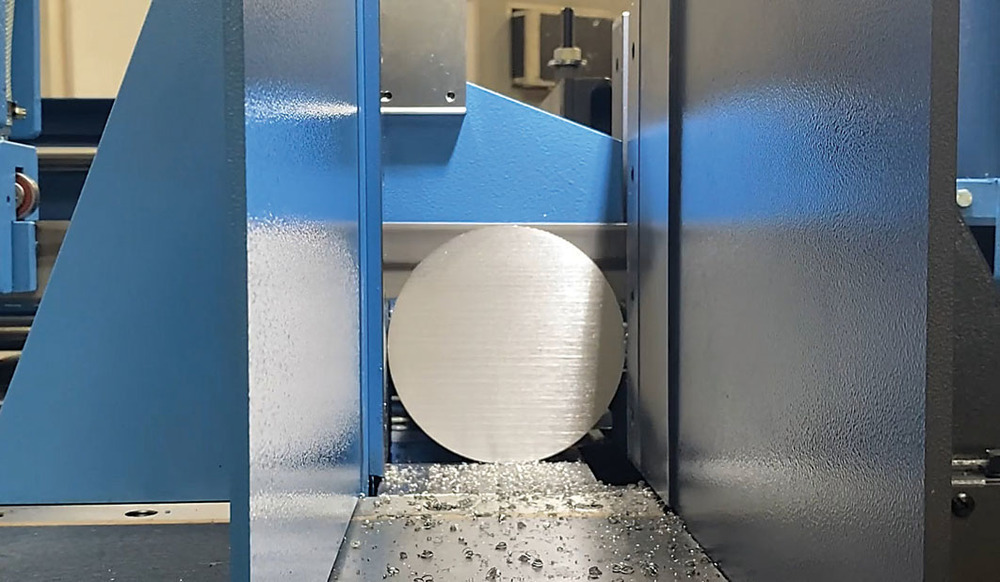

Another tooth design features three ground teeth to pull five chips. While a blade generating five chips may impart a slightly different surface finish than a blade that pulls seven chips, the five-chip blade can remove material quicker due to the variation in chip widths. “It likes using coarse sandpaper versus fine sandpaper.”
Because end users are looking for the best blade at the lowest price, Masters said Wikus offers a line of carbide-tipped blades that includes good, better and best. The Taurus offering is a relatively inexpensive level one blade for sawing all steel and nonferrous metals. “When people are looking to go from applying bimetal to carbide, sometimes that sticker price shock keeps them from doing that, so many manufacturers offer an introductory or general-purpose carbide blade. It’s to show what a carbide blade is capable of doing. You can run it at faster speeds (compared to bimetal) because it accepts more heat.”
Moving up the line, the company reports that its Futura blade, as well as the Futura VA, 718, NE and NE RS offerings, is a level three product — best. Featuring a ground trapezoid tooth with a positive rake angle and optimized chip division, the blade provides high cutting performance to boost productivity, high wear resistance to extend tool life and low cutting forces to achieve smooth, straight cuts.
The carbide grade is one element that impacts blade price. The grade is also targeted towards specific applications, Masters noted. Carbide that provides high abrasion resistance is suitable for sawing nonferrous metals, which generally contain a lot of impurities. In contrast, harder carbide grades tolerate higher temperatures and provide more wear resistance, making them a better fit for cutting steel alloys.

Raking it in
Just like bimetal blades, the carbide blades come in various rake angles. They can range from negative, neutral and positive offerings, based on the application and the desired results in performance and tool life, Masters said. In connection with the rake angle, a blade has a specific geometry to allow penetration into the workpiece.
A softer steel generally does not require a very high positive rake angle to be cut effectively, he added, but metals that are more prone to workharden and nickel-based alloys do perform better when using the higher angles to create a desired chip and still keep the heat to a minimum. “A positive rake angle comes in to shave and lift the chip.”
