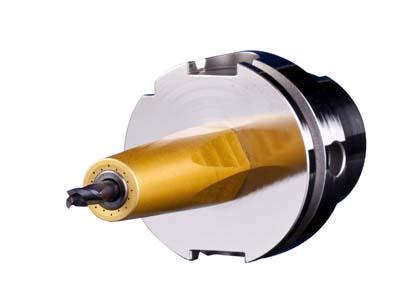
New JetSleeve from Bilz Tool Co. Inc. is for enhancing milling tasks by providing more performance due to precise coolant supply. According to the company, the coolant supply impresses with its considerable economic and ecological advantages for customers in the mold and die industry, the automotive industry, and medical and dental technology.
The heart of the new JetSleeve is shrink chuck with three compressed air holes and an aluminum sleeve. With the help of 16 holes at different angles on the front of the sleeve, the pressurized medium is forced at high speed and without separation to the working areas where the chips are blown away as soon as they are formed. This means no more milling cutter breakage. The result is a direct influence on considerably improved tool life and less annual tool costs. The most tangible cost advantages, however, are achieved by a significantly improved surface quality of the work pieces, because vibrations are reduced during the operation due to the hydraulic design of the JetSleeve holder.
Reworking such as finishing, polishing, and finish-milling are no longer necessary. JetSleeve can be used for milling cutters from diameters of 3mm up to 20mm and for all taper sizes HSK and SK, Special solutions and lengths are always possible. Not only does this cover the biggest part of all milling tasks, but in contrast to former solutions. JetSleeve can also be used on all machines with internal coolant flow. This means a one-time investment cost which pays off immediately through higher production capacity. Process security is guaranteed due to the automatic operation, as there is no chip accumulation and programming is not interrupted.
The considerably reduced raw material consumption has a great effect on the production of milling tools. Furthermore, much less air pressure and power for compressors is needed and there is less oil pollution.
Contact Details
Related Glossary Terms
- chuck
chuck
Workholding device that affixes to a mill, lathe or drill-press spindle. It holds a tool or workpiece by one end, allowing it to be rotated. May also be fitted to the machine table to hold a workpiece. Two or more adjustable jaws actually hold the tool or part. May be actuated manually, pneumatically, hydraulically or electrically. See collet.
- coolant
coolant
Fluid that reduces temperature buildup at the tool/workpiece interface during machining. Normally takes the form of a liquid such as soluble or chemical mixtures (semisynthetic, synthetic) but can be pressurized air or other gas. Because of water’s ability to absorb great quantities of heat, it is widely used as a coolant and vehicle for various cutting compounds, with the water-to-compound ratio varying with the machining task. See cutting fluid; semisynthetic cutting fluid; soluble-oil cutting fluid; synthetic cutting fluid.
- gang cutting ( milling)
gang cutting ( milling)
Machining with several cutters mounted on a single arbor, generally for simultaneous cutting.
- milling
milling
Machining operation in which metal or other material is removed by applying power to a rotating cutter. In vertical milling, the cutting tool is mounted vertically on the spindle. In horizontal milling, the cutting tool is mounted horizontally, either directly on the spindle or on an arbor. Horizontal milling is further broken down into conventional milling, where the cutter rotates opposite the direction of feed, or “up” into the workpiece; and climb milling, where the cutter rotates in the direction of feed, or “down” into the workpiece. Milling operations include plane or surface milling, endmilling, facemilling, angle milling, form milling and profiling.
- milling cutter
milling cutter
Loosely, any milling tool. Horizontal cutters take the form of plain milling cutters, plain spiral-tooth cutters, helical cutters, side-milling cutters, staggered-tooth side-milling cutters, facemilling cutters, angular cutters, double-angle cutters, convex and concave form-milling cutters, straddle-sprocket cutters, spur-gear cutters, corner-rounding cutters and slitting saws. Vertical cutters use shank-mounted cutting tools, including endmills, T-slot cutters, Woodruff keyseat cutters and dovetail cutters; these may also be used on horizontal mills. See milling.
- polishing
polishing
Abrasive process that improves surface finish and blends contours. Abrasive particles attached to a flexible backing abrade the workpiece.