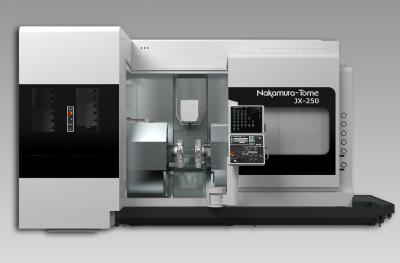
Methods Machine Tools, Inc., North America's foremost supplier of leading-edge precision machine tools and automation, has introduced the Nakamura-Tome JX-250 High Performance Multitasking Turning Center which offers the largest machining area envelope in its class for high precision milling and turning of complex parts, along with a unique twin lower turret configuration allowing ultimate flexibility of complex component manufacturing. The ATC-style Nakamura JX-250 features NT Smart Cube Tool Spindle, the shortest tool spindle on the market today. The 12,000 RPM tool spindle permits maximum part length on the left and right spindles, including when the horizontal tool spindle and lower turrets are in the cut.
To optimize part transfer, independent right spindle guideways on lower turrets minimize the distance between the spindles at 11.8” (300 mm). For highest processing flexibility, a single or twin lower turret design is offered with overlapping travels and Y-Axis box guideways are standard. The new multitasking machining center provides up to 168 tool stations.
"We are pleased to offer the highly precise and efficient Nakamura JX-250 mill/ turn solution for precision manufacturing in a broad range of industries, including aerospace, medical and automotive," said Mr. Sergio Tondato, Nakamura-Tome Product Manager at Methods Machine Tools, Inc. "The JX-250 is exceptionally productive ‒ allowing maximum part length and performing left and right simultaneous machining.”
The Nakamura JX-250 offers high accuracy and exceptional rigidity due to its horizontal bed design with a wide, low center of gravity and vertical column structure, weighing 55,000 lbs. NT Thermo Navigator AI technology controls thermal growth during machining and compensates for temperature changes.
The new multitasking turning center has a maximum turning diameter of 12.6" (320 mm) and a maximum turning length of 65" (1,650mm). The left and right spindles have 3" (80 mm) and 2.5" (65 mm) bar capacity, respectively. Tool spindle X,Y,Z travel is 25.4" x ± 4.9" x ± 32.5" (645 mm x ±125 mm x ±825 mm). The B-axis tool spindle positioning range is 240°
The JX-250 features a SmartX PC-based 19" high-resolution color touch screen, which works in conjunction with the Fanuc 31i-B5 control for a high degree of functionality. A 5-Axis Precision Milling software package ensures optimal 5-axis milling.
The JX-250 comes equipped with several smart features including the NT Work Navigator that can recognize the coordinates of machine parts with non-round shapes such as those in forgings and castings, without any additional costs involved. This feature eliminates the need for costly positioning fixtures and clamping devices. The Advanced NT Nurse System all-in-one software package is also included, providing convenient, easy-to-use support for the operation, programming and production on the JX-250. Critical functionality includes phase recognition (key for multitasking), direct chucking enabling transfer without positioning error, and precise synchronization of the left/ right-hand spindles. Additional functions include a load monitor for identifying tool wear/ breakage, tool life management and machine monitoring.
All Nakamura-Tome machines are equipped with a standard electronic detector safety feature that greatly reduces the impact and force of a machine collision. Should a crash occur, within 4 milliseconds after the crash, servo motor-feeding direction is reversed and the machine will stop in EMG mode.
Contact Details
Related Glossary Terms
- gang cutting ( milling)
gang cutting ( milling)
Machining with several cutters mounted on a single arbor, generally for simultaneous cutting.
- machining center
machining center
CNC machine tool capable of drilling, reaming, tapping, milling and boring. Normally comes with an automatic toolchanger. See automatic toolchanger.
- milling
milling
Machining operation in which metal or other material is removed by applying power to a rotating cutter. In vertical milling, the cutting tool is mounted vertically on the spindle. In horizontal milling, the cutting tool is mounted horizontally, either directly on the spindle or on an arbor. Horizontal milling is further broken down into conventional milling, where the cutter rotates opposite the direction of feed, or “up” into the workpiece; and climb milling, where the cutter rotates in the direction of feed, or “down” into the workpiece. Milling operations include plane or surface milling, endmilling, facemilling, angle milling, form milling and profiling.
- turning
turning
Workpiece is held in a chuck, mounted on a face plate or secured between centers and rotated while a cutting tool, normally a single-point tool, is fed into it along its periphery or across its end or face. Takes the form of straight turning (cutting along the periphery of the workpiece); taper turning (creating a taper); step turning (turning different-size diameters on the same work); chamfering (beveling an edge or shoulder); facing (cutting on an end); turning threads (usually external but can be internal); roughing (high-volume metal removal); and finishing (final light cuts). Performed on lathes, turning centers, chucking machines, automatic screw machines and similar machines.