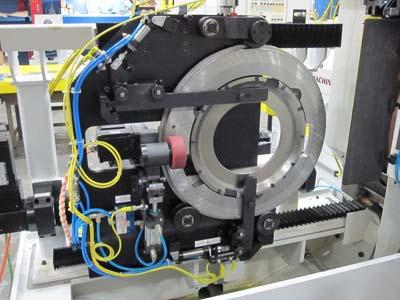
Hypro Inc., a value leader in machining, manufacturing, assembly of components and complex parts, has ordered a turnkey double disc grinding cell from C & B Machinery. C& B Machinery develops and builds grinding systems for manufacturers around the world; in this case, it will build a "Park & Grind" double disc grinding cell for Hypro, Waterford, Wis.
The grinding cell is designed to grind the faces of brake backing plates, up to 25" in diameter, for agricultural and off road equipment. This machine will be set up to grind ten different backing plate configurations and be flexible for any future program changes. The grinding cycle time for a finished part will be 180 seconds.
Double disc grinders remove an equal amount of material from both faces, simultaneously. This machine performs a "rotary plunge" grinding cycle. A single brake backing plate is introduced to the grinding wheels via a reciprocator, the carrier rotation will begin and the shuttle carriage will travel forward into the grind zone to a part's unique end position at which point the grinding wheels plunge grind simultaneously through axis interpolation. There are several advantages for grinding in this manner. The part is floating and rotating while being ground producing the best possible parallelism and flatness. Alternatively, parts like these can be introduced and ground using a magnetic chucking system, which can only grind one side of a part at a time. That process would add to grinding cycle time and add to the cost per piece thus reducing the return on investment.
This grinding cycle was developed by C & B Machinery engineers. In addition to the operating and investment cost savings, it allows 100 percent gauge feedback on every component ground. Size control is tightened, resulting in higher statistical capability.
Contact Details
Related Glossary Terms
- backing
backing
1. Flexible portion of a bandsaw blade. 2. Support material behind the cutting edge of a tool. 3. Base material for coated abrasives.
- disc grinding
disc grinding
Operation in which the workpiece is placed against the side of a wheel rather than the wheel’s periphery. See grinding.
- grinding
grinding
Machining operation in which material is removed from the workpiece by a powered abrasive wheel, stone, belt, paste, sheet, compound, slurry, etc. Takes various forms: surface grinding (creates flat and/or squared surfaces); cylindrical grinding (for external cylindrical and tapered shapes, fillets, undercuts, etc.); centerless grinding; chamfering; thread and form grinding; tool and cutter grinding; offhand grinding; lapping and polishing (grinding with extremely fine grits to create ultrasmooth surfaces); honing; and disc grinding.
- interpolation
interpolation
Process of generating a sufficient number of positioning commands for the servomotors driving the machine tool so the path of the tool closely approximates the ideal path. See CNC, computer numerical control; NC, numerical control.