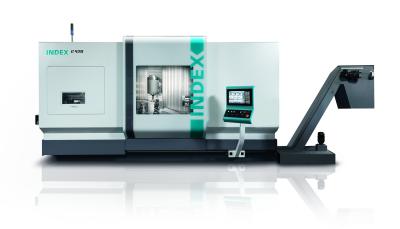
INDEX has announced the launch of its new G420 turn/mill center. The machine features identical 3,500-rpm twin spindles with 315 mm (400 mm optional) chucks and a robust 5-axis milling spindle that provides up to 12,000 rpm with an HSK-T63 interface or 18,000 rpm with a Capto C6 interface. The machine’s high inherent stability and dynamic response make it an exceptional choice for working with difficult-to-machine materials, providing significant value to aerospace manufacturers looking to complete large, complex parts in a single setup.
The G420’s main and counter spindles each accommodate bar stock of up to 102 mm in diameter and can chuck parts up to 315 mm in diameter (Ø400 mm optional). The large work area provides space for parts up to a maximum length of 1,600 mm and incorporates an ergonomic design to optimize operator accessibility. Additionally, an optional workpiece handling system can be incorporated for loading, unloading and transferring parts of up to 20 kg and 120 mm in diameter.
A powerful milling spindle offers 26 kW, 150 Nm and 12,000 rpm with an HSK-T63 interface or 27.5 kW, 100 Nm and 18,000 for the Capto C6 option. Optimized Y/B quill kinematics allow for highly productive simultaneous 5-axis milling operations to tackle complex geometries.
Designed as a modular system, the G420 can accommodate up to three tool carriers in its workspace, each equipped with a Y-axis. Turret steady rests are available to ensure maximum stability when machining long or shaft-shaped parts.
Ergonomics and flexibility were major considerations when designing the G420. All relevant components are easily accessible to operating and maintenance personnel. A chip conveyor can be mounted to either side of the machine, allowing customers to make optimum use of available floor space. Furthermore, automation solutions, including conveyor belts and robot handling units, can easily be integrated to provide additional enhancements to productivity.
Contact Details
Related Glossary Terms
- chuck
chuck
Workholding device that affixes to a mill, lathe or drill-press spindle. It holds a tool or workpiece by one end, allowing it to be rotated. May also be fitted to the machine table to hold a workpiece. Two or more adjustable jaws actually hold the tool or part. May be actuated manually, pneumatically, hydraulically or electrically. See collet.
- gang cutting ( milling)
gang cutting ( milling)
Machining with several cutters mounted on a single arbor, generally for simultaneous cutting.
- milling
milling
Machining operation in which metal or other material is removed by applying power to a rotating cutter. In vertical milling, the cutting tool is mounted vertically on the spindle. In horizontal milling, the cutting tool is mounted horizontally, either directly on the spindle or on an arbor. Horizontal milling is further broken down into conventional milling, where the cutter rotates opposite the direction of feed, or “up” into the workpiece; and climb milling, where the cutter rotates in the direction of feed, or “down” into the workpiece. Milling operations include plane or surface milling, endmilling, facemilling, angle milling, form milling and profiling.