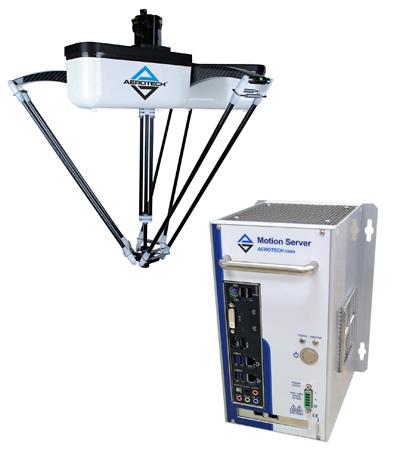
The RCP-DELTA from Aerotech Inc. is available in four models that support payloads up to 3 kg, with X/Y operating ranges of 500/800/1100/1300mm, and an optional continuous rotation about the Z-axis (yaw). Extensive use of carbon fiber and lightweight aluminum results in a robot that is capable of sustaining 200 pick-and-place operations per minute with peak acceleration on the order of 15g. With absolute encoders on each motor the robot never has to be referenced, even after a loss of power.
The RCP-DELTA control system is based on Aerotech's A3200 Machine Controller. The A3200's networked, distributed architecture provides a scalable platform upon which additional robots, I/O, and positioning devices can be integrated easily. Multiple programming interfaces provide deployment flexibility by allowing developers to work in the environment that matches their skill sets or application requirements. External sensors are supported with industry standard fieldbuses (EtherCAT, Modbus TCP, Ethernet/IP, and others) or applications operating in the RCP-DELTA's real-time enabled Windows operating system.
IP65 protection is standard (sealed against dust and low-pressure water jets) and IP69K (sealed against dust and close-range high pressure and high temperature spray) is available for applications where periodic cleaning with high-pressure water and/or steam is required.
The RCP-DELTA supports all standard A3200 programming and control capabilities such as multi-block look-ahead, corner rounding, and command shaping. Additional Delta robot specific functions are included for common robotic operations such as target queues, tracking moving material, and teaching tool/part locations.
Contact Details
Related Glossary Terms
- look-ahead
look-ahead
CNC feature that evaluates many data blocks ahead of the cutting tool’s location to adjust the machining parameters to prevent gouges. This occurs when the feed rate is too high to stop the cutting tool within the required distance, resulting in an overshoot of the tool’s projected path. Ideally, look-ahead should be dynamic, varying the distance and number of program blocks based on the part profile and the desired feed rate.
- shaping
shaping
Using a shaper primarily to produce flat surfaces in horizontal, vertical or angular planes. It can also include the machining of curved surfaces, helixes, serrations and special work involving odd and irregular shapes. Often used for prototype or short-run manufacturing to eliminate the need for expensive special tooling or processes.