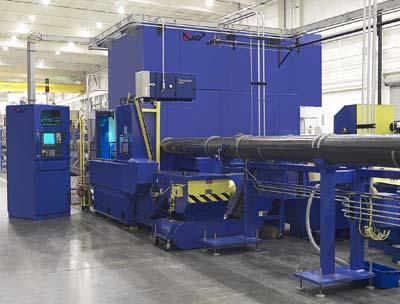
MAG's E Mill is a machine for economical machining of long, small cross-section parts used in aerospace, construction, shipbuilding and wind power. It is ideal for titanium, aluminum and composite work on stringers, spars, beams and similar parts. The E Mill performs contour machining, routing, drilling and tapping to produce finished, complex, 3D-geometry parts up to 12 m (39.4 ft) long in a single setup, reducing processing costs compared to vertical-platform machines. The innovative, economical design combines a production-proven 500mm 3-axis horizontal machining center (HMC) with headstock and tailstock adapted from horizontal lathes to provide fourth and fifth axes of motion. The part manipulation system allows A-axis programmable rotation and 360 degrees infinite positioning, while supplying V-axis linear travel for pull-through part feed. Work stock is loaded and unloaded from infeed and outfeed tubes. The E Mill can be ordered with a choice of a 16,000 or 24,000 rpm HSK63A spindle. Supporting single setup processing, a drum-style automatic tool changer accommodates 12 tools up to 8 kg (17.6 lb) in weight, 200mm (7.9 in) long, and 125mm (4.9 in) diameter. The E Mill comes standard with full enclosure guarding, vacuum filtration and mist/dust extraction for CE and OSHA compliance, especially important for machining composite materials. A pressurized way system protects against wear from abrasive composite dust. The headstock/tailstock system features through-hole chucks with powered jaws, allowing the work stock to be advanced incrementally through the jaws. The live headstock travels on V-axis linear slides, letting it move next to the stationary tailstock, lock on the workpiece, then slide back, pulling the work stock along. The system provides 1089mm (42.9 in) of travel for incremental part indexing. The fully programmable feed system can accommodate work stock from 300mm (12 in) to 12 m (39.4 ft) in length and up to 304.8mm (12 in) square in cross section. The headstock moves on parallel guideways 775mm (30 in) apart, while the fixed tailstock offers a similar broad base. This gives excellent stability for coordinated A-axis part rotation. Made from a tough industrial plastic, the infeed and out-feed tubes are clamshell designs. The in-feed opens from the top for loading work stock, with the outfeed bottom opening for ease of part removal. The tubes are seamless extrusions to prevent abrasion and delamination of composite materials, while the enclosed design provides additional containment of cutting fluids, part chips and dust. The E Mill machine design can be adapted to larger machining centers with more powerful spindles for processing of harder materials. Besides cost savings over machining platforms with 12 m (39.4 ft) travel or more, the compact E Mill design saves valuable plant floor space, avoids fixture costs, and enables faster set-up for reduced WIP.
Contact Details
Related Glossary Terms
- abrasive
abrasive
Substance used for grinding, honing, lapping, superfinishing and polishing. Examples include garnet, emery, corundum, silicon carbide, cubic boron nitride and diamond in various grit sizes.
- centers
centers
Cone-shaped pins that support a workpiece by one or two ends during machining. The centers fit into holes drilled in the workpiece ends. Centers that turn with the workpiece are called “live” centers; those that do not are called “dead” centers.
- feed
feed
Rate of change of position of the tool as a whole, relative to the workpiece while cutting.
- fixture
fixture
Device, often made in-house, that holds a specific workpiece. See jig; modular fixturing.
- machining center
machining center
CNC machine tool capable of drilling, reaming, tapping, milling and boring. Normally comes with an automatic toolchanger. See automatic toolchanger.
- milling machine ( mill)
milling machine ( mill)
Runs endmills and arbor-mounted milling cutters. Features include a head with a spindle that drives the cutters; a column, knee and table that provide motion in the three Cartesian axes; and a base that supports the components and houses the cutting-fluid pump and reservoir. The work is mounted on the table and fed into the rotating cutter or endmill to accomplish the milling steps; vertical milling machines also feed endmills into the work by means of a spindle-mounted quill. Models range from small manual machines to big bed-type and duplex mills. All take one of three basic forms: vertical, horizontal or convertible horizontal/vertical. Vertical machines may be knee-type (the table is mounted on a knee that can be elevated) or bed-type (the table is securely supported and only moves horizontally). In general, horizontal machines are bigger and more powerful, while vertical machines are lighter but more versatile and easier to set up and operate.
- parallel
parallel
Strip or block of precision-ground stock used to elevate a workpiece, while keeping it parallel to the worktable, to prevent cutter/table contact.
- tapping
tapping
Machining operation in which a tap, with teeth on its periphery, cuts internal threads in a predrilled hole having a smaller diameter than the tap diameter. Threads are formed by a combined rotary and axial-relative motion between tap and workpiece. See tap.
- through-hole
through-hole
Hole or cavity cut in a solid shape that connects with other holes or extends all the way through the workpiece.