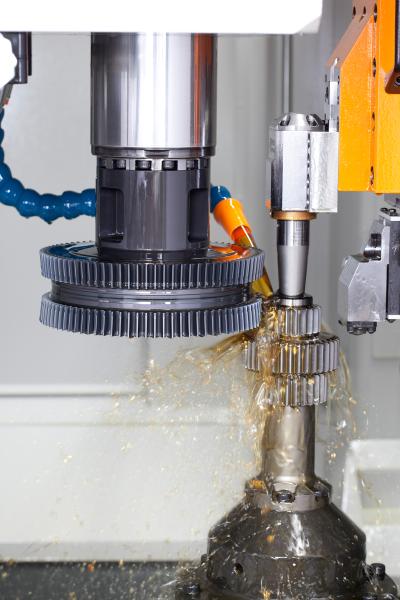
Liebherr-Verzahntechnik GmbH has expanded its machine portfolio for small workpieces with the small-footprint (Platform 1) LS 180 F shaping machine equipped with an electronically operated, movable cutter head slide. The machine can shape smaller gears in different axial positions with only short setup times. The machine is likely to be of interest for job shops, especially with aerospace work. The LS 180 F is also highly productive, capable of up to 1,500 double strokes per minute, processing workpieces up to 180 mm diameter, maximum module 5 mm.
Shaping continues to be the gear manufacturing process of choice for gears to be part of transmissions with minimum available space, for example, cluster gears with limited cutter overrun, which can be machined in one clamping in the new Liebherr machine, avoiding additional setups.
Previously, only larger machines could accommodate such flexible applications; smaller shaping machines did not feature the necessary movable cutter head slide, according to the company. The new LS 180 F now enables Liebherr to provide the right size of machine with a lot of features for small workpieces, too.
The new cutter head design also enables workpieces with internal and external gear teeth to be machined in the same clamping operation. To accomplish this, the machine is equipped with a twin-track cam as standard. The LS 180 F continues to be available with a mechanical helical guide. The new version is also compatible with older versions, meaning that existing helical guides and removal cams can be used with the LS 180 F.
“One actual application is, for example, a component used to adjust aircraft landing flaps,” said Dr. Andreas Mehr from the grinding and shaping technology development and application team at Liebherr-Verzahntechnik. “Every component features three gears that have to be positioned quite accurately to each other. That is why it is absolutely necessary to machine the entire gear tooth machining procedure in one clamping.” But there are also potential customers for the LS 180 F in pump manufacturing as well as in the motorbike and tractor industry. “This machine is extremely versatile,” Dr. Mehr emphasized. “Given its high stroke rate of 1,500 double strokes per minute, this machine can produce small quantities very cost-effectively.”
The LS 180 F enables Liebherr to combine the small footprint of the Platform 1 with applications that were previously only feasible using larger machines. The LS 180 (without vertical cutter head slide) will be redesigned and an LS 180 E (with electronic helical guide and movable cutter head slide) will be designed from scratch in 2017.
“Ultimately we will then be able to offer the same maximum flexibility in the smallest machine class as we have only been able to do with larger machines to date,” said Dr. Hansjörg Geiser, head of gear cutting machinery development and design engineering at Liebherr-Verzahntechnik.
Technical Data
Max. normal module 5 mm
Max. workpiece size 180 mm
Infinitely variable stroke rate as standard 1,500 DS/min
Stroke length (with SK 1.70) max. 70 mm
Centre distance, cutter spindle/machine table -30 mm ... 285 mm
Axis angle, cutter spindle/machine table +/-0.5°
Column swivel axis -1°...+12°
Stroke position range, cutter head slide 275 mm
Radial feed axis, column carriage 5,000 mm/min
Total weight 13,000 kg
Footprint (LxWxH) 5,000 x 3,480 x 2,950 mm
Related Glossary Terms
- computer-aided manufacturing ( CAM)
computer-aided manufacturing ( CAM)
Use of computers to control machining and manufacturing processes.
- feed
feed
Rate of change of position of the tool as a whole, relative to the workpiece while cutting.
- grinding
grinding
Machining operation in which material is removed from the workpiece by a powered abrasive wheel, stone, belt, paste, sheet, compound, slurry, etc. Takes various forms: surface grinding (creates flat and/or squared surfaces); cylindrical grinding (for external cylindrical and tapered shapes, fillets, undercuts, etc.); centerless grinding; chamfering; thread and form grinding; tool and cutter grinding; offhand grinding; lapping and polishing (grinding with extremely fine grits to create ultrasmooth surfaces); honing; and disc grinding.
- shaping
shaping
Using a shaper primarily to produce flat surfaces in horizontal, vertical or angular planes. It can also include the machining of curved surfaces, helixes, serrations and special work involving odd and irregular shapes. Often used for prototype or short-run manufacturing to eliminate the need for expensive special tooling or processes.