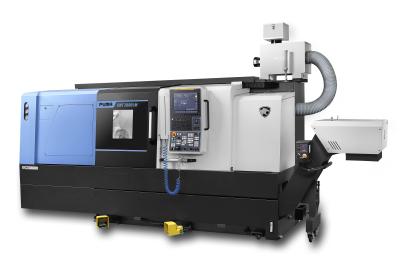
DN Solutions, a worldwide leader in the machine tool industry, introduces the new PUMA DNT 2100 and 2600. The DNT Series will replace the extremely popular PUMA GT 2100 and 2600 models. “The GT Series has been an international best-seller for a long time,” said Andy McNamara, Vice President of Sales and Marketing at DN Solutions America. “But we never stop looking for ways to upgrade our products and improve the machining experience of our customers.”
The PUMA DNT Series is equipped with the most powerful spindle in its class, a redesigned turret body and live tool drive that guarantee powerful and precise machining and exceptional productivity. The design of the new machines focuses on convenient operation and easy maintenance.
The upgrades on the DNT Series include features that separate it from its GT predecessors by way of enhanced rigidity, usability and accuracy.
Like the GT Series, box guideways are applied to all axes on the DNT Series to prevent vibration, ensure dynamic rigidity and deliver powerful and precise machining during heavy duty cutting. Rigidity enhancements on the DNT Series consist of an improved bed design, which includes increased guideway span and saddle width, a higher rigidity bearing arrangement in the main spindle and adoption of a high rigidity, low temperature live tool drive.
Convenience features on the DNT Series include an ergonomic control panel with adjustable height iHMI touch screen for quick and easy operation, a wider maintenance space and the addition of an inverter type chip converter with a 45∞ incline cover design for better chip handling.
The PUMA DNT Series improves on machining accuracy by optimizing the spindle structure and adopting the thermal compensation function (optional). A low heat generation bearing in the new live tool drive also help to minimize thermal deformation.
The DNT Series comes in a 2-axis and a milling version. Both have a 25 hp (18.6 kW) or 35 hp (26.1 kW) motor that turn the spindle at speeds ranging from 3,500 to 4,500 r/min.
Chuck sizes are also common to both configurations with a range of eight to twelve inches in diameter.
The maximum turning diameter of the 2-axis models is 15.7” (398.8 mm) to 18.1” (460 mm) and the maximum turning length is 21.6” (549 mm) to 42.4” (1077 mm). The milling versions come with a maximum turning diameter of 12.6” (320 mm) to 14.7” (373 mm). The maximum turning length is 19.7” (500 mm) to 40.5” (1029 mm). The BMT-55 live tooling turret has speed of 6,000 r/min powered by a 7.5 hp (5.6 kW) motor.
Options that add to the versatility of the DNT Series include a high torque spindle, servo tailstock, servo automatic door and others. For light automation, a parts conveyor and various bar feeders are offered.
“The PUMA DNT Series machines have the largest machining areas in their class and deliver maximum productivity with minimum cost,” McNamara said. “You won’t find a more comprehensive range or a better combination of value, performance and reliability anywhere else.”
Contact Details
Related Glossary Terms
- chuck
chuck
Workholding device that affixes to a mill, lathe or drill-press spindle. It holds a tool or workpiece by one end, allowing it to be rotated. May also be fitted to the machine table to hold a workpiece. Two or more adjustable jaws actually hold the tool or part. May be actuated manually, pneumatically, hydraulically or electrically. See collet.
- gang cutting ( milling)
gang cutting ( milling)
Machining with several cutters mounted on a single arbor, generally for simultaneous cutting.
- milling
milling
Machining operation in which metal or other material is removed by applying power to a rotating cutter. In vertical milling, the cutting tool is mounted vertically on the spindle. In horizontal milling, the cutting tool is mounted horizontally, either directly on the spindle or on an arbor. Horizontal milling is further broken down into conventional milling, where the cutter rotates opposite the direction of feed, or “up” into the workpiece; and climb milling, where the cutter rotates in the direction of feed, or “down” into the workpiece. Milling operations include plane or surface milling, endmilling, facemilling, angle milling, form milling and profiling.
- turning
turning
Workpiece is held in a chuck, mounted on a face plate or secured between centers and rotated while a cutting tool, normally a single-point tool, is fed into it along its periphery or across its end or face. Takes the form of straight turning (cutting along the periphery of the workpiece); taper turning (creating a taper); step turning (turning different-size diameters on the same work); chamfering (beveling an edge or shoulder); facing (cutting on an end); turning threads (usually external but can be internal); roughing (high-volume metal removal); and finishing (final light cuts). Performed on lathes, turning centers, chucking machines, automatic screw machines and similar machines.