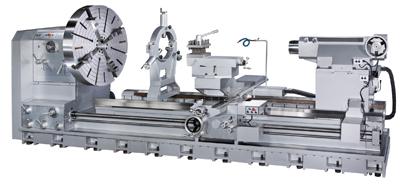
Sharp Industries Inc. is offering the large swing, big bore manual lathe that is ideal for large oil pipe work, heavy shaft turning jobs and large diameter steel rods. The M series lathes are available with swings of 40", 50", 60", 70", and 80", distance between centers from 60" to 315" and spindle bores sizes of 6", 9" and 12".
The Sharp M series machine base is a one piece structure, made from high grade Meehanite casting to maintain durability and maximum stability under heavy cutting conditions. The 32" wide bedways are induction hardened and ground with separate bedways at the front of the bed to support the heavy carriage and apron. This allows better dispersion of cutting force from the carriage. The apron is equipped with a 6-way control of the carriage and cross slide movements. The operator can run the machine next by the apron with great ease.
The cross slide ways are coated with Turcite-B for better oil retention and wear resistance for long time usage. The headstock is designed with 3 point bearing support of the spindle, combined with the large spindle motor, up to 50 HP; it delivers full power for heavy duty machining works.
The rear chuck adapter is available for double chuck mounting. The gears and shafts are made from hardened and ground alloy steel, the spindle is made from forged, chrome alloy material. The fully enclosed gear box allows easy change of inch, metric, MP and DP threads without changing any gears. Coarse inch threads are available up to ¼ TPI. The heavy duty tailstock is available with motorized movement on the quill and the base for ease of operation.
Contact Details
Related Glossary Terms
- centers
centers
Cone-shaped pins that support a workpiece by one or two ends during machining. The centers fit into holes drilled in the workpiece ends. Centers that turn with the workpiece are called “live” centers; those that do not are called “dead” centers.
- chuck
chuck
Workholding device that affixes to a mill, lathe or drill-press spindle. It holds a tool or workpiece by one end, allowing it to be rotated. May also be fitted to the machine table to hold a workpiece. Two or more adjustable jaws actually hold the tool or part. May be actuated manually, pneumatically, hydraulically or electrically. See collet.
- cutting force
cutting force
Engagement of a tool’s cutting edge with a workpiece generates a cutting force. Such a cutting force combines tangential, feed and radial forces, which can be measured by a dynamometer. Of the three cutting force components, tangential force is the greatest. Tangential force generates torque and accounts for more than 95 percent of the machining power. See dynamometer.
- lathe
lathe
Turning machine capable of sawing, milling, grinding, gear-cutting, drilling, reaming, boring, threading, facing, chamfering, grooving, knurling, spinning, parting, necking, taper-cutting, and cam- and eccentric-cutting, as well as step- and straight-turning. Comes in a variety of forms, ranging from manual to semiautomatic to fully automatic, with major types being engine lathes, turning and contouring lathes, turret lathes and numerical-control lathes. The engine lathe consists of a headstock and spindle, tailstock, bed, carriage (complete with apron) and cross slides. Features include gear- (speed) and feed-selector levers, toolpost, compound rest, lead screw and reversing lead screw, threading dial and rapid-traverse lever. Special lathe types include through-the-spindle, camshaft and crankshaft, brake drum and rotor, spinning and gun-barrel machines. Toolroom and bench lathes are used for precision work; the former for tool-and-die work and similar tasks, the latter for small workpieces (instruments, watches), normally without a power feed. Models are typically designated according to their “swing,” or the largest-diameter workpiece that can be rotated; bed length, or the distance between centers; and horsepower generated. See turning machine.
- turning
turning
Workpiece is held in a chuck, mounted on a face plate or secured between centers and rotated while a cutting tool, normally a single-point tool, is fed into it along its periphery or across its end or face. Takes the form of straight turning (cutting along the periphery of the workpiece); taper turning (creating a taper); step turning (turning different-size diameters on the same work); chamfering (beveling an edge or shoulder); facing (cutting on an end); turning threads (usually external but can be internal); roughing (high-volume metal removal); and finishing (final light cuts). Performed on lathes, turning centers, chucking machines, automatic screw machines and similar machines.
- wear resistance
wear resistance
Ability of the tool to withstand stresses that cause it to wear during cutting; an attribute linked to alloy composition, base material, thermal conditions, type of tooling and operation and other variables.