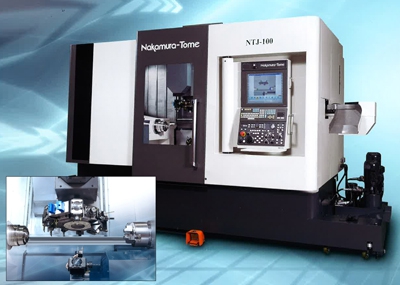
Methods Machine Tools Inc. has introduced the Nakamura-Tome NTJ-100 Multitasking Turn/Mill Center, which is well-suited for a wide range of production needs. Applications range from low to high volume lots of medical, aerospace, general job shop components and more.
The new Nakamura NTJ-100 multitasking center offers fast tool changes compared to a full tool spindle ATC machine. A large tool capacity, up to 54 tool stations for turning and 24 tool stations for milling tools, reduces setup time. For faster cycle times, the new NTJ-100 has two high rigidity turrets, each with a Y-axis, 3.5 inches (80mm) on the upper and 2.6 inches (65mm) on the lower, facilitating pinch turn and pinch mill operations. An upper turret swiveling B-Axis with a range of 182 degrees is ideal for easily producing angular features, eliminating the requirement for expensive angle milling heads.
"The NTJ-100 is well positioned to serve a variety of industries including medical where angular features are found on components such as hip cups and bone plates," said Richard Parenteau, Director of Application Development at Methods Machine Tools. "Also for example, special aerospace fuel fittings and control valves have many angled aspects which are an excellent fit for this machine."
Two milling-tool motors, each at 9.5/3 HP can double the performance compared to traditional multitasking centers. Twin 6,000-rpm spindles offer fast motor acceleration and deceleration to improve machining efficiency. Synchronization of the left and right C-Axes is offered for parts simultaneously clamped by the left and right side chucks. The NTJ-100 has a maximum turning diameter of 6.9 inches (175mm), a maximum turning length of 26.7 inches (678mm) and a standard 1.6 inches (42mm)/maximum 2.6 inches (65mm) bar capacity.
The new NTJ-100 provides X-Axis and Z-Axis speeds of 787 ipm and 1,574 ipm respectively. Designed with a minimum 7.9 inches (200mm) and maximum 35.8 inches (910mm) distance between spindles to eliminate any interference of tooling during multitasking, the NTJ-100 allows for multiple tools in the cut simultaneously.
To ensure rugged, stable performance, the machine weighs 22,046 lbs. (10,000 Kg). The NTJ-100 has a small footprint to maximize floor space of 149.6 inches (3,799mm) length x 78.7 inches (2,100mm) width.
For ease-of-operation, the NTJ-100 features a large 19" high-resolution, touch screen LCD panel. The Nakamura-Tome Intelligent Programming System (NT-IPS) is a PC-based control that is built into the machine. It works in conjunction with the latest Fanuc 31iB-2 controller to give a high degree of functionality, coupled with fast processing speeds. New standard functions include a spindle speed override switch, a program number search, C-axis synchronization and helical interpolation.
CAMplete TruePath Turn/Mill software is standard on Nakamura-Tome Multitasking Turning Centers. CAMplete Turn/Mill software is an integrated suite of G-Code editing, optimization, analysis and verification tools, enabling a full range of turn/mill functions. Methods recently introduced Version 6.0 of this software which includes several upgrades for greater macro language support, improved error handling, increased post processing capabilities and more.
Contact Details
Related Glossary Terms
- centers
centers
Cone-shaped pins that support a workpiece by one or two ends during machining. The centers fit into holes drilled in the workpiece ends. Centers that turn with the workpiece are called “live” centers; those that do not are called “dead” centers.
- gang cutting ( milling)
gang cutting ( milling)
Machining with several cutters mounted on a single arbor, generally for simultaneous cutting.
- inches per minute ( ipm)
inches per minute ( ipm)
Value that refers to how far the workpiece or cutter advances linearly in 1 minute, defined as: ipm = ipt 5 number of effective teeth 5 rpm. Also known as the table feed or machine feed.
- interpolation
interpolation
Process of generating a sufficient number of positioning commands for the servomotors driving the machine tool so the path of the tool closely approximates the ideal path. See CNC, computer numerical control; NC, numerical control.
- milling
milling
Machining operation in which metal or other material is removed by applying power to a rotating cutter. In vertical milling, the cutting tool is mounted vertically on the spindle. In horizontal milling, the cutting tool is mounted horizontally, either directly on the spindle or on an arbor. Horizontal milling is further broken down into conventional milling, where the cutter rotates opposite the direction of feed, or “up” into the workpiece; and climb milling, where the cutter rotates in the direction of feed, or “down” into the workpiece. Milling operations include plane or surface milling, endmilling, facemilling, angle milling, form milling and profiling.
- milling machine ( mill)
milling machine ( mill)
Runs endmills and arbor-mounted milling cutters. Features include a head with a spindle that drives the cutters; a column, knee and table that provide motion in the three Cartesian axes; and a base that supports the components and houses the cutting-fluid pump and reservoir. The work is mounted on the table and fed into the rotating cutter or endmill to accomplish the milling steps; vertical milling machines also feed endmills into the work by means of a spindle-mounted quill. Models range from small manual machines to big bed-type and duplex mills. All take one of three basic forms: vertical, horizontal or convertible horizontal/vertical. Vertical machines may be knee-type (the table is mounted on a knee that can be elevated) or bed-type (the table is securely supported and only moves horizontally). In general, horizontal machines are bigger and more powerful, while vertical machines are lighter but more versatile and easier to set up and operate.
- turning
turning
Workpiece is held in a chuck, mounted on a face plate or secured between centers and rotated while a cutting tool, normally a single-point tool, is fed into it along its periphery or across its end or face. Takes the form of straight turning (cutting along the periphery of the workpiece); taper turning (creating a taper); step turning (turning different-size diameters on the same work); chamfering (beveling an edge or shoulder); facing (cutting on an end); turning threads (usually external but can be internal); roughing (high-volume metal removal); and finishing (final light cuts). Performed on lathes, turning centers, chucking machines, automatic screw machines and similar machines.