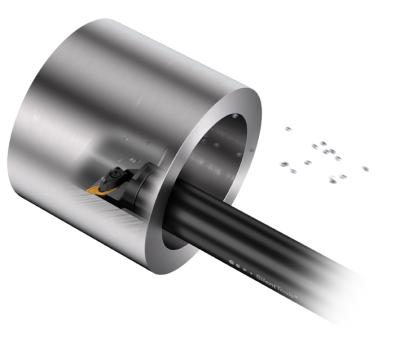
Following last year’s launch of PrimeTurning methodology and tools for external turning operations, Sandvik Coromant is introducing a dedicated CoroTurn Prime SL head that makes this process available for internal turning operations. The new SL head will meet the needs of oil and gas, aerospace and other manufacturers that machine diameters in excess of 90 mm (3.5 inches) and overhangs up to 8–10×D.
“The inside-out machining capability provided by the CoroTurn Prime SL head solution in combination with PrimeTurning techniques promotes excellent chip evacuation and chip control,” states Hakan Ericksson, product manager – general turning, Sandvik Coromant. “In turn, manufacturers can achieve an excellent surface finish matched by high productivity, longer tool life and high machine utilization.”
In contrast to conventional internal turning, PrimeTurning sees the tool enter the material at the chuck end of the component and remove metal as it travels back out toward the bore exit (inside-out direction). This allows for the application of a small entering angle, which offers significant productivity gains. However, if required, another version is also available with a reversed tip seat that makes it possible to perform PrimeTurning in the opposite direction (outside-in).
The two insert types for internal PrimeTurning are: A-type for profiling, finishing and light roughing; and B-type for roughing to finishing operations.
Speed and feed rates can effectively be doubled with PrimeTurning. This is because the small entering angle and higher lead angle create thinner, wider chips that spread the load and heat away from the nose radius, resulting in increased cutting data and/or tool life. Furthermore, as cutting is performed in the direction moving away from the shoulder, there is no danger of chip jamming, a common and highly undesirable effect of conventional internal turning.
With CoroTurn Prime SL heads, customers can create a wide range of tool combinations from a small inventory of adapters and cutting heads. SL heads are available in 40 mm (1.575 inches) diameter and fit with solid steel bars and carbide bars as well as with Silent Tools damped boring bars for vibration-free internal machining.
In addition, Sandvik Coromant now offers the new -H3 geometry to eliminate any concerns about chip control, which can be challenging when machining low-carbon and high-strength steels. The -H3 geometry is available for B-type inserts in grades GC4325, GC1115 and H13A.
Contact Details
Related Glossary Terms
- boring
boring
Enlarging a hole that already has been drilled or cored. Generally, it is an operation of truing the previously drilled hole with a single-point, lathe-type tool. Boring is essentially internal turning, in that usually a single-point cutting tool forms the internal shape. Some tools are available with two cutting edges to balance cutting forces.
- chuck
chuck
Workholding device that affixes to a mill, lathe or drill-press spindle. It holds a tool or workpiece by one end, allowing it to be rotated. May also be fitted to the machine table to hold a workpiece. Two or more adjustable jaws actually hold the tool or part. May be actuated manually, pneumatically, hydraulically or electrically. See collet.
- feed
feed
Rate of change of position of the tool as a whole, relative to the workpiece while cutting.
- lead angle
lead angle
Angle between the side-cutting edge and the projected side of the tool shank or holder, which leads the cutting tool into the workpiece.
- profiling
profiling
Machining vertical edges of workpieces having irregular contours; normally performed with an endmill in a vertical spindle on a milling machine or with a profiler, following a pattern. See mill, milling machine.
- turning
turning
Workpiece is held in a chuck, mounted on a face plate or secured between centers and rotated while a cutting tool, normally a single-point tool, is fed into it along its periphery or across its end or face. Takes the form of straight turning (cutting along the periphery of the workpiece); taper turning (creating a taper); step turning (turning different-size diameters on the same work); chamfering (beveling an edge or shoulder); facing (cutting on an end); turning threads (usually external but can be internal); roughing (high-volume metal removal); and finishing (final light cuts). Performed on lathes, turning centers, chucking machines, automatic screw machines and similar machines.