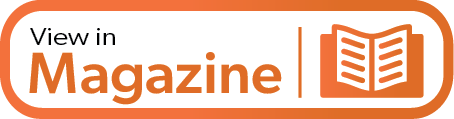
Part manufacturers with machine shops have advantages compared to other manufacturers when incorporating additive manufacturing (AM), or 3D printing, to their capabilities for producing metal parts, according to Joel Sam, metals business development manager for EOS North America. That’s because job shops typically have CNC machine tools, including wire EDMs and bandsaws, as well as cutting tools and post-processing equipment such as media blasting that complement metal AM.
“This is why I always say that machine shops have a leg up when it comes to getting into metal 3D printing. Other customers who don’t already have that equipment – it’s a lot bigger ask.” Sam said. “With plastic printing, sometimes you can just take it out of the printer and you’re ready to go, but with laser powder bed fusion, you have to product separate the metal from the build plate, so you need a wire EDM or bandsaw to do that.”
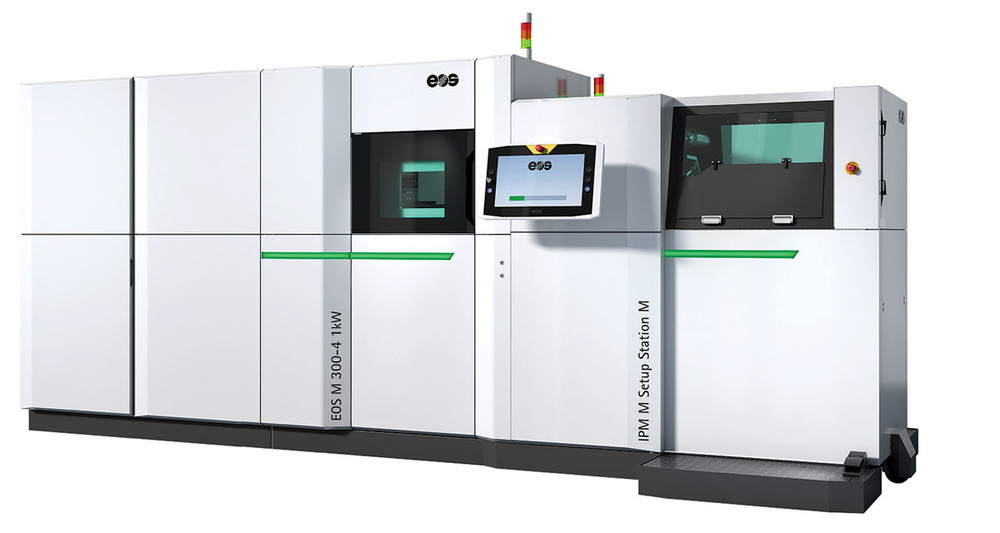
Sam also noted that the surface finish of printed metal parts is generally a bit rough and must be finished on a CNC machine or with a secondary process. That requirement is particularly important when, for example, there is a sealing surface or a feature that requires tight concentricity.
EOS North America has regional offices at its technical centers in Novi, Michigan, and Pflugerville, Texas, and offers laser powder bed fusion, or Direct Metal Laser Solidification (DMLS), technology for 3D printing metal parts, selective laser sintering technology for plastic 3D printing, and materials for both technologies.
Nonetheless, machine shops must overcome a couple of key barriers to successfully implement metal AM, Sam said. The first is expertise. Shops, such as contract manufacturers, employ workers with a range of machining skills, such as knowing the proper speeds and feeds needed for a job, understanding how to read blueprints, and performing CAD/CAM programming. AM, however, requires new skills, such as using 3D printing- specific software.
For example, EOS offers EOSPRINT software that, according to the company, allows end users to assign and optimize process parameters for industrial 3D printing on EOS systems. It calculates the exact path of the laser in the production process to optimize build speed and part quality.
