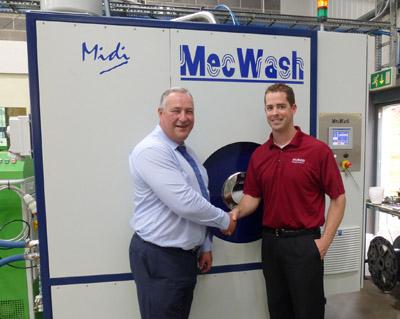
HUSCO International, a global leader in the development and manufacture of hydraulic and electrohydraulic controls, has invested in two additional MecWash component cleaning systems following the success of previous installations.
HUSCO commissioned its first MecWash Midi for use at the company's European headquarters in Runcorn, Cheshire, in 2000. Since then it has installed three units in the UK, as well as five in the US and one in China. The 11th machine will be delivered this month with the 12th scheduled for later this year.
The Midi aqueous wash machines clean hydraulic control valves used in off-highway applications, including agricultural machinery, materials handling and construction, to the exacting standards demanded by HUSCO's customers around the world.
HUSCO's Senior Manufacturing Engineer Eric Pollard, comments, "Our customers trust us to deliver precision engineered parts manufactured to the very highest specifications. HUSCO's global reputation is recognition of our unwavering commitment to quality and this applies to all aspects of our supply chain."
Achieving the highest standards of cleanliness possible is absolutely vital for parts destined to end up in hydraulic and pneumatic systems where even the smallest levels of contamination can have significant long-term effects.
Pollard continues: "Solid particle contamination can interfere with the lubrication process in hydraulic fluid systems, causing wear to the components can result in additional maintenance and repair costs, and a substantial decrease in the system's service life. Worn components can lead to parts seizing, higher fluid temperatures, leaks and reduced control. Contamination can also damage the system's fluid by accelerating oxidation, again resulting in inefficient operation. It is therefore vital that all of our parts are free from contamination before they reach the assembly line. This is the main reason why we continue to invest in MecWash machines, as they are renowned for achieving high cleanliness standards."
HUSCO initially chose the MecWash Midi after a number of trials at the company's dedicated laboratory to identify the best combination of wash features and detergent for its specific requirements.
MecWash Managing Director John Pattison, says, "The Midi is the ideal choice for cleaning components used in hydraulic and pneumatic systems. It has been specifically designed to process complex and intricate machined parts that require very high standards of cleanliness, surface finish and dryness, and can incorporate a range of functionality including ultrasonic, high flow washing, rinsing, dedicated jetting and vacuum drying. Most importantly of all, as HUSCO has confirmed, the Midi provides 24/7 reliability which is absolutely imperative in the demanding industries in which it is used."
HUSCO successfully operates manufacturing facilities and provides local support throughout Europe, India and China, as well as the US which is home to its global headquarters. It has developed a manufacturing blueprint that enables the company to replicate production operations across continents; robust supplier relationships are a key factor in the company's global success. HUSCO recognizes that "the best products and processes are only as good as the inputs which make them up" and proactively develops successful, long-term relationships with suppliers through its dedicated Supplier Development Team.
This way of thinking resulted in the HUSCO installations overseas, as Pattison explains, "A number of our customers with global manufacturing operations choose to replicate successful practices when they establish new facilities both here in the UK and overseas. This approach removes some of the risk and can speed up the whole process. "Experienced and market savvy companies like HUSCO, recognize the value of establishing and maintaining mutually beneficial relationships for the benefit of the whole supply chain, including their end-users."
As with the majority of the previous Midi installations, the two machines currently in production will both benefit from Aqua-Save waste water recycling and treatment systems to reduce the volumes of water used in the wash process.
Contact Details
Related Glossary Terms
- materials handling
materials handling
Methods, equipment and systems for conveying materials to various machines and processing areas and for transferring finished parts to assembly, packaging and shipping areas.