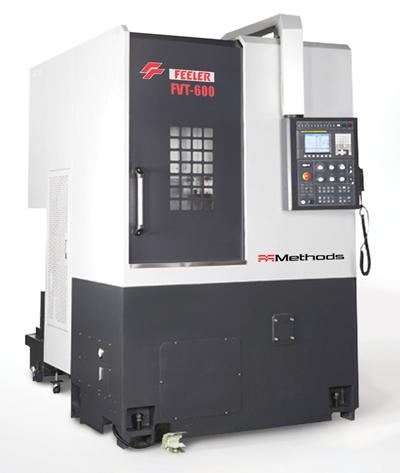
Methods Machine Tools Inc. has introduced the new High Performance FEELER FVT-600 Vertical Turning Lathe, ideal for machining large, heavy, challenging parts including those used in aerospace and power generation industries. To easily automate processes for high-volume production applications, the FEELER FVT-600 is available in left-side and right-side versions, allowing automation to be strategically stationed between the lathes.
"Increasingly, manufacturers are relying on vertical turning lathes to accommodate their larger and heavier parts," said Mr. Dale Hedberg, FEELER Product Manager, Methods Machine Tools Inc. "We are pleased to introduce the FEELER FVT-600 which is equipped with heavy-duty roller type linear guideways, resulting in high rigidity when making heavy cuts."
To minimize thermal deformation and vibration, and increase positioning accuracy, the FVT-600 features rugged construction and precision ballscrews that are directly coupled with highly responsive AC servo motors. The new FEELER vertical turning lathe offers a high-precision and high-rigidity spindle which is supported by two double-row cylindrical roller bearings and duplex angular thrust bearings.
This enables the lathe to endure heavy cutting in both radial and axial directions, resulting in high accuracy during long cutting cycles. The FVT-600 design permits coolant to flush chips to an extra wide conveyer where the chips are immediately evacuated.
The FEELER FVT-600 features a 12 position turret and offers an X-Axis travel of 12" (305mm) and a 25.6" (650mm) Z-Axis travel. Spindle speeds range from 50 to 2,000 RPM on a standard chuck size of 15" (381mm) and optional chuck sizes including 18" (457.2mm), 21" (533.4mm) or 24" (609.6mm), providing a high metal removal rate of 24 m/min. The new FEELER lathe offers a maximum turning diameter of 23.6" (600mm) and a maximum turning length of 25.6" (650mm). Maximum workpiece weight is 2,205 lbs (1,000 kg).
A reliable, easy-to-use FANUC 0i-TD control is standard and available in a swiveling control box for ergonomics and convenience. The FEELER FVT-600 offers a compact footprint at 134" length x 71" width (3,400mm length x 1,800mm width) and weighs 19,842 lbs (9,000 kg).
Contact Details
Related Glossary Terms
- chuck
chuck
Workholding device that affixes to a mill, lathe or drill-press spindle. It holds a tool or workpiece by one end, allowing it to be rotated. May also be fitted to the machine table to hold a workpiece. Two or more adjustable jaws actually hold the tool or part. May be actuated manually, pneumatically, hydraulically or electrically. See collet.
- coolant
coolant
Fluid that reduces temperature buildup at the tool/workpiece interface during machining. Normally takes the form of a liquid such as soluble or chemical mixtures (semisynthetic, synthetic) but can be pressurized air or other gas. Because of water’s ability to absorb great quantities of heat, it is widely used as a coolant and vehicle for various cutting compounds, with the water-to-compound ratio varying with the machining task. See cutting fluid; semisynthetic cutting fluid; soluble-oil cutting fluid; synthetic cutting fluid.
- lathe
lathe
Turning machine capable of sawing, milling, grinding, gear-cutting, drilling, reaming, boring, threading, facing, chamfering, grooving, knurling, spinning, parting, necking, taper-cutting, and cam- and eccentric-cutting, as well as step- and straight-turning. Comes in a variety of forms, ranging from manual to semiautomatic to fully automatic, with major types being engine lathes, turning and contouring lathes, turret lathes and numerical-control lathes. The engine lathe consists of a headstock and spindle, tailstock, bed, carriage (complete with apron) and cross slides. Features include gear- (speed) and feed-selector levers, toolpost, compound rest, lead screw and reversing lead screw, threading dial and rapid-traverse lever. Special lathe types include through-the-spindle, camshaft and crankshaft, brake drum and rotor, spinning and gun-barrel machines. Toolroom and bench lathes are used for precision work; the former for tool-and-die work and similar tasks, the latter for small workpieces (instruments, watches), normally without a power feed. Models are typically designated according to their “swing,” or the largest-diameter workpiece that can be rotated; bed length, or the distance between centers; and horsepower generated. See turning machine.
- turning
turning
Workpiece is held in a chuck, mounted on a face plate or secured between centers and rotated while a cutting tool, normally a single-point tool, is fed into it along its periphery or across its end or face. Takes the form of straight turning (cutting along the periphery of the workpiece); taper turning (creating a taper); step turning (turning different-size diameters on the same work); chamfering (beveling an edge or shoulder); facing (cutting on an end); turning threads (usually external but can be internal); roughing (high-volume metal removal); and finishing (final light cuts). Performed on lathes, turning centers, chucking machines, automatic screw machines and similar machines.