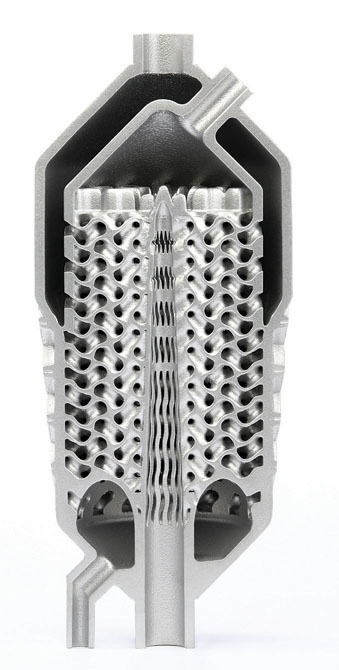
“If you just have an STL file, which historically has been the standard 3D printing file,” Sam said, “you can drop it into EOSPRINT directly and print it if it’s completely printable.”
EOS continually strives to make its software more intuitive, Sam added, because safety is the main way that operators interact with the print on the front end. Traditional manufacturing software, such as CAD/CAM, is developed with conventional machining in mind, but new software is required for topology optimization and other AM-specific design processes.
Artificial intelligence is also entering the AM design picture to boost efficiency, he noted. “You enter in your limits or your design points, and the computer can do the work for you.”
Gaining Knowledge
Metal AM education and training for shop staff is critical for efficiently and profitably printing parts, Sam added. EOS has a training team based at its Metro Detroit Additive Minds Academy Center that travels to customer sites and shows operators how to use EOS technology. In addition, Sam emphasized the need for end users to comprehend the design-for-manufacturing principle, which is covered in an online course he teaches as part of the EOS Additive Minds Academy. The course also covers the types of geometries that are buildable – or not buildable – and the impact that changing laser parameters has on the build process.
The Additive Minds Academy, the EOS workforce development and education arm, provides comprehensive training programs for AM education, onboarding, upskilling and reskilling. The academy also offers continuous learning opportunities for companies using EOS technology.
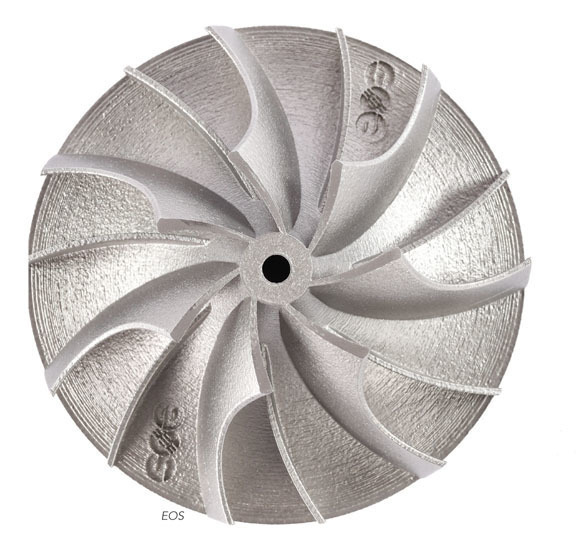
Even companies without an AM machine can visit an EOS training center for guidance on the process, the necessary software and machine operation. The training and education enable manufacturers to build on the technical aptitude that their machining personnel already have for mechanical and manufacturing engineering.
Sam emphasized the need for more specialized AM training in the industry, noting “that’s what we’re trying to do [with] that online content and in-person training.”
Another barrier to AM adoption, Sam added, is the relatively high cost of the equipment. Industrial 3D printers are a sizeable investment, with varying prices dependent on factors such as platform type, laser power, build volume and customization needs.
On top of the price is the trial and error required to learn a new technology. “When you’re building parts for a customer, you typically want to have first-time success,” Sam said, “and with 3D printing, if you’re new to it, it’s going to take a few tries to figure it out.”
A machine shop could outsource 3D printing to a service bureau, Sam noted, adding that he worked for a bureau before joining EOS that had 17 EOS machines, as well as in-house CNC machining, heat treatment and a coordinate measuring machine and surface profile scanner. Bringing AM in-house can be done in “baby steps,” starting with one piece of equipment and expanding as expertise and business grows.
Controlling Quality
Although the majority of metal part manufacturers already have a quality control (QC) department, they might have to learn new QC techniques that are more unique to additive, Sam said. For instance, destructive tensile testing is familiar in conventional manufacturing where a controlled tension is applied to a sample until it fully fails. A metal AM part, on the other hand, might require optical microscopy to ensure that there are no pores in a print. “If something goes wrong with the laser parameters for some reason, or the parameters aren’t optimized, you’re going to see porosity.”
