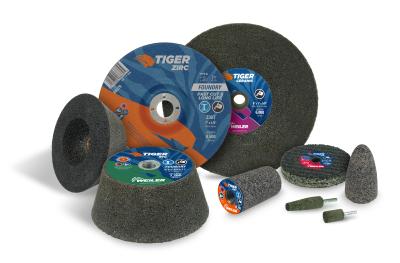
Weiler Abrasives, a leading provider of abrasives, power brushes and maintenance products for surface conditioning, announced the availability of its Tiger® abrasives line designed to deliver maximum performance in the most demanding foundry applications. With solutions to address all grinding applications in the cleaning room, Tiger products help decrease cycle times and improve operator experience.
“It’s common for the cleaning room to be a bottleneck in production. We’re excited to bring products to the market that will increase efficiencies and help foundries keep up with increasing demand,” says Kyle Thompson, technical product manager, High Volume Production, Weiler Abrasives. “This comprehensive portfolio encompasses the full breadth of off-hand products used in this market — so there is a productivity-enhancing solution for every job.”
Tiger Type 11 Cups
The Tiger Type 11 cup wheels are available with industry-exclusive ceramic grain technology to deliver up to 30% faster cut-rate compared to competitive zirconia cups. The advanced micro-structure of the Tiger Ceramic grain results in extremely low specific cutting energy, providing ultra-high metal removal rates to improve productivity when grinding cast and ductile iron, cast steel and other hard-to-grind materials. Tiger cup wheels are available with multiple grain technologies: Tiger Zirc for fast and consistent metal removal; Tiger SiC for controlled cut-rate on sand castings with burnt-in sand; and Tiger AO for consistent performance on cast iron.
Each of the Tiger Foundry cup wheels includes a unique anchored nut to secure the cup in place, increasing safety and preventing product breakage. Testing shows that this feature provides up to three times higher torque holding strength and withstands double speed burst test ratings. The nut is zinc-plated to prevent oxidation, eliminate contamination and allow for easy spin-on and spin-off changeover. A precision-balanced cup design ensures smooth, vibration-free operation and reduces operator fatigue.
Tiger Type 27 Grinding Wheels
Weiler Abrasives is offering its Tiger Type 27 depressed center grinding wheels in three performance tiers specifically designed for foundry applications, including Tiger Ceramic for superior cut and long life. The ability to remove 40% more material over the wheel’s life compared to competitive zirconia products increases productivity and reduces abrasive usage. Tiger Zirc and Tiger AO grinding wheels are also available, providing cost-competitive material removal rates and extended product life.
Each of the wheels include advanced anti-chipping technology that eliminates uneven edge breakage and chipping. This innovation improves operator safety by reducing flying debris during grinding and it also eliminates the need to dress the wheel to regain a workable edge, providing longer wheel life and increased product consistency. The grinding wheels have a triple fiberglass reinforcement for added strength. A 5/8 inch 11 nutted metal hub option allows for quick spin-on and spin-off changeover and prevents cross-threading or sticking to spindle due to heat buildup. In addition to 1/4-inch grinding wheels, 1/8-inch combination wheels are also available to provide flexibility and efficiency when switching between cutting and grinding applications.
Additional abrasive solutions
As part of the Tiger abrasives portfolio, Weiler Abrasives has added cones and plugs for ID cleaning, edge beveling, cleaning castings in hard-to-reach areas and more. The products feature a hexagon nut with channels that secures the cones and plugs to the grinding tool to increase safety and prevent product breakage.
Tiger Type 1 reinforced portable snagging wheels in ceramic, zirconia and alumina oxide are also available for pneumatic straight grinders, high-frequency electric straight grinders and die grinders. The wheel shape features a narrow contact area that makes it well-suited for targeted heavy stock removal applications.
Weiler Abrasives rounds out its offering with the Tiger Zirc mounted points in a variety of shapes and sizes for precise cleaning and grinding of parts with hard-to-reach areas and complex geometries.
Contact Details
Related Glossary Terms
- abrasive
abrasive
Substance used for grinding, honing, lapping, superfinishing and polishing. Examples include garnet, emery, corundum, silicon carbide, cubic boron nitride and diamond in various grit sizes.
- fatigue
fatigue
Phenomenon leading to fracture under repeated or fluctuating stresses having a maximum value less than the tensile strength of the material. Fatigue fractures are progressive, beginning as minute cracks that grow under the action of the fluctuating stress.
- grinding
grinding
Machining operation in which material is removed from the workpiece by a powered abrasive wheel, stone, belt, paste, sheet, compound, slurry, etc. Takes various forms: surface grinding (creates flat and/or squared surfaces); cylindrical grinding (for external cylindrical and tapered shapes, fillets, undercuts, etc.); centerless grinding; chamfering; thread and form grinding; tool and cutter grinding; offhand grinding; lapping and polishing (grinding with extremely fine grits to create ultrasmooth surfaces); honing; and disc grinding.
- inner diameter ( ID)
inner diameter ( ID)
Dimension that defines the inside diameter of a cavity or hole. See OD, outer diameter.