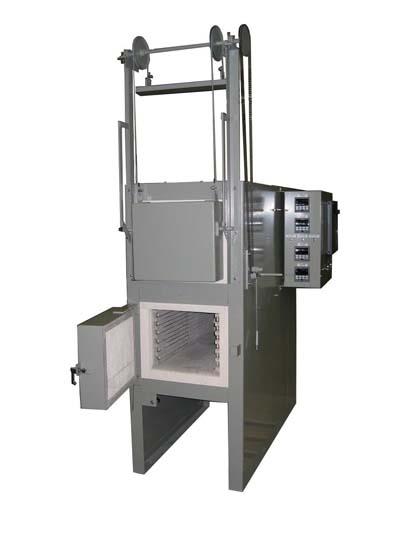
LMC Industries, a full service metal stamping and molding company in Arnold, Mo., has added a Lucifer Dual Chamber furnace to its cadre of equipment. Model HL82-H24 will be used for processing tool steels in their TS16949 and ISO9001certified facility.
According to Max Vogl, Tool Room Manager, LMC wanted a furnace for its tooling facility, which supports both their stamping and molding divisions "to retain the cost of sending out our heat treat" and "to improve the turnaround time of heat treating in emergency and weekend situations" Max says they chose Model HL82-H24 "because it gives us the versatility of heat treating a wide variety of tool steels which includes powder metals such as CPM. After searching the Web and discussion with companies we researched, Lucifer seemed to be the best fit for our company and came highly recommended from a tool shop and local steel supplier we do business with."
Built with 5" of multilayered firebrick and mineral wool block insulation for energy efficiency and low outside shell temperature, the 9"x12"x24" upper chamber heats to 2300°F. Easy-to-replace heating elements are mounted on side walls and door in removable panels with V grooves open to coils providing maximum radiation and faster heat response. The vertical lift counterweighted door is hand crank operated. A lower tempering chamber of the same dimensions, built with 4.5" of insulating firebrick and mineral wool block, heats to 1200°F. A 16 gauge stainless steel liner forms the work chamber, on board with a 1⁄6-hp motor recirculating alloy fan to direct the heated air in a horizontal flow pattern while keeping heating elements isolated from the workload. The lower chamber is complete with a horizontal swing door with 5" of insulation, a cam lock and safety micro switch.
Both chambers are controlled by Honeywell UDC 2500 microprocessor based digital time proportioning temperature controllers with a separate high limit controller on the upper chamber. Max plans to use the furnace to remove the white cast layer after Wire EDM processes by tempering punches and die sections which reduces chipping during the stamping process, and to incorporate in their Preventative Maintenance program the tempering of punches and die sections to relieve the stress build up by stamping, which can lead to punch breakage if not done.
Max adds "Lucifer has been great to work with and met their commitment on delivery. LMC is very satisfied that we chose Lucifer and would recommend this type of furnace to any company that is in the same type of business that we are""
Contact Details
Related Glossary Terms
- computer-aided manufacturing ( CAM)
computer-aided manufacturing ( CAM)
Use of computers to control machining and manufacturing processes.
- electrical-discharge machining ( EDM)
electrical-discharge machining ( EDM)
Process that vaporizes conductive materials by controlled application of pulsed electrical current that flows between a workpiece and electrode (tool) in a dielectric fluid. Permits machining shapes to tight accuracies without the internal stresses conventional machining often generates. Useful in diemaking.
- lapping compound( powder)
lapping compound( powder)
Light, abrasive material used for finishing a surface.
- payload ( workload)
payload ( workload)
Maximum load that the robot can handle safely.
- tempering
tempering
1. In heat-treatment, reheating hardened steel or hardened cast iron to a given temperature below the eutectoid temperature to decrease hardness and increase toughness. The process also is sometimes applied to normalized steel. 2. In nonferrous alloys and in some ferrous alloys (steels that cannot be hardened by heat-treatment), the hardness and strength produced by mechanical or thermal treatment, or both, and characterized by a certain structure, mechanical properties or reduction in area during cold working.
- tool steels
tool steels
Group of alloy steels which, after proper heat treatment, provide the combination of properties required for cutting tool and die applications. The American Iron and Steel Institute divides tool steels into six major categories: water hardening, shock resisting, cold work, hot work, special purpose and high speed.
- web
web
On a rotating tool, the portion of the tool body that joins the lands. Web is thicker at the shank end, relative to the point end, providing maximum torsional strength.
- wire EDM
wire EDM
Process similar to ram electrical-discharge machining except a small-diameter copper or brass wire is used as a traveling electrode. Usually used in conjunction with a CNC and only works when a part is to be cut completely through. A common analogy is wire electrical-discharge machining is like an ultraprecise, electrical, contour-sawing operation.