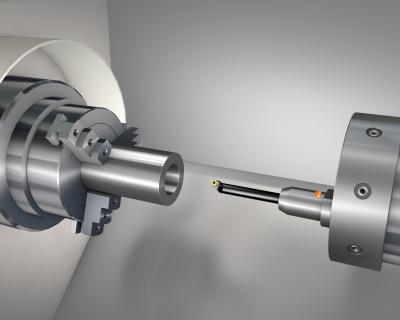
Sandvik Coromant has introduced a high-precision hydraulic chuck for turning operations that offers enhanced pull-out security. CoroChuck 935 has been designed to deliver fast, rigid and secure clamping, time after time.
With clamping security assured, machine shops can confidently perform demanding turning operations, including those with long overhangs. In fact, CoroChuck 935 ensures a clamping length of four times the bar diameter. Developed for use on lathes, turning centers and multi-task turn-mill machines, the new hydraulic chuck covers most common machine interfaces.
“The design principal behind the high level of security offered by CoroChuck 935 is based on fulcrum technology,” explains Åke Axner, global product manager – machine integration at Sandvik Coromant. “A thin, brazed membrane offers an optimized clamping function, whereby expansion creates two distinct clamping points on each side (fulcrums). The concept ensures the clamping force repeats for every use, providing the best possible pull-out resistance and damping performance.”
Further benefits of the new chuck include the use of EasyFix sleeves to provide the correct center height and help reduce set-up time. EasyFix sleeves are a solution for cylindrical boring bars that sees a spring plunger mounted in the sleeve click into a groove on the bar to guarantee the correct center height. The metallic sealing also offers good performance in applications that require high pressure coolant. Moreover, EasyFix facilitates improved cutting action and insert life.
CoroChuck 935 is available in 20 and 25 mm bore sizes ( ¾ and 1 inch) to suit Coromant Capto, HSK-A/C/T, cylindrical shank and VDI machine interfaces. Imperial sizes are available in Coromant Capto and cylindrical shank interfaces.
Contact Details
Related Glossary Terms
- boring
boring
Enlarging a hole that already has been drilled or cored. Generally, it is an operation of truing the previously drilled hole with a single-point, lathe-type tool. Boring is essentially internal turning, in that usually a single-point cutting tool forms the internal shape. Some tools are available with two cutting edges to balance cutting forces.
- centers
centers
Cone-shaped pins that support a workpiece by one or two ends during machining. The centers fit into holes drilled in the workpiece ends. Centers that turn with the workpiece are called “live” centers; those that do not are called “dead” centers.
- chuck
chuck
Workholding device that affixes to a mill, lathe or drill-press spindle. It holds a tool or workpiece by one end, allowing it to be rotated. May also be fitted to the machine table to hold a workpiece. Two or more adjustable jaws actually hold the tool or part. May be actuated manually, pneumatically, hydraulically or electrically. See collet.
- coolant
coolant
Fluid that reduces temperature buildup at the tool/workpiece interface during machining. Normally takes the form of a liquid such as soluble or chemical mixtures (semisynthetic, synthetic) but can be pressurized air or other gas. Because of water’s ability to absorb great quantities of heat, it is widely used as a coolant and vehicle for various cutting compounds, with the water-to-compound ratio varying with the machining task. See cutting fluid; semisynthetic cutting fluid; soluble-oil cutting fluid; synthetic cutting fluid.
- shank
shank
Main body of a tool; the portion of a drill or similar end-held tool that fits into a collet, chuck or similar mounting device.
- turning
turning
Workpiece is held in a chuck, mounted on a face plate or secured between centers and rotated while a cutting tool, normally a single-point tool, is fed into it along its periphery or across its end or face. Takes the form of straight turning (cutting along the periphery of the workpiece); taper turning (creating a taper); step turning (turning different-size diameters on the same work); chamfering (beveling an edge or shoulder); facing (cutting on an end); turning threads (usually external but can be internal); roughing (high-volume metal removal); and finishing (final light cuts). Performed on lathes, turning centers, chucking machines, automatic screw machines and similar machines.