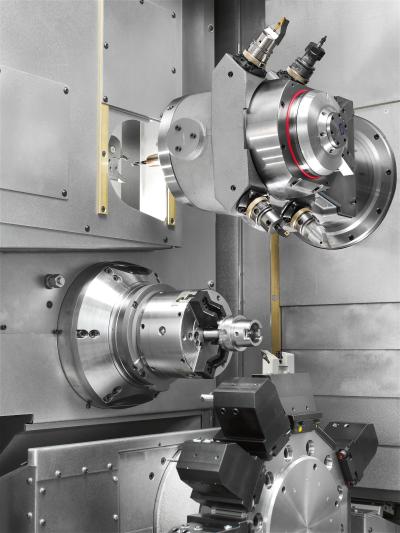
The INDEX G220 turn-mill center includes a motorized 5-axis 18,000-rpm milling spindle and a tool turret with a Y-axis, providing maximum machining flexibility for producing complex parts in a single setup from bar stock up to 90 mm in diameter or via a maximum chuck diameter of 210 mm. The distance between spindles is 1,280 mm, and the maximum turning length is 1,000 mm. The high-accuracy, done-in-one capabilities of the machine benefit users in the precision parts industries, including automotive, aerospace and mechanical engineering.
The G220’s fluid-cooled, identical main and counter spindles provide power of 31.5/32 kW (100%/40%), a torque of 125/ 170 Nm and a maximum speed of 5,000 rpm. The fluid-cooled, five-axis motorized milling spindle is available in both HSK-T40 and HSK-T63 configurations. The HSK-T40 version offers power of 11 kW, torque of 19/30 Nm and speed of up to 18000 rpm, while the HSK-T63 version offers power of 17 kW, torque of 62/90 Nm and speed of up to 12,000 rpm. Both milling spindle options feature hydrostatic bearings in the Y and B axes, and a stable circular guide further ensures excellent rigidity and damping. The Y axis features a +/-80 mm stroke, while the B axis is driven directly by a torque motor and has a swivel range of -50/+230 degrees. With a large travel distance in the X direction, machining at up to 30 mm below the turning center height is possible.
The motorized milling spindle operates using a one-row tool chain magazine, which features space for 70 tools for the HSK-T40 configuration or 50 tools for HSK-T63. An optional double-row tool magazine enables setup during machining and accommodates twice as many tools as the standard solution.
A tool turret is located in the lower part of the machine and can accommodate VDI 25 and VDI 30 tool mountings in 18 or 12 stations, respectively. All stations can be equipped with individually driven tools with power of 6 kW, torque of 18 Nm and a maximum speed of 7,200 rpm.
The compact machine features a programmable gantry-type removal unit for finished workpieces. It can unload remnants from the main spindle and finished parts from the counter spindle. The G220 offers a generous work area, providing operators easy access to the main and counter spindles, the turret and the motorized milling spindle, as well as the operating panel.
The G220 offers extremely high user friendliness and process reliability with the latest generation of the INDEX C200 sl controller. Based on the Siemens Sinumerik 840D sl (solution line), the G220’s control features an 18-inch touchscreen and incorporates the INDEX iXpanel operating system that expands operator support. As part of the iXpanel platform, the control includes an i4.0 button that toggles the screen between a traditional operating strip and activity-oriented display.
Additionally, the operating panel can do more than just operate the machine, as it includes a second input which can be used for INDEX’s optional Virtual Machine (VM) program simulation. By pressing a button, the operator can instantly switch to the VM environment and make use of simulation, irrespective of current machine operations.
Contact Details
Related Glossary Terms
- chuck
chuck
Workholding device that affixes to a mill, lathe or drill-press spindle. It holds a tool or workpiece by one end, allowing it to be rotated. May also be fitted to the machine table to hold a workpiece. Two or more adjustable jaws actually hold the tool or part. May be actuated manually, pneumatically, hydraulically or electrically. See collet.
- gang cutting ( milling)
gang cutting ( milling)
Machining with several cutters mounted on a single arbor, generally for simultaneous cutting.
- milling
milling
Machining operation in which metal or other material is removed by applying power to a rotating cutter. In vertical milling, the cutting tool is mounted vertically on the spindle. In horizontal milling, the cutting tool is mounted horizontally, either directly on the spindle or on an arbor. Horizontal milling is further broken down into conventional milling, where the cutter rotates opposite the direction of feed, or “up” into the workpiece; and climb milling, where the cutter rotates in the direction of feed, or “down” into the workpiece. Milling operations include plane or surface milling, endmilling, facemilling, angle milling, form milling and profiling.
- turning
turning
Workpiece is held in a chuck, mounted on a face plate or secured between centers and rotated while a cutting tool, normally a single-point tool, is fed into it along its periphery or across its end or face. Takes the form of straight turning (cutting along the periphery of the workpiece); taper turning (creating a taper); step turning (turning different-size diameters on the same work); chamfering (beveling an edge or shoulder); facing (cutting on an end); turning threads (usually external but can be internal); roughing (high-volume metal removal); and finishing (final light cuts). Performed on lathes, turning centers, chucking machines, automatic screw machines and similar machines.