Performing surface profile measurements with a laser scanner is another nondestructive QC test, which exists in conventional manufacturing but is more common for AM parts, according to Sam. That is because 3D printed parts usually have organic curvatures that don’t have many datum surfaces. “You can’t really put it on a CMM for every single measurement. We still use CMMs, but we often have to do surface profiles because the whole reason we’re doing 3D printing is so that we can print these organic surfaces that are not just flat angles and circles.”
Hybrid Approach
With the exception of “extremely custom machines” for special applications such as printing using multiple materials, Sam said laser powder bed fusion equipment is not well suited for hybrid machining, which allows shops to perform additive manufacturing and subtractive machining in one machine. “You have to have somewhere to get rid of your chips, and there’s just not a good place.”
Directed energy deposition (DED) is a more appropriate technology for hybrid production, according to Sam, but DED can neither achieve the tighter tolerances that are possible with laser powder bed fusion nor provide parts that have the full density and strength of a conventional metal. “With DED, you’re going to have more porosity.”
Instead, laser powder bed fusion is suitable for a different type of hybrid machining that involves removing a damaged portion of a broken part – via wire EDMing, for example – so the workpiece has a horizontal face, Sam explained. The flat surface is then printed on top of it to fix the part. “That’s hybrid because the bottom section is machined and then there’s a flat line and above that line everything is printed.”
He noted that the major applications are for tool repair and inserts for automotive die casting.
As AM adoption continues to grow among CNC machine shops, EOS is busy advancing technologies to enhance laser powder bed fusion. One development is in situ monitoring, which performs real-time quality assessment so users don’t have to wait until a build is completed before determining if a part is free of defects. With in situ monitoring, a camera is installed inside the build chamber to monitor the melt pool as the laser passes through the metal.
“By looking at the temperature gradients, looking at those camera images, you can assess if you’ve got a hot spot or a pore there,” Sam said. “That’s one of the big buzz phrases in the additive industry is doing quality control inside the machine, so if you see a problem, you can stop the build right there. You don’t waste any more powder, time or money finishing something that is scrap.”
Another development is support-free printing, which EOS offers with its Smart Fusion software, Sam noted. The software observes where there is overheating in a part being built, which is a primary cause of defects. When overheating is observed, the software dynamically throttles back the laser power to prevent defects. For example, the power setting can be lowered from 300 watts to 290 watts for a specific section, such as an overhang.
With the ability to transfer thermal energy away from specific part features, Sam added that a minimal number of supports are needed, reducing the overall build time, material consumption and post processing time. Some supports are still required, but the software could reduce the amount by up to 80% or 90% for a given part. “It’s cheaper and faster start to finish.”
Passion for Printing
Zeal Lifestyle Ltd. in Surrey, U.K., focuses on making stylish, functional and adaptable mobility aids for supported living. The company’s journey began when its two founders — Georgia Williams and Joshua King — independently looked into purchasing a walker for family members. Before that, though, both founders studied industrial design at Brunel University in London and worked at other companies.
During the COVID pandemic lockdowns, Willaims’ great aunt, at 86 years old, needed a walker to use indoors and outdoors to support her mobility. Despite an extensive search, Williams could not find a walker that matched her great aunt’s stylish tastes and personality. As Williams learned, resistance to using mobility aids is a common obstacle encountered by caregivers, in terms of both the denial that an assistive aid is necessary and the resentment that comes from having to purchase a device that often looks and feels limited and unappealing.
Williams and King took matters into their own hands and designed a walker that put the end user first. Late last year, Zeal began taking pre-orders after receiving awards for its usercentered design. Zeal will fill those pre-orders and begin direct retail sales at the company’s official launch scheduled for this summer.
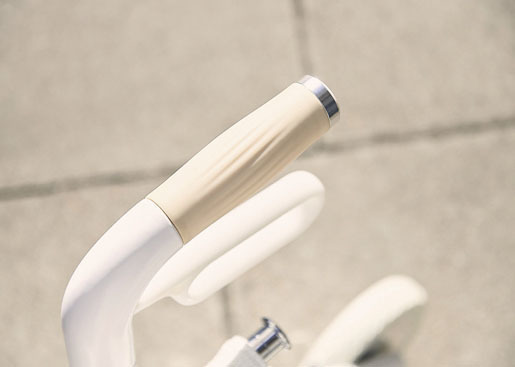
The Zeal walker is coming to market following four years of collaboration with users and a comprehensive product development process commonplace for a Class 1 medical device that must adhere to specific ISO standards. Zeal’s mission is to remove the stigma of walkers and mobility aids, and provide a product that users like.
