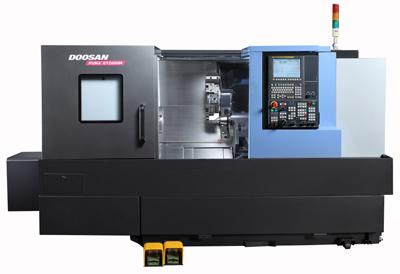
Doosan has expanded its range of Puma GT series turning centers with four new models: the Puma GT2600, GT2600M, GT2600L and GT2600LM. The family of four Puma GT2600 turning centers joins the Puma GT2100 and GT2100M, introduced in late 2013. Distinguishing features include a ridged 30-degree, single-piece, slant-bed design, box guideways, a fast non-lifting servo-driven turret and EZ Guide i Conversational Programming System.
Standard chuck size is 10" (optional 12" available) with a maximum swing over bed of 24.8" and swing over saddle of 18.1". Maximum turning length is 25.9" on the standard Puma GT2600; 24" for Puma GT2600M, while the long bed versions offer 42.4" on the Puma GT2600L and 40.6" on the Puma GT2600LM. The maximum bar working diameter is 3.2" on all four models.
Box guideways are applied to all axes to increase dampening and rigidity, providing the ideal platform for taking deep, powerful cuts. The Puma GT's 30° single-piece slant bed design reduces the center of gravity of both the spindle and cross slide by 12 percent, which minimizes thermal growth and improves operator ergonomics. Rapid travels: 945 ipm (X-axis) and 1181 ipm (Z-axis).
The spindle design features three angular ball bearings in the front and cylindrical roller bearings in the rear, minimizing thermal growth and increasing precision. An optimized spindle overhang design has minimized the rotational inertial load, enhanced rigidity, and reduced accel/decel time. Spindle motor, 30 hp. Maximum spindle speed, 3500 rpm. Maximum spindle torque 459 ft lbs.
Turret indexing times are fast on the Puma GT2600, due to a servo-driven non-lifting design, with a high torque motor. The new design is not only faster, it's more reliable, with 53 percent fewser moving parts. Number of tool stations is 12; size, 1.0 x 1.0"; maximum boring bar size, 2.0" for the Puma GT2600(L), 1.5" for the Puma GT2600M(LM); turret indexing time, 0.15 sec.
Puma GT2600M and GT2600LM feature a BMT55P top plate which secures each tool with four bolts and keys to provide powerful machining performance with high efficiency, high rigidity, and a high precision internal drive system. A bevel drive gear and air/oil cooling deliver low heat generation, minimizes thermal growth, while providing silent vibration free performance. Rotary tool speed is 5000 rpm with a 7.5 hp rotary tool motor.
The operating console features a Doosan-Fanuc i control with a large 10.4" color TFT LCD monitor with USB port, PCMCIA Card, embedded Ethernet connectivity, full QWERTY keypad and several single-touch Hot Keys to simplify set-up and operation. For added convenience, the pendant is designed to swing 88°.
Doosan's EZ Guide i is included as a standard feature, offering shop floor conversational type programing. Roughing, finishing, castings, grooving, threading, peck drilling and more are all accomplished through EZ Guide's menu driven functions. Programs are easily generated using cycles instead of long hand code.
Further, the new Puma GT2600 is easier to load. Distance from front cover to spindle center is reduced from 17.2 inches to 15.3 inches. And finally, for a machine with similar specifications, the new Puma GT2600 series are 14 to 25 percent more compact than the previous models. Cost of floor space does impact the hourly operating cost and, in many cases, shop floor real estate has become an important issue.
The Puma GT2600 guarding has been designed to provide easy access for adjustment, maintenance and service. The chip conveyor design bolts directly to the machine allowing the chip pan and coolant tank to slide out independently. This design eliminates coolant leakage and makes it easy to access and clean the tank. The tail stock guide ways on the new Puma GT2600 series are covered and fully protected from chips. This eliminates the ongoing cleanup time required on previous models.
Energy savings is achieved by using a 23 percent more efficient hydraulic unit. An LED work light is now being used which lasts 10 times longer than the previous halogen type and generates little heat. This helps to keep the work area a little cooler and thermally stable. LED lights also consume much less energy. Auto power off functions further reduce power consumption and heat.
Contact Details
Related Glossary Terms
- boring
boring
Enlarging a hole that already has been drilled or cored. Generally, it is an operation of truing the previously drilled hole with a single-point, lathe-type tool. Boring is essentially internal turning, in that usually a single-point cutting tool forms the internal shape. Some tools are available with two cutting edges to balance cutting forces.
- boring bar
boring bar
Essentially a cantilever beam that holds one or more cutting tools in position during a boring operation. Can be held stationary and moved axially while the workpiece revolves around it, or revolved and moved axially while the workpiece is held stationary, or a combination of these actions. Installed on milling, drilling and boring machines, as well as lathes and machining centers.
- centers
centers
Cone-shaped pins that support a workpiece by one or two ends during machining. The centers fit into holes drilled in the workpiece ends. Centers that turn with the workpiece are called “live” centers; those that do not are called “dead” centers.
- chuck
chuck
Workholding device that affixes to a mill, lathe or drill-press spindle. It holds a tool or workpiece by one end, allowing it to be rotated. May also be fitted to the machine table to hold a workpiece. Two or more adjustable jaws actually hold the tool or part. May be actuated manually, pneumatically, hydraulically or electrically. See collet.
- conversational programming
conversational programming
Method for using plain English to produce G-code file without knowing G-code in order to program CNC machines.
- coolant
coolant
Fluid that reduces temperature buildup at the tool/workpiece interface during machining. Normally takes the form of a liquid such as soluble or chemical mixtures (semisynthetic, synthetic) but can be pressurized air or other gas. Because of water’s ability to absorb great quantities of heat, it is widely used as a coolant and vehicle for various cutting compounds, with the water-to-compound ratio varying with the machining task. See cutting fluid; semisynthetic cutting fluid; soluble-oil cutting fluid; synthetic cutting fluid.
- grooving
grooving
Machining grooves and shallow channels. Example: grooving ball-bearing raceways. Typically performed by tools that are capable of light cuts at high feed rates. Imparts high-quality finish.
- inches per minute ( ipm)
inches per minute ( ipm)
Value that refers to how far the workpiece or cutter advances linearly in 1 minute, defined as: ipm = ipt 5 number of effective teeth 5 rpm. Also known as the table feed or machine feed.
- threading
threading
Process of both external (e.g., thread milling) and internal (e.g., tapping, thread milling) cutting, turning and rolling of threads into particular material. Standardized specifications are available to determine the desired results of the threading process. Numerous thread-series designations are written for specific applications. Threading often is performed on a lathe. Specifications such as thread height are critical in determining the strength of the threads. The material used is taken into consideration in determining the expected results of any particular application for that threaded piece. In external threading, a calculated depth is required as well as a particular angle to the cut. To perform internal threading, the exact diameter to bore the hole is critical before threading. The threads are distinguished from one another by the amount of tolerance and/or allowance that is specified. See turning.
- turning
turning
Workpiece is held in a chuck, mounted on a face plate or secured between centers and rotated while a cutting tool, normally a single-point tool, is fed into it along its periphery or across its end or face. Takes the form of straight turning (cutting along the periphery of the workpiece); taper turning (creating a taper); step turning (turning different-size diameters on the same work); chamfering (beveling an edge or shoulder); facing (cutting on an end); turning threads (usually external but can be internal); roughing (high-volume metal removal); and finishing (final light cuts). Performed on lathes, turning centers, chucking machines, automatic screw machines and similar machines.