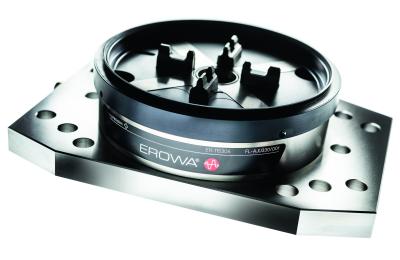
The EROWA PowerChuck P is the universal interface for quick and precise positioning of palletized workpieces or fixtures on a machine table. With the new PowerChuck Edge 20, the workpiece palletizing system has been updated with new, innovative design and functions.
Whether on milling or drilling machines, profile or surface grinding machines, or on the spindles of dividing heads and lathes, the EROWA PowerChuck P workpiece palletizing system is the most flexible and precise interface between machine and workpiece. The new PowerChuck P chucks and pallets are 100% compatible with the previous versions as well.
The 10,000 N clamping force in the PowerChuck P chuck guarantees a powerful and reliable hold during workpiece manufacturing. The compact, low profile design of the clamping system leaves plenty of room for workpieces and their machining.
Another beneficial aspect of the new PowerChuck P is the use of low-wear ceramic clamping balls. These guarantee consistent, low maintenance performance over a longer period of time over the previous clamping balls.
Lastly, like its predecessor, the new PowerChuck P workpiece palletizing system can be automated throughout. Sealing rings protect the chucks from waste and guarantee safe automatic loading.
Contact Details
Related Glossary Terms
- chuck
chuck
Workholding device that affixes to a mill, lathe or drill-press spindle. It holds a tool or workpiece by one end, allowing it to be rotated. May also be fitted to the machine table to hold a workpiece. Two or more adjustable jaws actually hold the tool or part. May be actuated manually, pneumatically, hydraulically or electrically. See collet.
- gang cutting ( milling)
gang cutting ( milling)
Machining with several cutters mounted on a single arbor, generally for simultaneous cutting.
- grinding
grinding
Machining operation in which material is removed from the workpiece by a powered abrasive wheel, stone, belt, paste, sheet, compound, slurry, etc. Takes various forms: surface grinding (creates flat and/or squared surfaces); cylindrical grinding (for external cylindrical and tapered shapes, fillets, undercuts, etc.); centerless grinding; chamfering; thread and form grinding; tool and cutter grinding; offhand grinding; lapping and polishing (grinding with extremely fine grits to create ultrasmooth surfaces); honing; and disc grinding.
- milling
milling
Machining operation in which metal or other material is removed by applying power to a rotating cutter. In vertical milling, the cutting tool is mounted vertically on the spindle. In horizontal milling, the cutting tool is mounted horizontally, either directly on the spindle or on an arbor. Horizontal milling is further broken down into conventional milling, where the cutter rotates opposite the direction of feed, or “up” into the workpiece; and climb milling, where the cutter rotates in the direction of feed, or “down” into the workpiece. Milling operations include plane or surface milling, endmilling, facemilling, angle milling, form milling and profiling.
- surface grinding
surface grinding
Machining of a flat, angled or contoured surface by passing a workpiece beneath a grinding wheel in a plane parallel to the grinding wheel spindle. See grinding.