To prototype the plastic parts, the Zeal team worked with London-headquartered print bureau 3D People Ltd. The development of the mobility aid was complex and required numerous functional prototypes during the iterative process. The first fully functional walker prototype was made with 3D-printed parts for testing size and human interactions. Utilizing selective laser sintering (SLS) and Multi Jet Fusion (MJF) processes offered by 3D People – along with its finishing options – ensured Zeal quickly received high-quality parts.
“Over the past year, we’ve ordered around 500 parts in SLS and MJF for various prototypes and design iterations,” King said. “The MJF process is great for parts that need to be smooth. After post-processing, it’s hard to tell them apart from injection-molded parts. SLS works better for visual parts since the off-white finish is more aesthetically pleasing than MJF’s dark gray.
We switch between the two different processes, depending on the stage of design. Costs are also important, of course, and these can also vary based on part size and process used, so that’s something we factor in too, but it’s an easy thing.”
High quality is critical for functional prototypes that have to go through stringent testing, King added. “The quality of the parts from 3D People has been consistently excellent. Everything we’ve received has been accurate, and there’s been very little need for extra finishing before testing. Any issues we have had were sorted quickly by the team, which has made the whole process much easier.”
When finishing was required, multiple options are available from 3D People, including dedicated vapor smoothing, vibro-polishing and dyeing. King said Zeal found the vapor smoothing option invaluable for a number of parts and for different reasons. “Vapor smoothing gives the parts a polished look and makes them feel nicer. It also saves us from having to do extra finishing work later, which has been a big time-saver. Vapor smoothing can also give a more waterproof finish, which is easy to wipe clean. That was really useful for us because unfinished parts get dirty really quickly and easily, which is not ideal when undertaking multiple user tests.”
Related Glossary Terms
- bandsaw
bandsaw
Machine that utilizes an endless band, normally with serrated teeth, for cutoff or contour sawing. See saw, sawing machine.
- centers
centers
Cone-shaped pins that support a workpiece by one or two ends during machining. The centers fit into holes drilled in the workpiece ends. Centers that turn with the workpiece are called “live” centers; those that do not are called “dead” centers.
- computer numerical control ( CNC)
computer numerical control ( CNC)
Microprocessor-based controller dedicated to a machine tool that permits the creation or modification of parts. Programmed numerical control activates the machine’s servos and spindle drives and controls the various machining operations. See DNC, direct numerical control; NC, numerical control.
- die casting
die casting
Casting process wherein molten metal is forced under high pressure into the cavity of a metal mold.
- electrical-discharge machining ( EDM)
electrical-discharge machining ( EDM)
Process that vaporizes conductive materials by controlled application of pulsed electrical current that flows between a workpiece and electrode (tool) in a dielectric fluid. Permits machining shapes to tight accuracies without the internal stresses conventional machining often generates. Useful in diemaking.
- flat ( screw flat)
flat ( screw flat)
Flat surface machined into the shank of a cutting tool for enhanced holding of the tool.
- lapping compound( powder)
lapping compound( powder)
Light, abrasive material used for finishing a surface.
- quality assurance ( quality control)
quality assurance ( quality control)
Terms denoting a formal program for monitoring product quality. The denotations are the same, but QC typically connotes a more traditional postmachining inspection system, while QA implies a more comprehensive approach, with emphasis on “total quality,” broad quality principles, statistical process control and other statistical methods.
- sintering
sintering
Bonding of adjacent surfaces in a mass of particles by molecular or atomic attraction on heating at high temperatures below the melting temperature of any constituent in the material. Sintering strengthens and increases the density of a powder mass and recrystallizes powder metals.
- wire EDM
wire EDM
Process similar to ram electrical-discharge machining except a small-diameter copper or brass wire is used as a traveling electrode. Usually used in conjunction with a CNC and only works when a part is to be cut completely through. A common analogy is wire electrical-discharge machining is like an ultraprecise, electrical, contour-sawing operation.