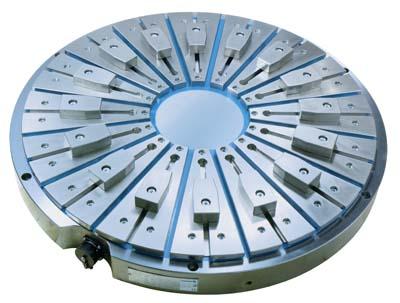
For exact machining of thin-walled rings on rotary tables, cylindrical grinding machines, and lathes, Schunk Inc. now offers a vast program of standardized magnetic chucks with radial pole pitch. MAGNOS radial pole plates work with electrically activated permanent magnets and are proven for hard and finish turning, as well as grinding and rough machining. The workpiece can be machined from three sides without a changeover and since the magnetic field is active up to the outer fringe areas, extremely large workpieces can now be clamped securely and deformation-free. Due to the two-dimensional acting holding force, vibrations are greatly reduced during machining. This prevents the cutting edges of the tools from damage and improves the surface quality of the workpiece. Depending on the individual application, three different sizes of standardized radial pole plates are offered. For grinding operations, an AlNiCo single magnet system with automatic demagnetization, for turning operations, an AlNiCo double magnet system with high holding forces. The third one is for demanding volume machining during rough turning, an extra strong AlNiCo neodymium magnet system.
Contact Details
Related Glossary Terms
- cylindrical grinding
cylindrical grinding
Grinding operation in which the workpiece is rotated around a fixed axis while the grinding wheel is fed into the outside surface in controlled relation to the axis of rotation. The workpiece is usually cylindrical, but it may be tapered or curvilinear in profile. See centerless grinding; grinding.
- grinding
grinding
Machining operation in which material is removed from the workpiece by a powered abrasive wheel, stone, belt, paste, sheet, compound, slurry, etc. Takes various forms: surface grinding (creates flat and/or squared surfaces); cylindrical grinding (for external cylindrical and tapered shapes, fillets, undercuts, etc.); centerless grinding; chamfering; thread and form grinding; tool and cutter grinding; offhand grinding; lapping and polishing (grinding with extremely fine grits to create ultrasmooth surfaces); honing; and disc grinding.
- pitch
pitch
1. On a saw blade, the number of teeth per inch. 2. In threading, the number of threads per inch.
- turning
turning
Workpiece is held in a chuck, mounted on a face plate or secured between centers and rotated while a cutting tool, normally a single-point tool, is fed into it along its periphery or across its end or face. Takes the form of straight turning (cutting along the periphery of the workpiece); taper turning (creating a taper); step turning (turning different-size diameters on the same work); chamfering (beveling an edge or shoulder); facing (cutting on an end); turning threads (usually external but can be internal); roughing (high-volume metal removal); and finishing (final light cuts). Performed on lathes, turning centers, chucking machines, automatic screw machines and similar machines.