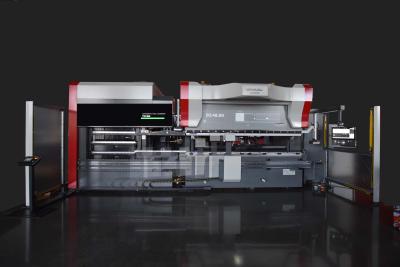
MC Machinery Systems introduces its new high-capacity automatic toolchanger (ATC) for its BH series of dual-drive press brakes. The ATC increases production levels and utilization rates while reducing setup time, especially in high-mix, low-volume environments.
The ATC allows for fully automated tool setup and removal, freeing up the operator to perform other tasks. Its available 107.3' x 170.6' storage capacity allows for ample tooling variation, ranging from high-runner V-dies to specialized hemming or offset tools. Up to 2" V-die openings and 19.7" lengths can be placed with the single, large-capacity tool manipulator with the added functionality of pick and place for small tool sections for setups that do not require the full setup to be removed. The manipulator is also equipped with a tool and bed cleaner that runs automatically during tool changes.
The ATC is engineered for operators of all experience levels. Programs can be created offline using DiamondBend software, at the control, or imported from other MOS controlled press brakes. Further support for operators is available with MC Machinery’s VIDERE operator support system for real-time bending information, sequences and automatic tool changes.
“More companies are looking at adding tool changers to their forming departments,” stated David Bray, product manager, press brakes. “This trend has gained momentum due to a perfect storm of industry and market factors, such as updating their laser processing equipment or finding qualified people to staff their forming departments. Metalworking companies are seeking ways to add efficiency to their blanking departments. The BH dual-drive ATC offers the largest storage with the most flexibility, it is the conclusive solution for customers looking for improved production and increased efficiency.”
Machines equipped with the ATC are not limited to the tools in the changer’s storage. The machine can be used as a stand-alone press brake or automated system, allowing for the flexibility for one-off jobs.
Contact Details
Related Glossary Terms
- automatic toolchanger
automatic toolchanger
Mechanism typically included in a machining center that, on the appropriate command, removes one cutting tool from the spindle nose and replaces it with another. The changer restores the used tool to the magazine and selects and withdraws the next desired tool from the storage magazine. The changer is controlled by a set of prerecorded/predetermined instructions associated with the part(s) to be produced.
- manipulator
manipulator
Arm or basic object-transferring device. Hands or gripping devices vary according to application, as do arm design and number of joints (axes or degrees of freedom). See degrees of freedom; effectuating device.
- metalworking
metalworking
Any manufacturing process in which metal is processed or machined such that the workpiece is given a new shape. Broadly defined, the term includes processes such as design and layout, heat-treating, material handling and inspection.
- toolchanger
toolchanger
Carriage or drum attached to a machining center that holds tools until needed; when a tool is needed, the toolchanger inserts the tool into the machine spindle. See automatic toolchanger.