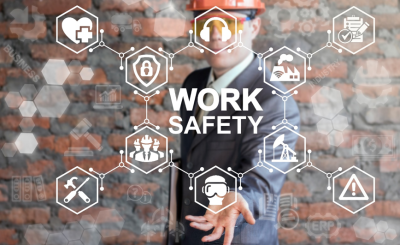
Bihler 4Slide-NC Technology advances the goal of an injury-free, OSHA-complaint, manufacturing facility. Job safety is among the most critical factors in protecting the most valuable asset of a manufacturing company - its employees. A safe working environment promotes a positive and productive culture, all the while enhancing company morale and building employee retention. Studies of manufacturing safety have shown that a safe work environment can boost productivity levels by as much as 83%.
The typical mechanical four-slide machine is composed largely of rotating shafts, each of which are potentially dangerous, due to the possibility of clothing being grabbed, or unintended pinching or crushing contact with skin, arms or hands, any of which of these occurrences can lead to severe injuries.
The Bihler 4Slide-NC servo automation technology eliminates the need for rotating shafts, and by so doing, greatly reduces the risk of hazardous injuries. The Bihler 4Slide-NC machine also has a safety enclosure, with door interlock switches, along with gate devices to safeguard the operator. Bihler 4Slide-NC is an OSHA-compliant equipment provider, and it maintains up-to-date inspections to ensure compliance with all applicable OSHA safety requirements.
With traditional four-slide machines, the recurring need for mechanical adjustments, and the accompanying repetitive use of hand tools, can result in musculoskeletal injuries. The programmable cam profile, with its instantaneous change, eliminates the need for a manual cam change. And, with its automated and enhanced capabilities, Bihler 4Slide-NC eliminates the constant need for ongoing process adjustment to facilitate the manufacturing process.
Proper training has been shown to be an invaluable means to reduce workplace injuries, and the Bihler 4Slide-NC system is therefore equipped with a video library to provide easily-accessible training material. Bihler 4Slide-NC is pleased to note that, as a result of the ergonomic design, and the easy-to-use features of the machine, there have been in the past four years, no equipment-related injuries whatsoever.
Depending upon the operating parameters under which they operate, depending upon whether or not they operate under air or liquid pressure, and depending upon the nature of the material handling, feeding and processing mechanisms, metal-forming machines are potentially a significant source of workplace injuries. Unfortunately, on an annual basis, six out of 100 metal fabrication workers report injuries that are related to equipment usage. According to the U.S. Department of Labor, each year, workers who operate and maintain machinery suffer approximately 18,000 injuries, in the form of amputations, lacerations, crushing injuries and abrasions, along with over 800 deaths.
Causes of injury:
- The primary cause of machine-related injuries is an ineffective guard - one that is either defective or missing.
- In the course of their daily work activities, metal fabrication workers are also at risk from health-related hazards and long-term injuries, such as repetitive strain injury, and occupational overuse syndrome.
- The improper use of manufacturing equipment can lead to musculoskeletal injuries, including carpal tunnel syndrome and tendonitis.
The Occupational Safety and Health Administration’s (OSHA) reports that deficiencies in providing machine guarding (as required under OSHA Standard 1910.212) are among the top 10 most frequent violations, noting that there were 1,933 such violations in 2017. As can be anticipated, amputations are the most dangerous outcome resulting from a lack of machine guarding in a manufacturing facility. Aside from the human cost, the failure to implement proper machine guarding may result in OSHA levying fines that can range from in excess of $130,000 all the way up to $2.5 million, depending upon the severity of the injury and whether or not there has been a reoccurrence of the the underlying violation. In the past year alone, the fabricated metal product industry has been served with a total of 3,608 citations that cost the industry over $10 million in fines and penalties.
Contact Details
Related Glossary Terms
- computer-aided manufacturing ( CAM)
computer-aided manufacturing ( CAM)
Use of computers to control machining and manufacturing processes.