A negative rake angle is appropriate for sawing case-hardened materials. To saw through the hard casing, which might be as hard as 62 HRC or harder, a significant amount of heat must be generated, Masters said. Unlike a positive rake, a negative rake compresses and plows the work to create a very hot chip. A level of heat that is near the materials forging temperature, which is nearing melting temperature.
“When you use one of the negative rakes,” he said, “you’re going to see a few sparks, you’re going to see blue and brown chips coming out, but that’s the whole idea. The goal is to push enough heat into the chip to soften it and push it out quickly, so you’re using a negative rake, a high rate of blade speed and a lot of feed pressure.”
Carbide accepts heat effectively, but Wikus also offers carbide-tipped bandsaw blades with a hard coating to act as an additional layer of insulation to protect against both heat and wear resistance, Masters said. A coated blade allows for faster blade speeds and additional feed to be used, as well as longer tool life. The coatings include titanium nitride, aluminum titanium nitride and others. Each is specific to the various applications they will be exposed to.
Pat Mooney Inc. is also a source for carbide blades, as well as other types and saws and other machine tools. The company distributes Bahco carbide-tipped bandsaw blades, Kanefusa carbide-tipped cold saw blades for nonferrous materials and Segmetal solid- carbide slitting saw blades for precise slotting applications.
When it comes to coating blades, Brian Thornton, account manager for the Addison, Illinois, company, said up to 70 percent of them are sold uncoated, especially Kanefusa blades. “A lot of times, uncoated blades from Kanefusa will outperform a coated blade from a competitor.”
DoALL does not sell any coated blades, Yulga noted, explaining, “We believe it’s just an added cost, and we haven’t seen that much benefit to justify the added expense.”
Refurbishing Blades
Wikus and DoALL do not offer blade resharpening services, but Pat Mooney resharpens nonferrous tungsten carbide-tipped blades, Thorton said, and recommends three to five resharpenings before the carbide tip gets too small and the angle on the tooth form does not perform properly.
The company also resharpens solid-carbide slitting saw blades on one of its two Nishijimax TNC-450F grinders. Because solid-carbide blades are small, thin and easily breakable, Pat Mooney recommends that only trained sawing professionals should resharpen them.
The Toughest Material Deserves the Toughest Blade - Tungsten Carbide
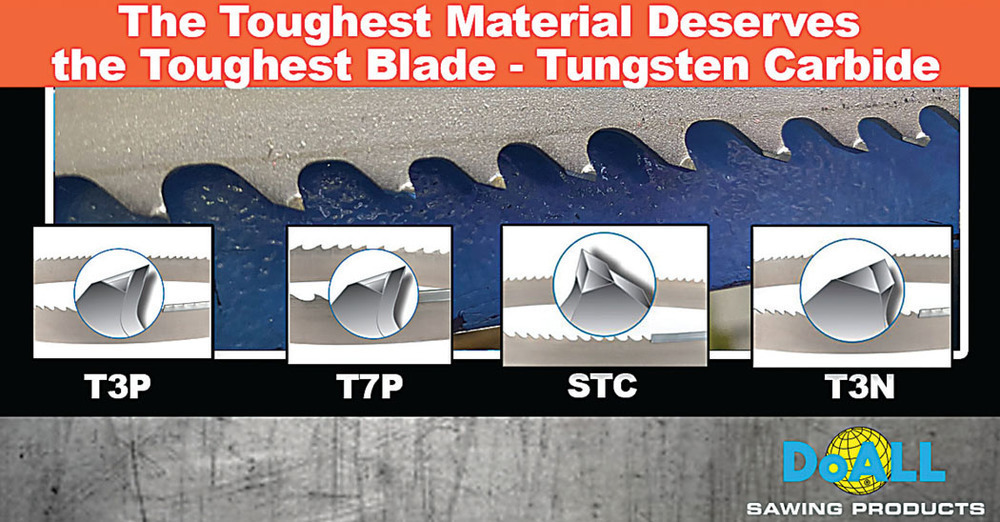
“Those tend to have fewer resharpenings but two to three is reasonable,” Thorton said.
