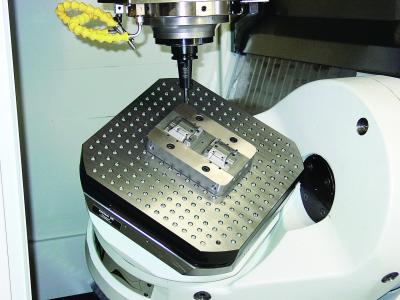
The System 3R Delphin Zero Point system from GF Machining Solutions provides an affordable clamping system for use during heavy milling operations on a variety of machine tools. With the Delphin system, manufacturers can increase their overall productivity by streamlining setups and reducing machine idle time.
The System 3R Delphin system has been optimized to handle any type of machine tool including those with T-Slot or grid pattern tables, as well as machines with pallet changers. Its robust design features flexible references to allow quick implementation of existing fixtures and pallets, which provides economic and productivity advantages, according to the company. By minimizing the distance between the connection’s reference surfaces and the workpiece to be machined, the mounting is more stable enabling operators to use the highest cutting rates.
The Delphin System offers the highest clamping force on the market at 60,000N per chuck face, with an accuracy of 5 microns in even the most challenging of conditions. It is available in pneumatic and hydraulic operating systems for a variety of machine tools to enable the machining of various sized workpieces, and for easy automation adaptation.
Contact Details
Related Glossary Terms
- chuck
chuck
Workholding device that affixes to a mill, lathe or drill-press spindle. It holds a tool or workpiece by one end, allowing it to be rotated. May also be fitted to the machine table to hold a workpiece. Two or more adjustable jaws actually hold the tool or part. May be actuated manually, pneumatically, hydraulically or electrically. See collet.
- gang cutting ( milling)
gang cutting ( milling)
Machining with several cutters mounted on a single arbor, generally for simultaneous cutting.
- milling
milling
Machining operation in which metal or other material is removed by applying power to a rotating cutter. In vertical milling, the cutting tool is mounted vertically on the spindle. In horizontal milling, the cutting tool is mounted horizontally, either directly on the spindle or on an arbor. Horizontal milling is further broken down into conventional milling, where the cutter rotates opposite the direction of feed, or “up” into the workpiece; and climb milling, where the cutter rotates in the direction of feed, or “down” into the workpiece. Milling operations include plane or surface milling, endmilling, facemilling, angle milling, form milling and profiling.