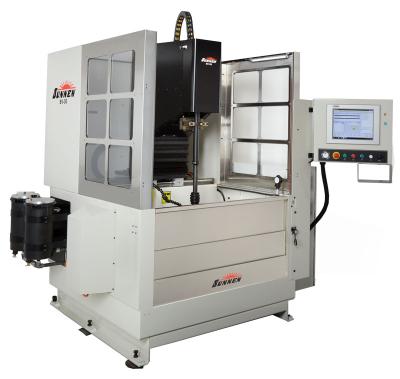
The new Sunnen SV-30 honing series is the next generation in the line of Cylinder King machines. True to its heritage, it achieves expert results on engine cylinder blocks, cylinder liners and other engine parts that require honing. Six standard models include four step-and-repeat capability versions allowing automatic bore-to-bore processing for in-line and V-block configurations, reducing setup time and improving bore quality.
In addition, two models are available with a manual X-axis. The SV-30’s cylinder diameter range is 0.75 to 8.0 in. (19 to 200 mm) depending on the tooling option, and the new Sunnen GH-LF tooling is required for automatic step-and- repeat operation.
With six new models in the series, the SV-30 can be tailored to meet the needs of manufacturers, job shops and automotive performance and rebuild shops. It includes a new PC control with simplified menus and storage for 1000+ setups for quick and easy changeovers. When used with the wide range of Sunnen-made abrasives, tooling and coolants, the U.S.-built SV-30 produces ideal bore roundness and surface finish in a variety of part types and materials at an affordable price.
The new SV-30 also includes spindle reversal, standard bore oversize setup (0.010”/0.020”/0.030”) and automatic tool protection at the top and bottom of the bore, which verifies an unobstructed stroke before starting a cycle. Models include either a variable-speed 6 hp (4.5 kW) servo or 5.5 hp (4.1-kW) induction spindle motor, producing speeds from 50-600 rpm. A 3.4 hp (2.5 kW) servo ball screw system produces up to 100 true vertical strokes per minute with a stroke travel of up to 27.75” (705 mm). The linear stroking drive maintains concentricity with the bore throughout the full stroke to produce a consistent diameter from top to bottom. A large, 48” x 30” (1219 mm x 760 mm) work envelope allows versatility in processing larger parts.
The new spindle reversal feature duplicates the capabilities of machines used by automotive OEMs. "Reversal can be used anytime in the process, but is especially helpful during the finishing strokes," said Phil Hanna, Sunnen product manager. "Reversal helps create a slightly rounder bore and aids in achieving the desired surface finish. It causes the honing stones to take out any less-than-round shape left after initial passes, while shaping up and dressing the stones themselves. Reversing the spindle also aids in removing folded-over metal and cleaning debris out of the valleys of the surface finish."
The Phoenix industrial PC control ensures automatic, consistent bore-to-bore geometry and finish, without constant adjustment by the operator. The 15-inch (381 mm) color touchscreen with intuitive controls provides a real-time display of the full-bore cross section during the process. The control can store 1,000-plus part setup programs, and a USB port allows offline setup file storage. The control's programmable Auto-Dwell feature automatically corrects taper anywhere in the bore for unattended operation, while two-stage honing tools with diamond or CBN abrasives can complete roughing and finishing operations in one pass for high productivity.
Left/right positioning of the honing column on its 32-inch X-axis (813 mm) is easily accomplished with a servomotor or a manual hand wheel located immediately below the operator station (model dependent). The machine is equipped with a 55-gallon (208-liter) internal coolant system with two standard steel canister cartridge filters, heavy-duty pump, and filter status gauge.
In addition to the GH-LF tooling (required for automatic step and repeat operation), the SV-30 is compatible with all of Sunnen's current large diameter tooling. This includes diamond abrasive hone heads and brushes, GHSS single-stage hone heads with CBN or diamond abrasives and brushes, and GHTS hone heads for two-stage honing with CBN or diamond abrasives.
The SV-30 is equipped with new standard LED lighting in the work envelope. It also has the latest standard safety features including light curtain, interlocked front door, stainless guarding around the work envelope, and safety PLC which limits setup speeds in all axes. Options include a T-slot base (for custom fixturing), heavy-duty manual rollover cradle for engine blocks, and a full-feature automation interface.
Contact Details
Related Glossary Terms
- V-block
V-block
Workholding device with V-shaped slot for holding pipe and other round stock during machining or inspection.
- abrasive
abrasive
Substance used for grinding, honing, lapping, superfinishing and polishing. Examples include garnet, emery, corundum, silicon carbide, cubic boron nitride and diamond in various grit sizes.
- coolant
coolant
Fluid that reduces temperature buildup at the tool/workpiece interface during machining. Normally takes the form of a liquid such as soluble or chemical mixtures (semisynthetic, synthetic) but can be pressurized air or other gas. Because of water’s ability to absorb great quantities of heat, it is widely used as a coolant and vehicle for various cutting compounds, with the water-to-compound ratio varying with the machining task. See cutting fluid; semisynthetic cutting fluid; soluble-oil cutting fluid; synthetic cutting fluid.
- cubic boron nitride ( CBN)
cubic boron nitride ( CBN)
Crystal manufactured from boron nitride under high pressure and temperature. Used to cut hard-to-machine ferrous and nickel-base materials up to 70 HRC. Second hardest material after diamond. See superabrasive tools.
- dressing
dressing
Removal of undesirable materials from “loaded” grinding wheels using a single- or multi-point diamond or other tool. The process also exposes unused, sharp abrasive points. See loading; truing.
- shaping
shaping
Using a shaper primarily to produce flat surfaces in horizontal, vertical or angular planes. It can also include the machining of curved surfaces, helixes, serrations and special work involving odd and irregular shapes. Often used for prototype or short-run manufacturing to eliminate the need for expensive special tooling or processes.
- work envelope
work envelope
Cube, sphere, cylinder or other physical space within which the cutting tool is capable of reaching.