However, with thin-kerf carbide-tipped blades being the industry standard for ferrous applications, Thorton noted that those blades are discarded without resharpening them. “That’s going to allow you to get more parts with less material loss, and you can use the blade until it fails because it’s not designed to be sharpened.”
In addition to the conventional triple-chip tooth design, or D type, in which the first tooth takes the chip out of the middle and then the following tooth takes chips out of both sides to remove material, Thorton said Pat Mooney also offers the California triple chip, or 3DX, which performs the same process over three teeth. “This is very common in the nonferrous world.” Another available grind is BC-5 type for thin-walled tube.
For job shops and other manufacturing environments that saw a wide range of materials and shapes, he noted that Pat Mooney offers the Easy-Cut bandsaw blades from Bahco with a tooth design for general- purpose cutting. The blade is suitable for sawing solids, pipes, profiles or bundles.
Thorton added that Pat Mooney also supplies Bahco’s Extreme Easy-Cut carbide bandsaw blades, which are more forgiving that a conventional blade. Bahco reports that the blades have a set pattern that gives a bigger span in cutting width, enables fast cutting and operational agility, provides a low cost per cut, and can be used in the same applications as bimetal blades.
Cool Cutting
Flood coolant is still common in the bandsaw world, especially when sawing more exotic, difficult-to-machine metals because flood coolant allows the workpiece and blade to be cooled at a higher rate than mist coolant, Thorton said. Mist coolant is more common for production applications in which a semisynthetic or specially formulated vegetable oil is mixed with air and gets atomized and applied to cool the blade/workpiece interface. Straight air, however, is not recommended because it won’t provide enough cooling to prevent the teeth from degrading prematurely, and the blade can impart a poor surface finish that negatively impacts downstream applications.

As manufacturers increasingly adopt automation, they are placing greater focus on surface finish, squareness and tolerance when sawing. “The more automated the process, the fewer defects and mistakes you want to have in all your upstream processes.”
Nonetheless, Yulga noted that some materials must be cut dry or at least without oil-based coolant because of contamination concerns. That is the case for a DoALL customer that cuts titanium spinal implants with one of its saws and carbide blades.
In the majority of cutting applications, carbide blades typically use flood coolant to keep the cutting tip cool and lubricated while mist coolant is often preferred when sawing aluminum at high speeds, Masters noted. An exception to the use of coolant is when sawing with the negative rake angle. The heat being created at the cutting edge is the intent and the introduction of flood coolant may introduce thermal shock to the carbide tips and cause them to fracture. Instead, Masters advises dripping coolant every few seconds or so to simply lubricate the sides of the blades but not flood the blade.
When targeting a carbide-tipped saw blade for a specific application, Masters emphasized the need to understand the complete process, including knowing the specifics of the workpiece material, the bandsaw machine, and the desired outcome. “It’s not just the blade. The blade is the smallest variable. Other factors are the machine operator’s knowledge, the condition of the machine, the condition of the coolant. There are so many things that weigh into it.”
Related Glossary Terms
- abrasive
abrasive
Substance used for grinding, honing, lapping, superfinishing and polishing. Examples include garnet, emery, corundum, silicon carbide, cubic boron nitride and diamond in various grit sizes.
- alloys
alloys
Substances having metallic properties and being composed of two or more chemical elements of which at least one is a metal.
- backing
backing
1. Flexible portion of a bandsaw blade. 2. Support material behind the cutting edge of a tool. 3. Base material for coated abrasives.
- bandsaw
bandsaw
Machine that utilizes an endless band, normally with serrated teeth, for cutoff or contour sawing. See saw, sawing machine.
- bandsaw blade ( band)
bandsaw blade ( band)
Endless band, normally with serrated teeth, that serves as the cutting tool for cutoff or contour band machines.
- coolant
coolant
Fluid that reduces temperature buildup at the tool/workpiece interface during machining. Normally takes the form of a liquid such as soluble or chemical mixtures (semisynthetic, synthetic) but can be pressurized air or other gas. Because of water’s ability to absorb great quantities of heat, it is widely used as a coolant and vehicle for various cutting compounds, with the water-to-compound ratio varying with the machining task. See cutting fluid; semisynthetic cutting fluid; soluble-oil cutting fluid; synthetic cutting fluid.
- feed
feed
Rate of change of position of the tool as a whole, relative to the workpiece while cutting.
- gang cutting ( milling)
gang cutting ( milling)
Machining with several cutters mounted on a single arbor, generally for simultaneous cutting.
- kerf
kerf
Width of cut left after a blade or tool makes a pass.
- quality assurance ( quality control)
quality assurance ( quality control)
Terms denoting a formal program for monitoring product quality. The denotations are the same, but QC typically connotes a more traditional postmachining inspection system, while QA implies a more comprehensive approach, with emphasis on “total quality,” broad quality principles, statistical process control and other statistical methods.
- rake
rake
Angle of inclination between the face of the cutting tool and the workpiece. If the face of the tool lies in a plane through the axis of the workpiece, the tool is said to have a neutral, or zero, rake. If the inclination of the tool face makes the cutting edge more acute than when the rake angle is zero, the rake is positive. If the inclination of the tool face makes the cutting edge less acute or more blunt than when the rake angle is zero, the rake is negative.
- sawing
sawing
Machining operation in which a powered machine, usually equipped with a blade having milled or ground teeth, is used to part material (cutoff) or give it a new shape (contour bandsawing, band machining). Four basic types of sawing operations are: hacksawing (power or manual operation in which the blade moves back and forth through the work, cutting on one of the strokes); cold or circular sawing (a rotating, circular, toothed blade parts the material much as a workshop table saw or radial-arm saw cuts wood); bandsawing (a flexible, toothed blade rides on wheels under tension and is guided through the work); and abrasive sawing (abrasive points attached to a fiber or metal backing part stock, could be considered a grinding operation).
- sawing machine ( saw)
sawing machine ( saw)
Machine designed to use a serrated-tooth blade to cut metal or other material. Comes in a wide variety of styles but takes one of four basic forms: hacksaw (a simple, rugged machine that uses a reciprocating motion to part metal or other material); cold or circular saw (powers a circular blade that cuts structural materials); bandsaw (runs an endless band; the two basic types are cutoff and contour band machines, which cut intricate contours and shapes); and abrasive cutoff saw (similar in appearance to the cold saw, but uses an abrasive disc that rotates at high speeds rather than a blade with serrated teeth).
- slotting
slotting
Machining, normally milling, that creates slots, grooves and similar recesses in workpieces, including T-slots and dovetails.
- superalloys
superalloys
Tough, difficult-to-machine alloys; includes Hastelloy, Inconel and Monel. Many are nickel-base metals.
- titanium nitride ( TiN)
titanium nitride ( TiN)
Added to titanium-carbide tooling to permit machining of hard metals at high speeds. Also used as a tool coating. See coated tools.
- tolerance
tolerance
Minimum and maximum amount a workpiece dimension is allowed to vary from a set standard and still be acceptable.
- tungsten carbide ( WC)
tungsten carbide ( WC)
Intermetallic compound consisting of equal parts, by atomic weight, of tungsten and carbon. Sometimes tungsten carbide is used in reference to the cemented tungsten carbide material with cobalt added and/or with titanium carbide or tantalum carbide added. Thus, the tungsten carbide may be used to refer to pure tungsten carbide as well as co-bonded tungsten carbide, which may or may not contain added titanium carbide and/or tantalum carbide.
- wear resistance
wear resistance
Ability of the tool to withstand stresses that cause it to wear during cutting; an attribute linked to alloy composition, base material, thermal conditions, type of tooling and operation and other variables.